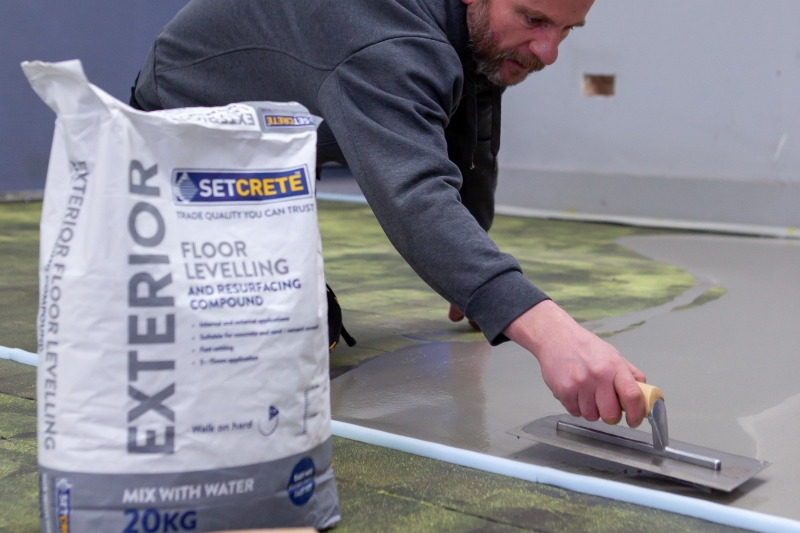
Peter Wilson brand manager for Setcrete floor levelling compounds explains how and why the preparation of the subfloor is essential in delivering the perfect flooring installation.
Before a floorcovering is installed, it is essential that the subfloor base is sound, dry and free from contaminants, such as oil, paint or old adhesive residues (left behind following the removal of a previous floorcovering). Inspection of the subfloor will quickly establish if the base is cracking or flaking, in which case the affected areas need to be treated or, in severe cases, removed and replaced.
Contamination is most likely on a conversion, especially if the space was previously used as a garage. If spillages or grease are present, these need to be removed mechanically, for example, using a grinder. With a new screed, there is often a thin surface film or crust formed by a mixture of water, cement and fine screed particles that dries out and settles on the surface as the screed cures. Known as laitance, this thin crust must be removed before proceeding.
Dealing with damp
Excess subfloor moisture is the biggest cause of flooring failure bar none. In older properties it is usually caused by the absence of a damp proof course (which only became mandatory in the 1960s) or by water ingress for outside. In newer buildings it is mainly the result of residual construction moisture, with a typical subfloor screed requiring around one day per millimetre of depth to fully dry out.
If left unchecked and untreated before a floorcovering is installed, this moisture will rise to the surface of the subfloor where it will attack adhesives used to install the floorcovering and damage the floorcovering itself. This can, for example, cause vinyl tiles to lift and wooden floors to warp and promote harmful mould growth.
It is not possible to ascertain the degree of subfloor moisture by touch or smell. The only reliable way of testing for it is by using a handheld moisture meter or, preferably a digital hygrometer. If the moisture level is above 75% relative humidity (RH), or 65% if a wood floor is to be installed, a remedial treatment is required.
Fortunately, these are readily available and quick to apply. A high-performance liquid, epoxy-based rapid set DPM system requires only a single application and will cure in around three hours, providing protection up to 98% RH.
Once the subfloor has been tested for moisture and, if required, a DPM has been applied, it is ready to received a levelling compound to create a super smooth surface that will optimise the appearance of the floorcovering.
Smooth work
Often subfloor screeds are not super smooth and a levelling compound should be applied before any floorcovering is installed. This is particularly important for thin, resilient floorcoverings, such as luxury vinyl tiles (LVTs), where even the smallest blemish in the subfloor will show though the floorcovering and compromise its finished appearance.
If the subfloor is a standard sand/cement screed, a general-purpose levelling compound should be OK to use, but sometimes a specialist levelling compound is required. For example, if time is tight, fast-track levelling compounds are available, which are ‘walk on’ hard after just 30 minutes and ready to receive a floorcovering in as little as two hours.
Alternatively, if an extension subfloor has been installed at a significantly different level to an adjoining room (say over 20mm difference), but the intention is to run the flooring seamlessly through both areas, a deep base levelling compound can raise the lower level by up to 50 mm in a single application. These products can also be used to fill in channels in the subfloor where an internal wall has been removed.
If the floor is semi exposed to the exterior elements, which could be the case if converting a garage into a home gym or a studio (or even you just want to upgrade an existing garage floor), an exterior grade levelling compound will be required. With this option, the levelling compound can also be left uncovered and used as a wearing course.
Exterior grade levelling compounds are also useful for levelling a particularly uneven damp subfloor prior to the application of a DPM, which could otherwise ‘pool’ in indentations and require more of the DPM to achieve complete coverage. The DPM will then need to be capped with a thin layer of levelling compound.
Once the levelling compound has set and cured, the subfloor is ready to receive the floorcovering, with the perfect surface texture to create a strong bond with the flooring adhesive. Not only will the finished installation benefit from optimised aesthetics, it will retain its appearance and integrity throughout its lifetime.
For further information on Setcrete visit setcrete.co.uk.