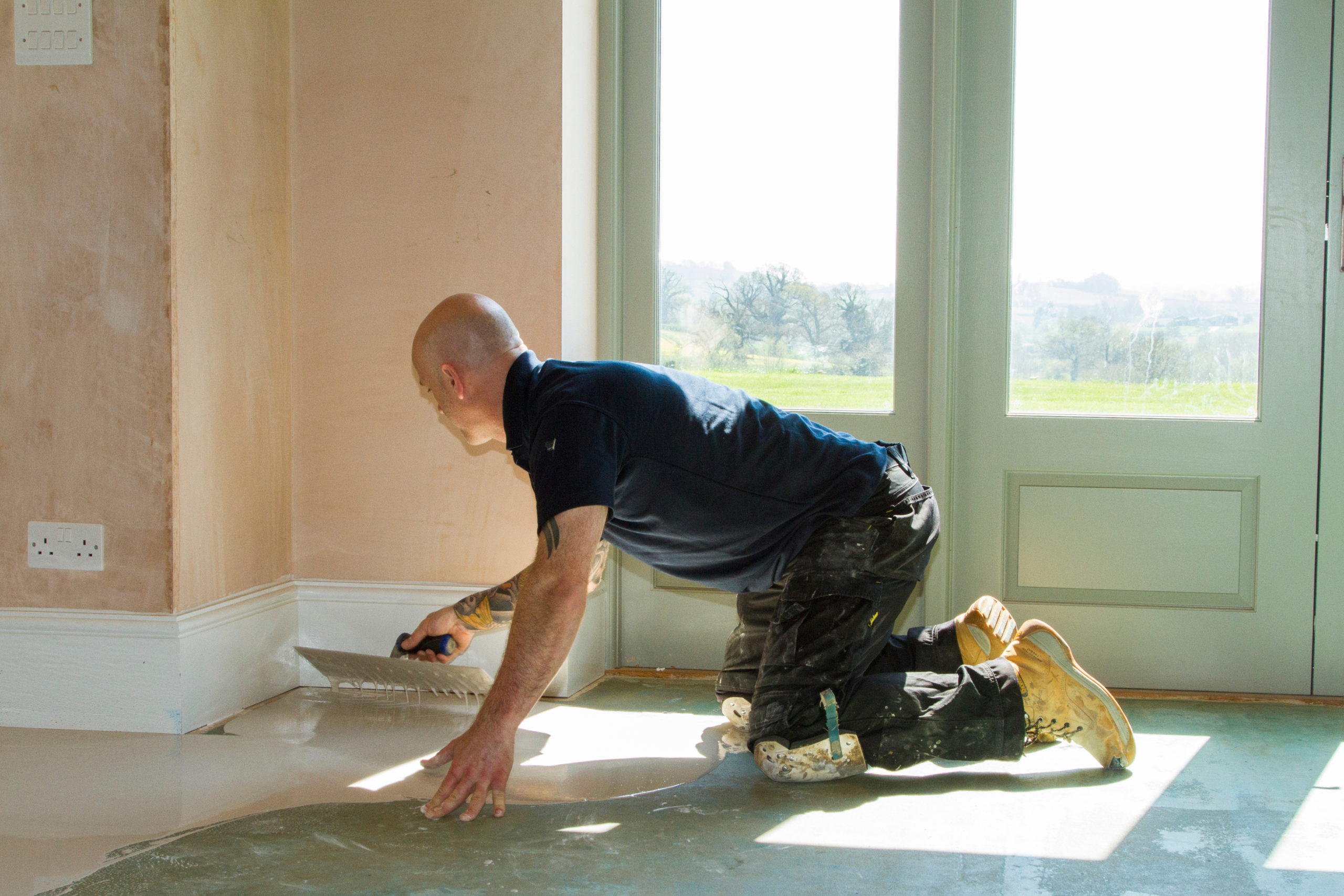
Setcrete High Performance maintains integrity for conservatory floors
Setcrete High Performance floor levelling compound is the perfect option for smoothing screeds in high solar gain areas, such as conservatories, prior to the installation of a floor covering. Such locations are subjected to sudden and wide fluctuations in temperature and require a levelling compound that can withstand the stresses and strains caused by the material’s desire to expand and contract in response to temperature changes.
