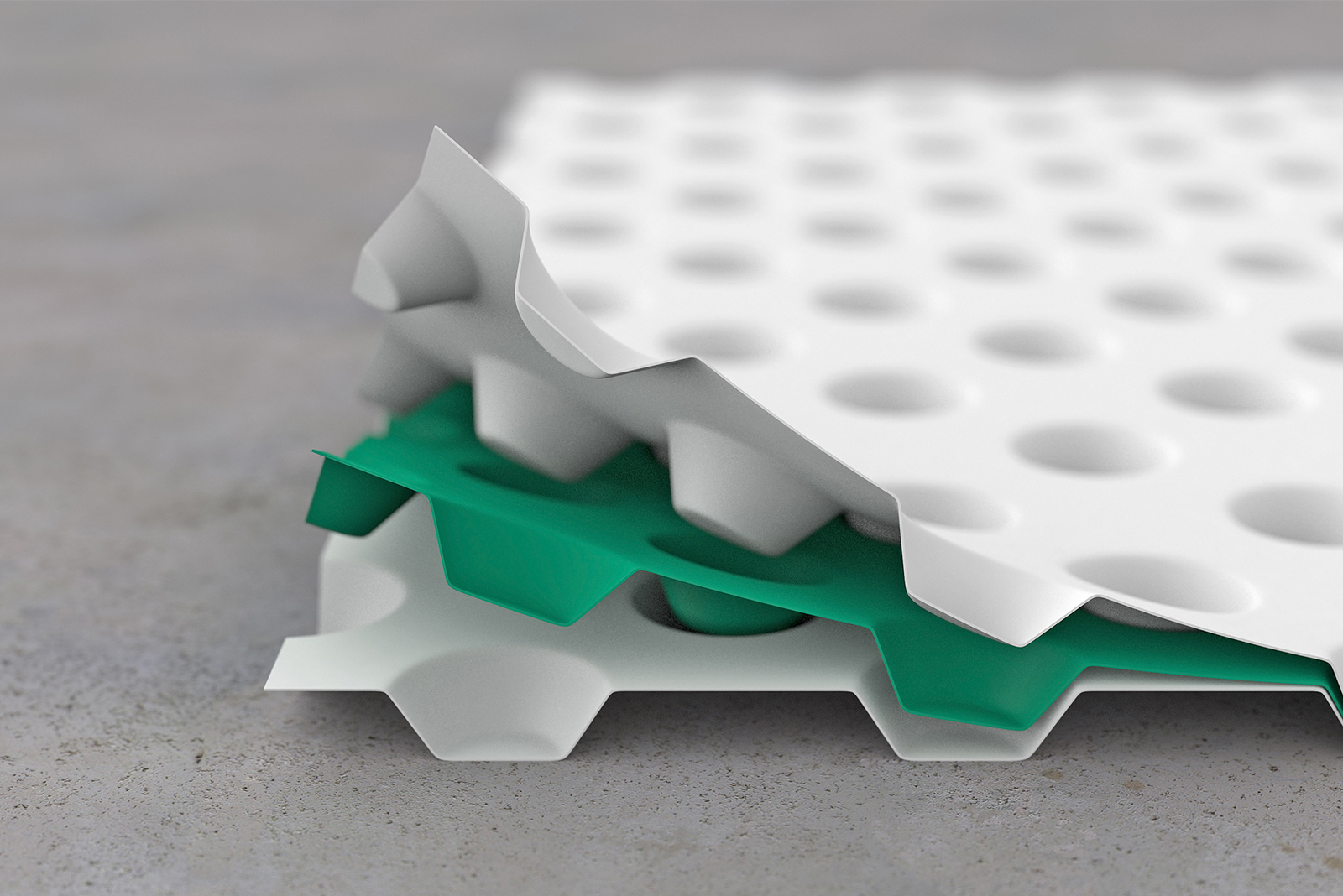
In recent years, sustainable and ethical construction techniques have become a main focus for the damp-proofing industry. Now, Safeguard Europe has upped its game by offering an award-winning ecologically-minded breed of cavity drainage membranes.
Under the Oldroyd Eco brand the membranes are created with an end-to-end process centred around dramatically reducing carbon footprint. To this end they are manufactured with the most modern procedures, transported with significantly reduced road miles and made of at least 60 per cent recycled plastic. It enables the company to justifiably claim that they are the most efficient cavity drainage membrane on the market in terms of workability, practicality, and environmental impact.
The product itself is an opaque studded cavity drainage membrane designed to manage the passage of moisture away from decorative surfaces on damp or contaminated internal walls and floors. As part of the commitment to environmentally friendly production techniques, the Oldroyd Eco range was launched to manufacture standard cavity drainage membranes with up to 100 per cent renewable energy. Embedded within its multi-layer technology also lies 60 per cent recycled plastic – but not the kind you would find from a typical two-litre Fanta bottle. In fact, Eco plastic is formed from discarded fishing nets, which otherwise would have been a hazard to marine life for centuries to come.
Around 30 per of the decline in some fish populations are a result from abandoned fishing equipment – and more than 70 per of marine life ensnarement is caused by discarded plastic fishing nets. By utilising these old and discarded nets the membranes gives new life to this seemingly purposeless plastic. Not only does it drastically reduce the amount of energy required to produce the membrane, but also helps to improve the condition of the marine environment.
This unconventional production process doesn’t detract from the product’s quality in any way, with the Multilayer-Technology (MLT) process allowing the use of 60 per cent recycled plastic without compromising the physical properties of the membrane. The recycled material is sandwiched between two white layers of virgin material via a heat-controlled polypropylene production process, which delivers highly consistent membrane thickness and density for uniform flexibility, without the “rucking” problems that plague lower quality membranes.
The melting and extrusion of plastic pellets to form these layers of virgin material comprise the most energy-consuming part of the membranes’ journey, introducing the highest embodied carbon per m². Fortunately, Oldroyd membranes are produced in Norway where 98 – 100 per cent of electricity comes from renewable resources (mainly hydroelectric power) – the embodied carbon from this stage is practically eliminated.
And, just to really take the foot out of the carbon footprint, Oldroyd located its new production facility close to a seaport. This means that the number of road miles required to reach export markets is significantly reduced. For the purposes of calculating embodied carbon, sea miles typically emit between 10 – 25 per cent of the amount of carbon emitted per road mile, meaning that Oldroyd membranes entail less CO² than domestically produced membranes.
The membranes can be applied in a range of projects, including indoor and outdoor environments, for both above-ground damp prevention and basement waterproofing. There are several basement waterproofing specification packs available that include Oldroyd Eco membranes for different waterproofing scenarios, including underpinning basements, piled wall basements, and new build reinforced concrete basements. It can be fixed to walls using special Brick Plugs with a compression seal. For application to floors, no fixings are generally required, however a screed or a floating timber floor can be applied on top.
In order to make the range of basement system designs easily accessible to contractors, Safeguard has created the Basement System Packs. These contain easy-to-understand technical illustrations, as well as key design considerations such as combining damp-proof courses with waterproofing systems. It also includes the relevant legislative requirements for each basement type, providing CAD drawings, NBS and CAWS clauses for both separate elements, and the complete system.
Safeguard also offers a number of training courses which delve into the specifics of applying membranes for both damp proofing and waterproofing scenarios. Find out more about these visit https://www.safeguardeurope.com/training-courses
To find out more about Safeguard Europe visit https://www.safeguardeurope.com/