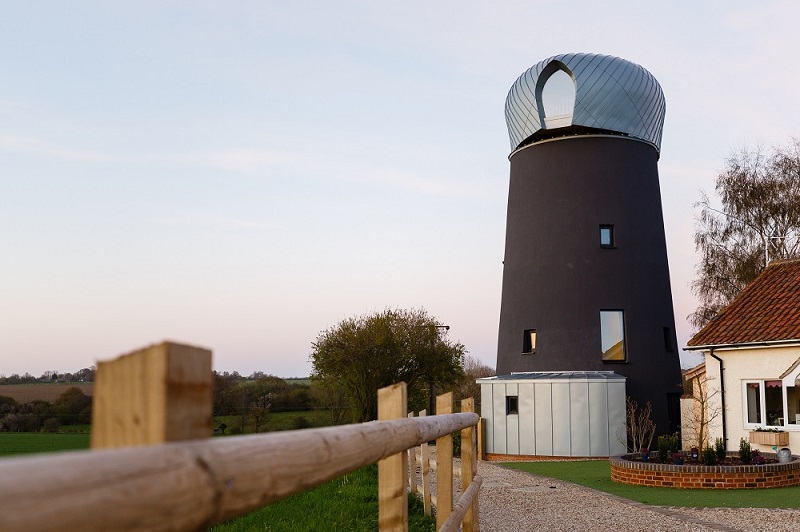
Professional Builder reports on a stunning windmill conversion using Kerto LVL Engineered Timber Solutions for Roof Systems.
Cockfield Windmill, situated in the heart of the Suffolk countryside, was a former windmill structure recently converted to accommodation for holiday lets. Before it was converted, the structure was just a mill stump constructed of brick with a traditional tar coating which no longer had its sails or cap.
Beech Architects were the architects involved in this interesting, yet challenging project, where the client wanted a new cap based on the traditional ‘inverted boat’ form, exploiting the stunning views over the Suffolk countryside.
Beech Architects contacted AJ Laminated Beams looking for a solution using engineered wood to create the curves for the cap of the windmill. AJ Laminated Beams, in turn, contacted Metsä Wood to see if Kerto LVL would be suitable.
Kerto is a laminated veneer lumber (LVL) product used in all types of construction. It is produced from 3mm thick rotary-peeled softwood veneers that are glued together to form a continuous sheet, which makes it incredibly strong and dimensionally stable. The product range includes both Kerto-S, generally used for beams, and Kerto-Q, generally used for roof decks etc.
Metsä Wood recommended the use of Kerto-Q to form the curved rib structure with each rib having a different shape and size to form the inverted boat. AJ Laminated Beams, first cut the arch shapes from the Kerto-Q sheets and then glued and screwed them together to form solid arches.
“The joints were designed with a mechanical fixing,” explains Mike Wells, owner of AJ Laminated Beams. “As an extra precaution, we glued the laminations together using Cascamite glue to give as much stiffness in each joint as possible.”
The cap with all its individual ribs was fully assembled in AJ Laminated Beams workshop, before being taken apart and making multiple deliveries to site to enable the components to be winched into place on-site.
Beech Architects looked at a number of solutions to the structure including steels and glulams but settled on Kerto as the best solution for the innovative shape and clients budget.
Kerto-Q panels were very well suited to this project because the panels could be cut easily to the shapes required and then once assembled, because the material is light, could be easily transported to site. Alternative solutions such as Glulam would not be suitable due to its lack of flexibility and fact that the product would be very expensive.
Mr Wells concludes: “It was not the most straight-forward project we have undertaken and the client and his installation team were extremely insightful on, at times, a testing project.”
For more information click here.