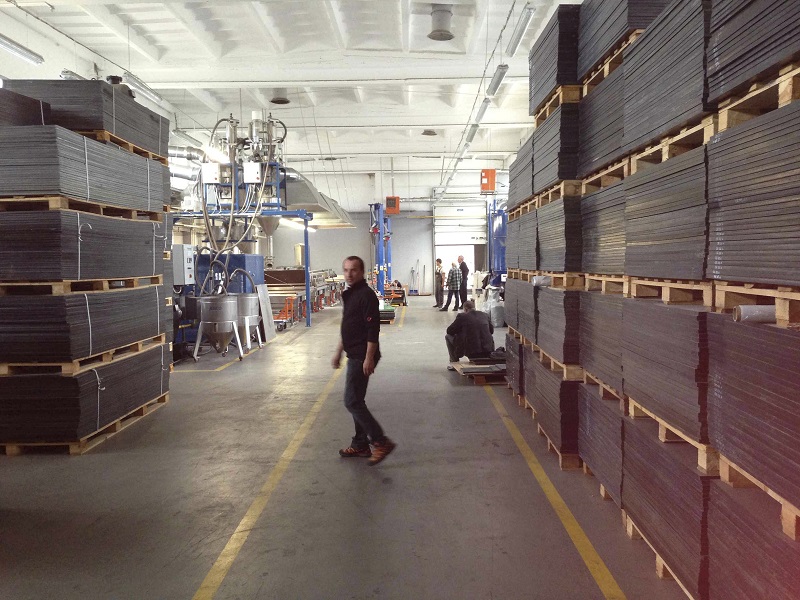
Professional Builder learns more about a new type of building board which is certain to whet the appetite of contractors.
“It’s not just about being eco-friendly, it’s about using a better product to build with, that will save you money and hassle,” says Nick Stillwell the man behind a new UK recycled plastic plywood replacement aimed at wet areas.
A manufacturing plant has been established in Frome, Somerset using waste plastic destined for UK landfill and diverting it into the manufacturing of a board which Nick is confident will quite literally go down a ‘storm’ with builders.
There are two types of board: the Storm Board HI (High Impact) and Storm Board SF (Shop Fitting). High Impact has a little more flex and can take hard use, Shop Fitting is more rigid and is used for finished products like furniture or indeed shop fitting.
The standard board is 19mm x 1,220mm x 2,440mm, and is a dark speckled grey colour. It is in fact sold in ‘oversize’, which means that the board is moulded larger than the finished size to allow for shrinkage during manufacture. The boards are strong but light, at under 30 kilos each, making them easy to manhandle around a build site.
Explains Nick: “Over many years Plywood has become the generic, go to sheet material in construction, but it does not perform well in the wet. It invariably needs sealing and/or painting, which is extra cost and time.
“Most plywood also contains formaldehyde, so it can’t be recycled or burnt for energy at the end of its use – it is simply landfill. Storm Board is 100 per cent recycled but also 100 per cent recyclable at end of life. This makes it ideal for short term out door uses.
“A typical application for Storm Board would be site hoardings. Generally cheaper plywood is used for this application, but it’s not so competitive once you have incurred the cost of painting, buying PVC sheet for the advertising and fixing it to the painted plywood.
“The whole lot is only good for landfill whilst Storm Board does not need to be painted, and you can stick vinyl graphics straight to it. At the end of use it can be stored outside and reused multiple times.
Adds Nick: “ Other applications for Storm Board Hi include tanking, as it can be glued and plastic welded, concrete shuttering jobs, public restrooms, gardens, sheds, animal enclosures and even emergency shelters.
“It is easy to wipe clean, water resistant, UV resistant, and more flexible than plywood, although you need to leave small expansion gaps for the board as it expands in heat unlike wood, which contracts.
“Storm Board SF is very stiff and is used in applications such as shop fitting, furniture, shelves and booths. It also makes very good outdoor weather proof chalk boards!
“Both HI and SF can be worked much like wood. They can be sawn with either hand or power tools in the same way as wood. We recommend tools not being set to too high a speed or you may experience some plastic melt on your blade. They can be routed and glued to create joints using plastic adhesives, and drilled and screwed, the plastic board acting much like its very own plug and gripping the screw,” he concludes.
For further information on Storm Board click here.