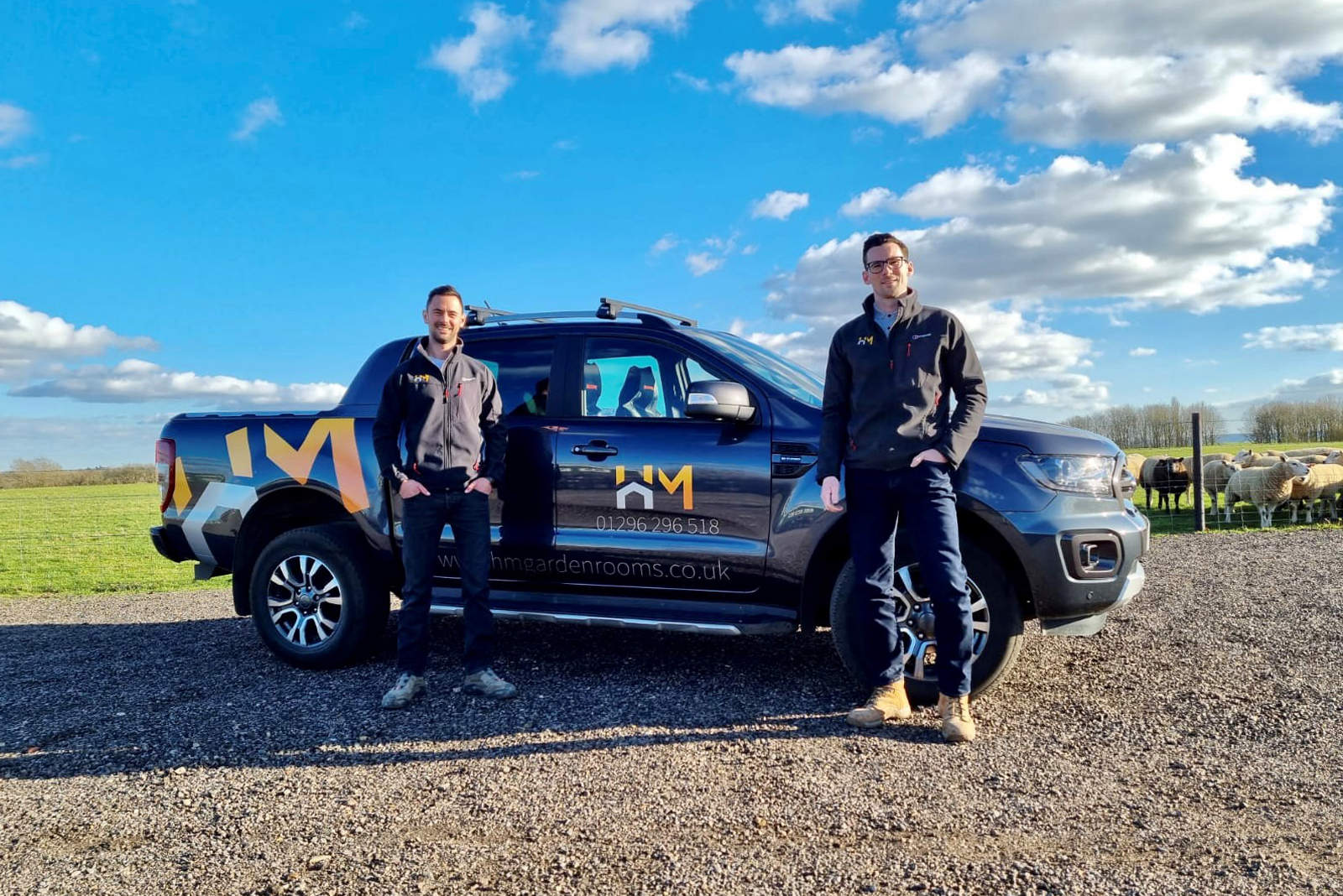
With garden room construction now a growing market, Professional Builder’s Lee Jones talks to two south east tradesmen who were quick to plant the seed of a new business.
