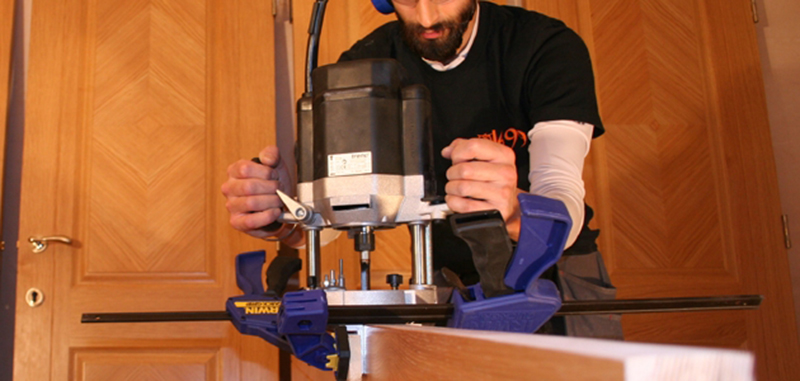
Tibby Singh Chodha tests the Trend Adjustable Hinge Jig on site.
I recently had a task on my hands to fit 32 locks into white oak doors, thus 32 mortises and faceplate cut outs. With each door costing around £300 I had one chance and one chance only.
I would say I am more of a traditional tradesman – using a hammer and chisel. If anything goes wrong I am the one to blame and not the machine.
Initially, I was hesitant to use this lock jig on such expensive doors. So many things went through my mind – such as, having to set the jig up each time, setting the router up and accidentally scratching the doors.
I must confess the Trend jig and Trend router have won me over compared to a hammer and chisel. For one thing there is no need for all the marking out onto the door in the conventional way – you simply determine the centre of the lock case and half the thickness of the door.
The jig is made from a 12mm thick laminate, with sliding phenolic plastic plates and engraved sight lines. It was so quick and easy to set up with the help of the engraved markings and the makers have also highlighted the most common markings for the lock body widths at 16mm and 19mm.
Once I knew the position of the lock I then adjusted the jig to the correct mortise aperture. It was so quick and easy to set up with the help of the engraved markings, and, being engraved, you can guarantee they won’t fade away. The great thing is that an allowance has already been made on the jigs increment scale for the offset between the cutter and the guide bush.
This means there’s no need to work out any technical measurements. The jig comes with a clamp bar, which is screwed onto the jig to the thickness of the door. Don’t worry – this is easy to set because, on the back of the jig, there are also engraved markings allowing a set up for 35mm, 40mm, 44mm and 54mm door widths.
I suggest using wooden packers when clamping the jig on to the door to avoid any scratches.
I had all the mortises chopped out in half the time it would have taken with a chisel. In order to do the cut out for the face plates I then simply re-adjusted the jig to the required width and length of the face plate.
Markings are also engraved at most common face plate widths of 22.5mm and 25.4mm. A pair of setting gauges are provided to set the width accurately as a tolerance should not be left for the faceplate.
You may be thinking about the rounded corners of the recess, but Trend has already overcome this by producing a corner chisel which locates into the rounded corner of the routed recess.
With one square blow with the hammer the corner is squared.
For further information on Trend visit www.trend-uk.com