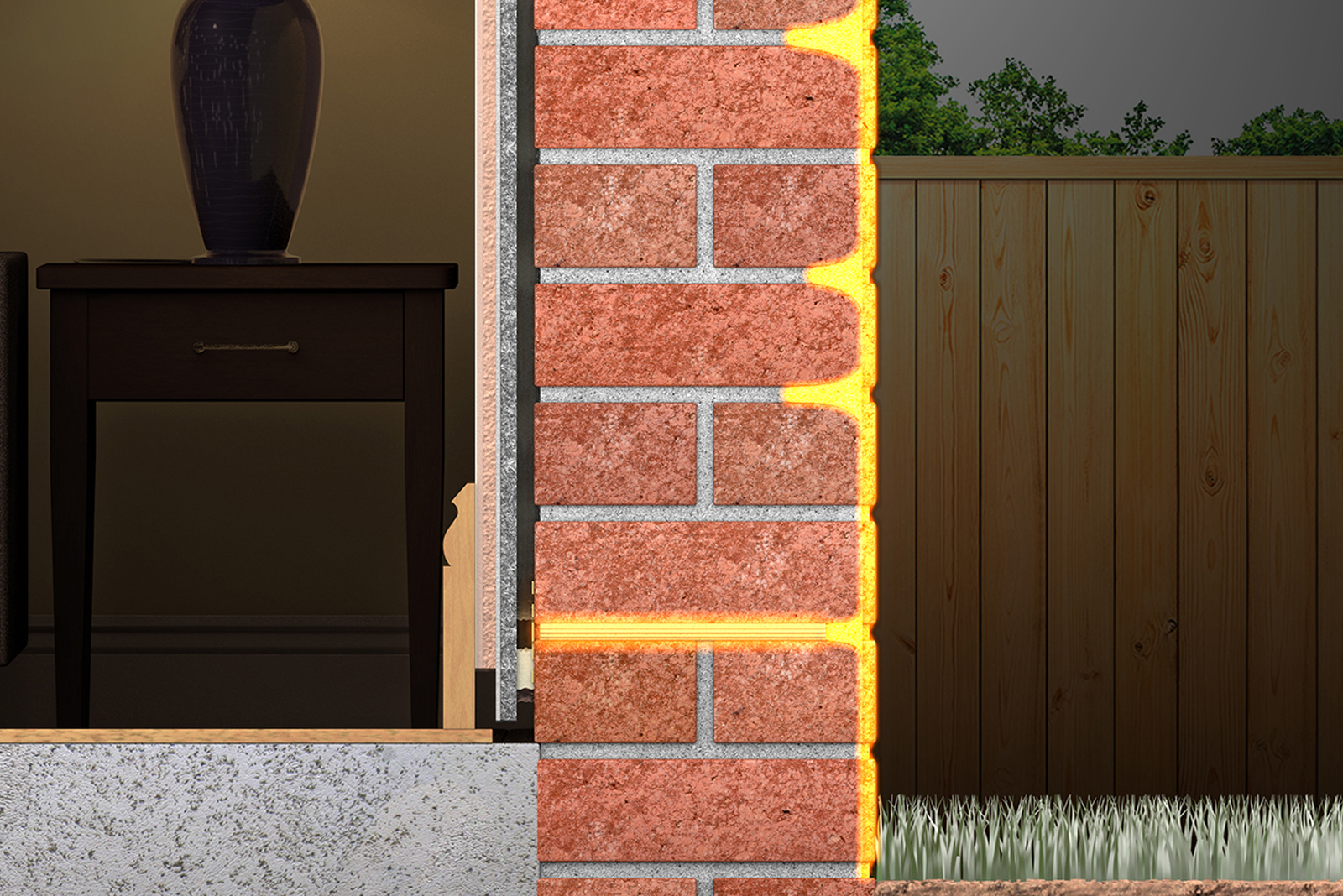
Hudson Lambert, director of Safeguard, outlines the best practice for internal wall insulation projects.
Lining walls with an insulation board or tile – Internal Wall Insulation – is an established and highly cost-effective means of improving the thermal performance of a wall and its building.
Although IWI is not the cheapest of the retrofit insulations, it is excellent value for money and brings three main benefits. Obviously, the first is the improvement in building energy efficiency. Second is the elimination of condensation, as wall surface temperature typically increases by several degrees centigrade.
