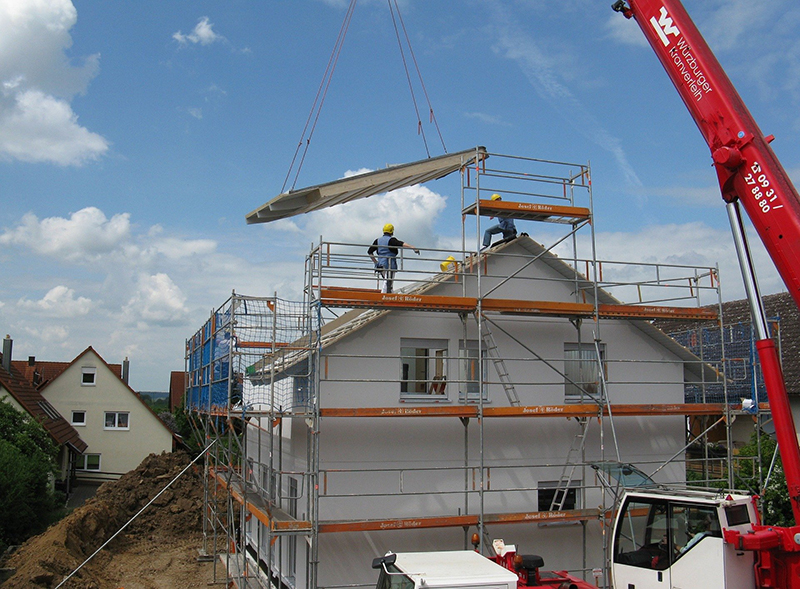
Nick Cowley, managing director at window and door manufacturer Euramax, looks at some of the differences between modular and traditional building methods.
The modern method of construction is defined as a way of working more effectively, to achieve more, while using less. This description lends itself heavily to offsite or modular construction techniques — the method of prefabricating parts of a building offsite, before transporting and assembling them at their final location.
Unlike traditional methods of linear construction, where the build is constructed onsite and each phase must be completed before the next one can proceed, a modular construction follows a less linear process.
The beginning
While modular construction methods are different to a traditionally constructed build, both processes have a similar starting point. Like all construction projects, a modular project must be planned and approved, the site must be prepared, and the foundation needs to be laid. It is at this stage that traditional and modular projects begin to differ.
Instead of waiting for foundations to be laid and set, modular construction can already get to work at an offsite prefabrication facility. Depending on the scale of the construction, modules can take up to four weeks to be manufactured. The ability to work on multiple phases of the project at the same time is not permitted with traditional construction, as the site preparation must be complete before next steps can be taken.
Next steps
As those working on modular projects can work on multiple aspects simultaneously, the construction can be completed quicker, saving time and money. In some cases, this can be as much as 50 per cent faster than a traditional construction project.
Once the foundation is prepared, the modules, which are manufactured on an assembly line, are shipped to site for assembly. The most common style of modules are manufactured from 2D panels, where four wall panels and ceiling panels are bolted together with screws. Depending on the desired building design and height, the modules can be stacked, laid or assembled in different ways to create the finished structure.
After the modules have been assembled onsite, final exterior finishes remain. Whereas electrical, plumbing and heating services must be installed onsite for a traditionally constructed build, these components can be fitted in the modules for a modular build. This increases the speed of completion and reduces delays.
Easy installation
One of the biggest differences of modular builds in comparison to traditional methods is their quality-controlled production environment. Manufacturing the modules offsite means that errors with quality can be resolved before assembly, streamlining the construction process. It also eliminates the chance of damage from vandalism and harsh weather conditions — factors that can cause disruption and increase the cost of traditional construction projects.
As quality is optimised, the process of installing fittings such as windows and doors also becomes smoother. For modular builds, specifications of windows and doors must be determined in the early stages of the project, otherwise inaccuracy can delay completion times, creating more work for the builders.
Windows and doors for modular builds must be manufactured to the same standard as windows and doors for a traditional build, but they must consider the specific requirements needed for a modular build. Euramax works closely with buying and specification teams to manufacture precise, high quality windows and doors for modular construction projects. Furthermore, Euramax products are rated A by The British Fenestration Ratings Council (BFRC), helping to improve the energy efficiency of the build.
It’s important to remember the history of brick and mortar construction and why it has been fundamental in the construction industry for many years. However, modular construction methods offer precision, time-saving and quality control that is difficult to obtain on a building site.
