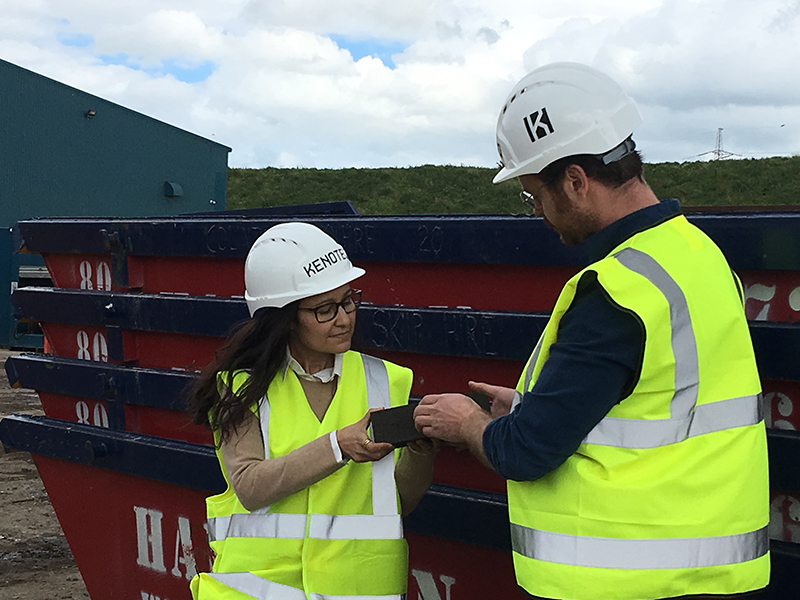
Professional Builder’s Lee Jones talks to the developer of the world’s first recycled brick.
If we are to continue along our present path many of the raw materials that we take for granted are either destined to become increasingly scarce resources, or environmentally insupportable. As we have reported previously, even sand could soon be in short supply, whilst all the stages of concrete production currently account for anywhere between 4 – 8 per cent of global CO2 emissions.
“If you look at the amount of virgin material we are still exploiting – and add to that the volume of waste we continue to generate– and it is clear that society is going to have a problem,” declares Professor Gabriela Modero. “That is the principle behind the K-Briq – it is the circular economy in action.”
First conceived as an idea some 10 years ago, civil and geotechnical engineering expert, Gabriela and her colleague Dr Sam Chapman, together with a team at Edinburgh’s Heriot Watt University, have since developed a brick made from 90 per cent recycled construction and demolition waste. It’s composed largely of concrete, brick and aggregate, and the product is now in commercial production through Kenoteq – a clean-tech spin off from Heriot-Watt that specialises in low-carbon building products.
Crucial to the lighter tread of its carbon footprint is that the K-Briq uses no cement, and does not require kiln firing. Instead the material is air dried, which means it is said to account for only 10 per cent of the CO2 emissions of a conventional clay brick. The process of manufacture is jealously guarded by Kenoteq, but it is a product that has already won plaudits, with a new pavilion at the Serpentine in London’s Hyde Park shortly to be built from K-Briq, and a number of other projects in the pipeline.
Continues Gabriela: “Commercially, this is a solution that will find favour with developers because there’s considerable flexibility in terms of colour, with a range of finishes available from recycled pigments. Not only that, but the quality of the brick, in terms of durability and longevity will also be apparent, whilst it also has a higher U-Value than its clay counterpart.”
Indeed, developers and the wider industry will increasingly need to demonstrate their environmental credentials to new and existing clients, and it’s not just in its thermal insulation properties that K-Briq can score points on sustainability. The Scottish government has equally set ambitious targets for housebuilding in the years ahead – with up to 50,000 new homes a year the current target and, given that the product will be produced north of the border, that means the energy miles in supplying those sites will be reduced.
Gabriela explains the development process: “We have the resources of a university at our disposal and, because we began in a controlled laboratory setting, we’ve been in the fortunate position that we could continuously and extensively test the product in-house to the building standards and beyond. What that process produced was a product that looks like a clay brick, and is roughly the same weight, but has a higher U Value. It’s also more breathable, which means it can contribute to keeping a property warm in the winter and cooler in the summer. Scaling the product up from a laboratory to a position where we are now producing thousands has been an interesting journey, but we’re now working towards BBA certification.”
For Kenoteq, however, this is just the beginning, and there are ambitious plans to introduce similar innovations: “The K-Briq is the first to enter the market, but we actually have a whole portfolio of products at different stages of development. They will be developed with the needs of the industry in mind, but equally along the same low carbon principles.” With investment in machinery that can produce up to 3 million bricks a year, the objective is to supply the builders’ merchant network, with a product that demonstrates the just what can be achieved from waste materials.