Condensation is the most common form of domestic damp and promotes black mould growth, long-established as harmful to health by exacerbating asthma and causing other respiratory problems. Not only does IWI eliminate this problem, it also offers the third and final advantage to residents of providing significant reductions in space heating costs.
However, as with CWI and EWI, if IWI is improperly designed or installed, it has the potential to exacerbate or create damp problems in a wall, especially those caused by rising or penetrating damp. In these cases, moisture can be trapped behind the insulation material leading to mould growth, which will ultimately emerge into the house itself, or cause structural and decorative problems, such as rotten joists or failed plasterwork.
This is a concern at any time but is currently more pertinent in the face of the Government’s ambitions for its PAS 2035 retrofit programme. Having committed to making the UK a zero-carbon nation by 2050, there is then an urgent need to upgrade our existing housing stock. It has also been made more pressing by the introduction of the Green Homes Grant – now extended to March 2022 – which subsidises homeowners for up to two-thirds of the cost of insulation installations, capped at £5,000 per grant.
A significant proportion of the UK’s 28.6m properties has no insulation. Around 6m properties with cavity walls have no insulation and 7.7m homes with solid wall – or 91 per cent – have no wall insulation. In effect, every one of our 28.6m existing homes will need upgrading in some way to be net carbon zero by 2050 – as well as most homes being built today.
Penetrating damp
One major cause of IWI failure is penetrating damp. Many masonry materials – especially those used historically – are porous and if saturated, can result in damp problems. More often penetrating damp is a result of defects – either in craftsmanship or cracks, missing pointing, and poorly sealed doors and windows.
Remedying a rain penetration problem is therefore a question of identifying the defects that appear to be the most likely paths of moisture ingress and dealing with them. Repointing and sealing doors and windows properly are self-explanatory. Small cracks can be filled using special polymers, whilst larger cracks may require crack stitching using a system such as Safeguard’s BrickFix. In the case of larger cracks, the cause of the crack – e.g., subsidence – should be rectified.
Finally, porous brickwork can be waterproofed with the application of a colourless masonry water repellent – such as Safeguard’s Stormdry – that has been designed to reduce the permeability of masonry without affecting its appearance. Silane/siloxane based waterproofing creams like Stormdry penetrate much more deeply into masonry, providing longer lasting and more reliable protection against rain penetration, than older or weaker formulations.
Apart from helping to maintain the integrity of IWI, the application of a suitable masonry protection cream will also improve the thermal performance of the wall itself – dry walls being more thermally resistant than wet ones – augmenting the benefits of the IWI installation. One particular benefit of Stormdry is that it allows wet walls to dry out while preventing moisture getting in, so can be applied at any time of the year – although it shouldn’t be applied if rain is expected within 24 hours or in temperatures below 7oC.
Rising damp
Although rising damp is not the most widespread form of dampness affecting buildings, it is relatively common in older properties typically built without damp-proof courses (DPCs). It is usually treated by introducing a new damp-proof course into a wall to prevent any further ground water rising up the wall. The most practical and effective way of achieving this today is the introduction of damp-proofing rods into a mortar course at DPC level. The use of damp-proofing rods also guarantees that a consistent dose will be applied to each hole.
IWI technologies
Having fixed the fabric of the building ready for IWI, some consideration is due to the types of insulation material available.
Traditionally, standard internal wall insulation systems have been difficult to incorporate into smaller rooms such as bathrooms and kitchens – which are also the most condensation prone – owing to the reduction in floor space.
For this reason, low profile insulation systems have been designed. These are much thinner than standard IWI, meaning that while energy savings are not as great (although still significant); they are still able to raise surface temperatures enough to greatly reduce the risk of condensation occurring. These systems are less disruptive to install than standard IWI and can be used in situations where it wasn’t practical such as in staircases and small bathrooms.
And even more cost-effective solutions have subsequently appeared on the market. Aerogel insulation exhibits the lowest thermal conductivity of any material and have been engineered to create incredibly slim insulation, such as Stormdry EP board, which boosts a property’s U-value at a fraction of the cost and with far less disruption of other systems.
IWI presents a cost and space-effective chance to retrofit colder homes and is bound to see an increase in uptake between the PAS 2035 programme and the Green Homes Grant scheme. However, as with every retrofit insulation project, it is crucial to ensure the building fabric is fixed first so time and treasure aren’t wasted on installations with failure in-built.
For further information on Safeguard Europe visit https://www.safeguardeurope.com/