The levelling compound utilises a fibre-reinforced cement formulation, with the tiny fibres performing a similar function to steel reinforcement in reinforced concrete. As such, the levelling compound will retain its integrity throughout the sudden and rapid warming and cooling cycles encountered in a conservatory or other heavily glazed areas, including school and hospital corridors and contemporary kitchens featuring bifold doors.
The solution is suitable for use over both absorbent and non-absorbent subfloors, including sand/cement and concrete screeds, as well as granolithic, terrazzo, epoxy and polyurethane resins, ceramic and quarry tiles.
In addition, the fibre reinforcement provides a level of flexibility that makes it suitable for use over plywood subfloors. Conventional levelling compounds subjected to slight flexing encountered in flexible subfloors will crack and break up over time and repeated use. Even when flooring grade plywood is firmly screw-fixed to a suspended floor in line with the recommended British Standards, it will still encounter minor movement when walked on.
As such, the product can be used throughout the entire floor of a property, providing a uniform, unbroken subfloor finish that offers the perfect base for the installation of floor coverings, optimising their aesthetic appearance and the long-term performance of the floor. This is particularly beneficial in modern, open plan homes, where the same flooring can run throughout the entire floor plan of a property.
The levelling compound can also be used to encapsulate mesh-mounted wire underfloor heating systems installed over both screeds and well-fixed timber (plywood) subfloors.
Moisture menace
Before installing any levelling compound and the subsequent floor covering, it is essential to check for the presence of moisture in the subfloor screed.
Subfloor moisture is the biggest cause of flooring installation failures bar none. It is particularly an issue for floor coverings that are adhered to the subfloor, such as increasingly popular luxury vinyl tiles, as well as wooden flooring.
Moisture in a subfloor will naturally rise to the surface, where, if it is unable to escape, will condense and collect under the installed floor covering. This moisture will attack the adhesive used to secure the flooring to the subfloor, causing vinyl sheet to blister and tiles to lift, and result in wood floors warping.
In older buildings, excess subfloor moisture is typically caused by the absence of a structural damp proof course (these only became mandatory in buildings in the 1960s) or, if a damp proof course was installed, it may have become damaged over time.
In new buildings or extensions, excess moisture is normally the result of residual construction moisture in a recently installed screed. As concrete typically dries at a rate of around one day per millimetre of screed (for the first 50mm and then 1mm every other day beyond this), a 150mm deep screed would be expected to take well over six months to dry out sufficiently for a floor covering to be safely installed.
Fortunately, there is a ready-made solution to the problem, which is to apply a liquid, epoxy resin damp proof membrane to the subfloor before installing the levelling compound and floor covering. Because this is an additional process and cost, it’s tempting to try and cut corners, especially if the subfloor ‘feels’ dry. But it’s not worth the risk, as remedial work, entailing the complete removal and reinstallation of the flooring, will be very expensive.
Test and treat
Subfloor moisture cannot be detected visually or by touch or smell. Easy-to-use, handheld moisture meters are available to give an instant reading of the presence or absence of moisture. However, to determine the precise moisture level, a digital hygrometer should be used at different points across a floor.
These need to be taped to the floor and left overnight to reach a state of equilibrium. The result, measured in terms of relative humidity (RH), needs to be below 75 per cent RH or below 65 per cent RH if wood flooring is going to be installed.
If moisture is present, a two-part epoxy DPM can be applied in a single application over the entire floor, offering protection up to 98 per cent RH. Rapid setting DPMs will cure in approximately three hours; ready to receive the new floor covering.
Once the DPM has cured, the membrane must be primed with Setcrete Acrylic Primer prior to applying the high-performance levelling compound. Subfloor priming is also required if the subfloor moisture level is below the permissible RH threshold and does not require a DPM to be applied.
The result is a super smooth subfloor surface that makes the installation of the final floor covering easier and faster and optimises the finished aesthetics and long-term performance of the finished floor.
For further information on Setcrete High Performance visit https://www.setcrete.co.uk/product/high-performance/