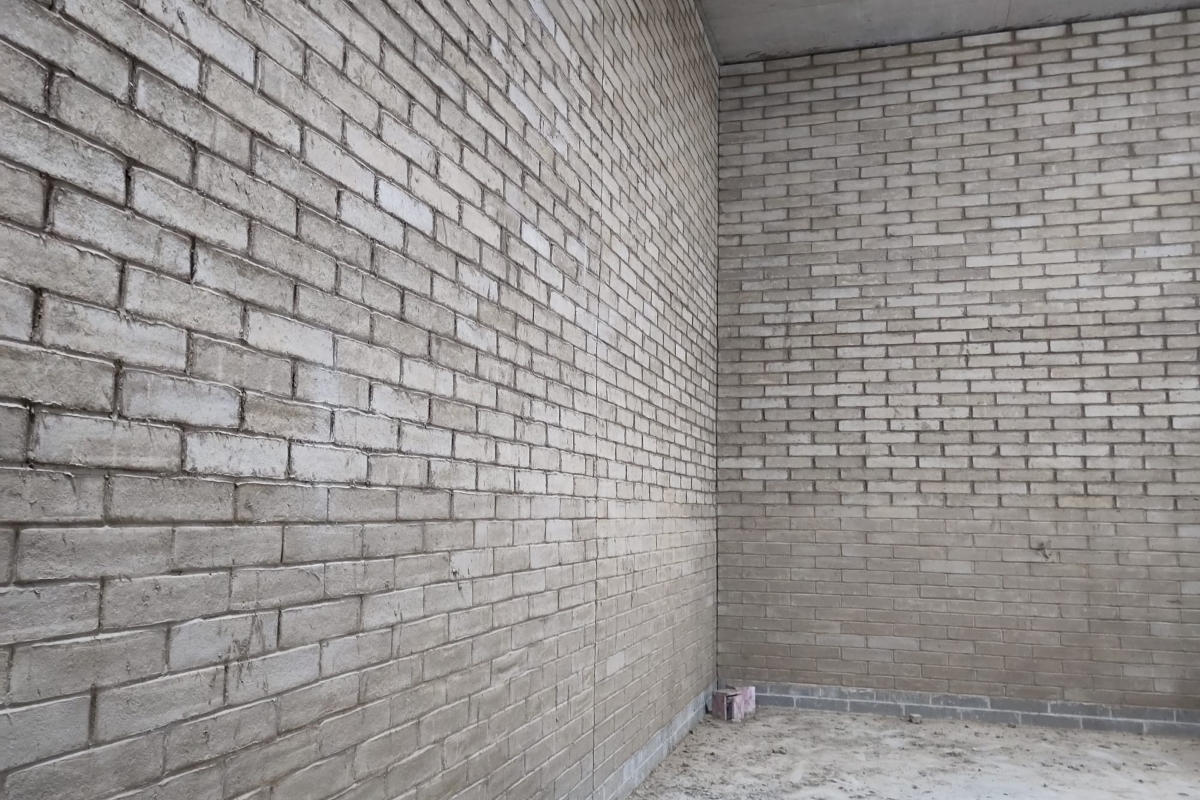
It’s clay time with the handmade brick specialist, H.G. Matthews, natural building blocks
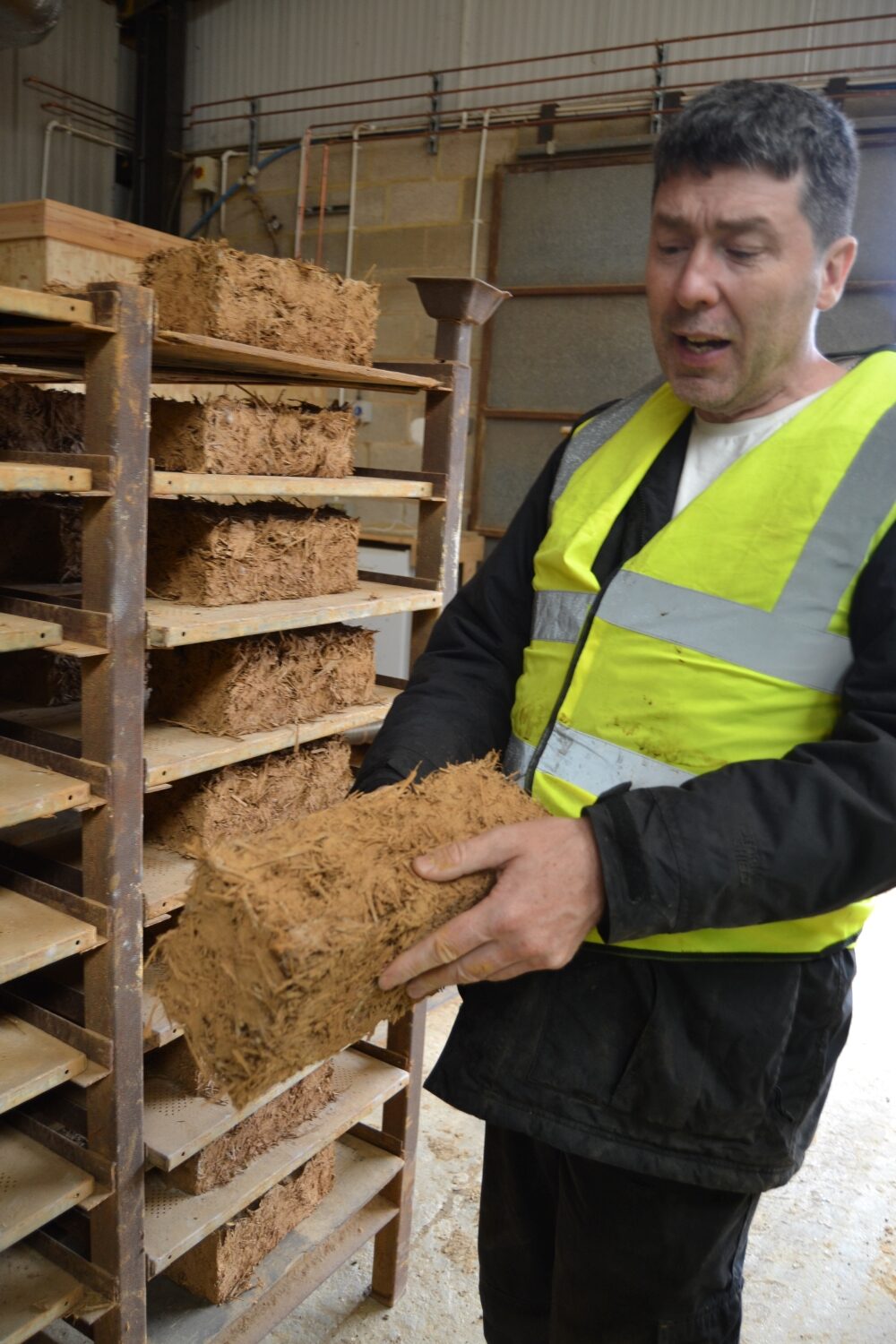
The rate at which we are using up the earth’s resources is accelerating at a worrying pace. We’re currently consuming 35 billion tonnes of sand, gravel and crushed rock for building, for example, a figure which is projected to reach 55 billion by 2060. At the same time, the cement industry is responsible for 8% of the world’s CO2 emissions. This has long been recognised as an unsustainable path, and the need to later course is now pressing. One handmade brick manufacturer thinks it’s done just that – and the solution is literally right beneath our very feet.
“Our approach has been two-fold”, enthuses Jim Matthews of Chesham-based H.G. Matthews. “We want to champion low carbon production techniques as well as sustainability in material resources. If you consider the latter point first what’s often not considered is the amount of virgin material used in construction.”
The H.G. Matthews answer is actually a return to a building material and technique that stretches back millennia. Indeed, the brick expert’s recipe can be found at the dawn of civilisation in the mud bricks of ancient Mesopotamia. Made from unfired clay, and wheat straw that act as a binder, H.G. Matthews’ Strocks are load-bearing natural building blocks that achieve a rating of 1.5Nm/mm2 which is more than enough for the loads in a one or two-storey property.
In the south of England clay is a ubiquitous substance but that doesn’t mean that all of it can be made into bricks. Only certain clays can cope with the stresses of being fired to over 1,000℃ but, when you’re eliminating the firing process entirely, any clay will do the job and you are presented with a superabundant material. That means the waste clay that H.G. Matthews routinely digs through to reach the consistency required for brick-making is now a useable commodity.
Not only that but, because it’s unfired, Strocks are using significantly lower levels of energy in their manufacture. Rainwater collected from the H.G. Matthews roof is used in the mix, and biomass boilers, fuelled by locally-sourced wood chips, take care of the drying. Moreover, a building made of Strocks is more breathable, thereby helping to regulate internal humidity in a home.
This then brings us to another ancient technique that suddenly finds a place in the modern world. If you’re digging out the foundations for a building, why landfill all that clay, and pay for the privilege? Instead, good use can be made of that earth by making blocks out of it, thereby effectively erecting a structure from the very ground on which it stands. This is exactly what Jim Matthews and his team have done and the results are impressive.
