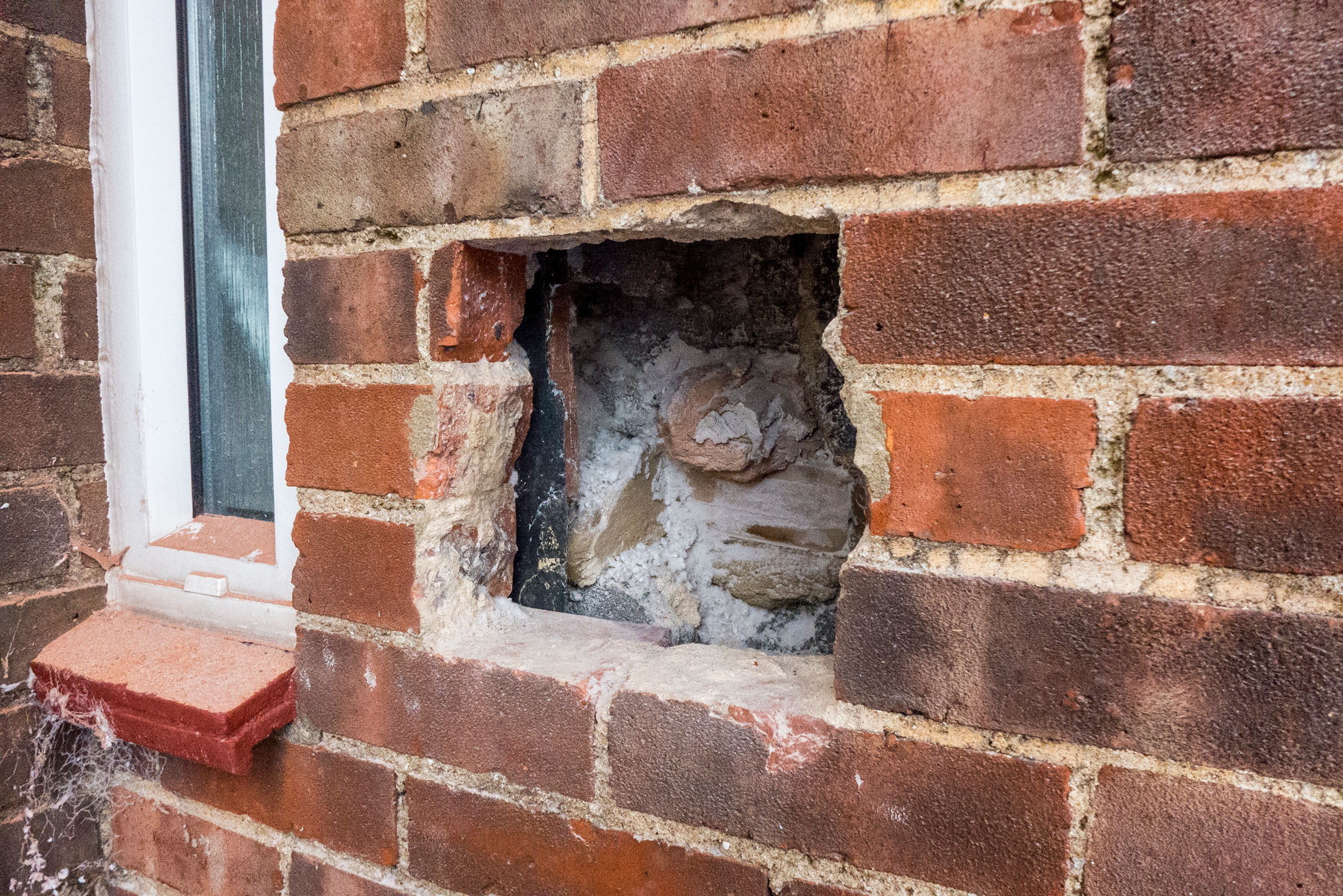
In the latest of its building defects series, Safeguard Europe looks at cavity wall insulation, the failure of which wrecks the energy performance of a wall – and worse.
With up to 35 per cent of heat loss in buildings occurring through the exterior walls, it’s not surprising that homeowners have looked for ways to improve the insulation properties of these walls. Cavity wall insulation has been the most popular solution to this problem in recent decades, due to the availability of government grants and non-intrusive installation.
If installed properly, cavity wall insulation can be a highly cost-effective insulation method. It is regularly used on new build properties in the form of cavity batts. However, as the number of homes treated has increased in recent years, there has been a noticeable increase in the number of homes where the installation of cavity wall insulation has led to damp problems occurring. In many cases, this has occurred because the external face of the cavity wall was in poor condition and therefore not suitable for filling with cavity wall insulation.
Different types of cavity wall insulation
Cavity wall insulation can come in many forms, such as: mineral fibre; polystyrene beads or urea formaldehyde foam. It is usually injected into the cavity of a wall using specialist equipment.
The insulation material itself is usually water-resistant. However, if the exterior masonry façade of the building the insulation has been installed on is not sound (i.e. large number of defects, porous brickwork, or degraded pointing) it can lead to moisture tracking through to the interior walls. Symptoms resulting from this penetrating moisture can include damp patches, blistering paint and mould growth.
Once moisture has tracked to the interior décor of a property, the cost of rectification can be significant. In particularly severe cases, where the insulation material itself has become damp, it would be necessary to completely remove the cavity wall insulation, at great cost, and redecorate the interior using a damp-resistant replastering method, such as the Dryzone Express Replastering System.
In situations where moisture has not compromised the insulation directly, but has just managed to track through to the interior, it should be possible to fix isolated exterior wall defects using a suitable repair mortar, such as the pre-mixed Stormdry XR Repair Mortar, and then weatherproof the wall using a breathable masonry waterproofer like Stormdry Masonry Protection Cream.
The colourless breathable coating will allow moisture within the building materials to evaporate and pass out of the wall as vapour but will stop the entry of more moisture in liquid form.
As the wall dries out on both the interior and exterior, the insulative properties of the cavity wall insulation will be restored and enhanced by the weatherproofer because dry building materials are more thermally resistant than wet building materials. Interior replastering can be carried out as needed using a suitably damp-resistant replastering method like the Dryzone Express Replastering System.
How to prevent cavity wall insulation failure
The best way to avoid the cost of cavity wall insulation failure is prevention. Fixing wall defects with Stormdry XR Repair Mortar and weatherproofing the wall with Stormdry Masonry Protection Cream, prior to the cavity wall insulation installation, will help prevent any moisture penetration and preserve the insulation.
For walls with significant networks of cracks, it is recommended to also use a crack-bridging waterproofer, such as Stormdry CB Crack-Bridging Coat, to provide extra protection.
If you suspect cavity wall insulation failure in a property, it should be inspected by a surveyor or company that specialises in dealing with such problems. Safeguard can provide details of such companies in your area.