Small building firms are amongst the most entrepreneurial that our economy can offer, which is not surprising given that the job itself is often a daily exercise in problem solving. Of course, all that ingenuity has been needed more than ever in the past year, but, as with every crisis, the pandemic has also brought its own opportunities. Confined to our domestic spaces, the prospect of improvement has suddenly piqued the interest of property owners, and the likes of home offices are now in hot demand. Two tradesmen who moved quickly to service that new-found need for a retreat are Jordan Hickson and Jordan Marsh of Buckinghamshire-based H M Garden Rooms.
“We set up the company in June of 2020,” explains Jordan Hickson, “and, to be honest, we were initially expecting to do maybe three builds in the first year, but the appetite for what we’re supplying has taken even us by surprise. In fact, we’re now approaching three times the turnover we initially projected.”
“We’ve been flat out,” adds Jordan Marsh, “and currently have four jobs in progress. For a lot of people, it’s not a question of an aspirational home improvement but a necessity, because they’re desperate for an environment that they can work in efficiently.”
A carpenter by trade, Jordan Hickson’s experience of Covid-19 is living proof that necessity is the mother of invention. Having been made redundant from his contract manager job near the beginning of lockdown, he and his business partner, Jordan Marsh – who was already the proprietor of a successful doors and windows firm in Marsh Glazing – realised that – in an age of working from home – a house would need to fulfil many more functions, and that’s what their garden room company is delivering.
“Our builds are a great way to rapidly add space, which can actually be put to any use and not just for an office” enthuses Jordan Hickson. “They can take as little as a couple of weeks to construct and, because they typically fall within current permitted developments rules, won’t need planning permission, which can cut out a lot of time and the likes of architect’s fees. When we’re socialising again, they will be areas for entertaining and to chill out, or for the more energetic they can be used as gyms and personal fitness studios.”
The first job the company secured was in Cumbria, and came through recommendation, but the two partners are largely operating in the home counties. Whatever the location, H M Garden Rooms promises a bespoke build that is suited to the client’s existing outdoor area and work closely with the client to tailor the room to their anticipated uses – but at an affordable price.
Jordan Marsh provides some detail on construction methods. “We use Ground Screws from Stop Digging because it removes the mess and major excavation work that’s associated with laying concrete foundations. They’re quicker, more environmentally friendly, suitable for soft or hard ground, and on any size of build. On those foundations we’ll then build a timber frame or make use of SIPS panels. In either instance we’re looking to deliver U-Values and a level of energy efficiency that is conducive to year-round use. These are not just sheds but structures that are designed to comply with Building Regulations, and that’s reflected in the quality of the materials we use.
“There’s a whole host of glazing options for doors and windows, mainly in either PVCu or aluminium, and bi-folds remain a popular choice. EPDM rubber roofing is the preferred option in a flat roof construction, and we find RubberCover by Firestone, supplied by Permaroof is the easiest to lay and gives the property owner the peace of mind of durable installation. Again, there are always plenty of options and a pitched roof with clay tiles is something a client can choose.”
In the Cumbria build the two Jordans made use of SterlingOSB Zero and that’s a material they’ve returned to again and again, as Jordan H explains. “SterlingOSB Zero is easier to use and lighter but just as strong as plywood. It’s also cheaper than ply and readily available so it ticks a lot of boxes for us”.
All of H M Garden Room’s buildings are clad in a variety of beautiful materials but Jordan has found that clients are increasingly asking for the SterlingOSB Zero to be left exposed on the interior as part of the design finish. “On the Cumbria job the client wanted the printed side of the OSB left bare inside their mud room as they really like the utilitarian feel of the material”.
“We’ve found that word of mouth has become our friend in generating work but have also advertised on Google and Facebook,” concludes Jordan Marsh. The team already run a successful building company in H M Contracting, which focuses on new build, refurbishment and structural alterations to the domestic residential market, and its new garden rooms venture compliments their existing business perfectly. “These kind of builds are so versatile that we see them continuing to be in demand way beyond the current Covid restrictions, and we’re certainly looking to scale up the business and build a brand that will proceed us.”
For further information on any of the companies mentioned in the this feature, see down below:
H M Garden Rooms https://www.hmgardenrooms.co.uk/
Norbord SterlingOSB Zero www.norbord.co.uk/
Stop Digging’s Ground Screw Foundation System https://stopdigging.co.uk/
Permaroof – RubberCover by Firestone https://www.permaroof.co.uk/