In order to demonstrate just what can be achieved with natural materials, H.G. Matthews was involved in the construction of a nursery close to its Buckinghamshire brickworks. Strocks were used in the inner cavity wall with wood-fired handmade bricks and lime mortar on the outer leaf, and hemp insulation in between. Glulam beams provided the structural integrity, and the building was finished with clay plasters and paints.
Since this project Strocks have also been used in a variety of applications, including the Apex Building for the Tribeca Development, King’s Cross, London.
Once a building like the above ultimately reaches the end of its useful life that’s not the end of the story either. A mix of clay, sand and straw can easily be reused, which makes an unfired block ideal for recycling.
Strocks are natural building blocks that can be used in the inner skin of an internal wall – where they will replace concrete blocks – or for outer walls that can then be clad in a sustainable building board. On the inside, a clay or lime plaster can be utilised, covered with a breathable paint. It’s easy to chase into the blocks with a multi-tool and fixings can be screwed into them in much the same way you would timber.
Subject to a two-hour fire test at over 1,000 degrees – as you would expect from clay – the material proved to be fire-proof. They can be laid exactly as you would any concrete block with the accompanying thin-bed clay mortar very easy to use – just spread the mortar on, put the blocks down and tap into place with a hammer.
“As far as we’re concerned the answer to producing a sustainable building block has been hiding in plain sight,” concludes Jim. “It’s the clay that’s all around us and has been used in various forms for thousands of years. It’s fully compatible with the demands of a circular economy and is a locally sourced solution. There’s a greatly reduced carbon footprint in manufacture, whilst there are real benefits for the occupiers of properties built with Strocks, particularly with regards to the moderation of moisture levels. In addition, the blocks demonstrate a very high thermal mass and density, which offers excellent insulative properties, keeping bills down in the winter. They’ll even absorb the harmful Volatile Organic Compounds (VOCs) that are found in modern homes. Put simply, clay and straw as building materials are still as good as it gets.”
For further information on H.G. Matthews Strocks natural building blocks visit Handmade bricks – HG Matthews Limited.