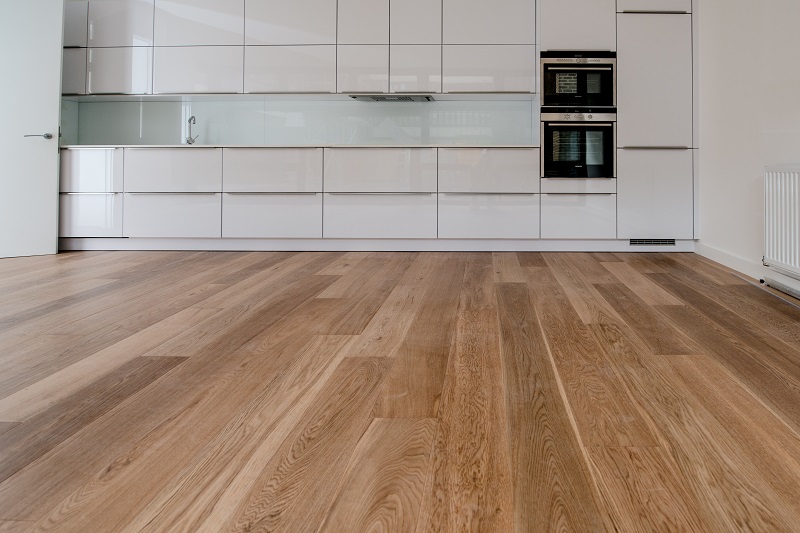
Peter Wilson, Brand Manager of subfloor preparation products manufacturer, Setcrete, explains what preparation subfloors need when installing luxury vinyl tiles
Luxury vinyl tiles (LVTs) and planks have enjoyed and continue to enjoy massive growth in UK flooring installations. Offering a plethora of styles and designs – often mimicking the appearance of traditional materials, such as timber and stone – LVTs are not the cheap and cheerful option associated with their 1970s’ ancestors.
In fact, many of today’s high end LVTs are anything but cheap and represent a significant investment. Customers rightly expect the finished appearance of their flooring to reflect this investment – they want the ‘Wow! Factor’. To deliver it, professional preparation of the subfloor is absolutely essential in optimising the aesthetics of the floor and also in safeguarding it against the number one cause of flooring installation failure.
To achieve the perfect finish when installing LVTs (or any vinyl for that matter), it is important that the subfloor base is completely smooth and free from undulations. LVTs are, by their nature, thin and flexible. When they are adhered to a subfloor any high spots or depressions in the subfloor can show through the material and be visible on the surface, increasingly so as the floor is walked on. LVTs and planks will also follow the contour of the floor, including any dips and undulations present.
To avoid these issues, the application of a levelling compound is essential. The levelling compound will smooth out any high spots and indentations and create a perfectly smooth and visually level subfloor surface, ready to receive the LVT. We would recommend a levelling compound that can deliver strength and toughness to keep the floor in prime condition.
If LVTs are going to be installed over plywood, a fibre-reinforced, high performance levelling compound should be used, which will be able to cope with slight flexing of the subfloor as it is walked on. The fibres act in a similar way to steel rods in reinforced concrete, maintaining the integrity of the cementitious compound. As well as being suitable over plywood subfloors, these high performance compounds are equally effective for use over other subfloor types, including normal sand/cement screeds and concrete. So, if you have an installation with a mix of subfloor types, the same levelling compound can be used throughout.
Once the levelling compound has fully dried, it provides the perfect surface for installing LVTs. The smooth, blemish-free levelling compound facilitates easy application of the adhesive using a notched trowel and provides a surface texture that encourages the adhesive to key into it, thereby delivering a strong, secure bond.
First Things First
To make sure that your pristine job maintains its aesthetic appearance and integrity, there is a critical first step that needs to be taken before even reaching for your electric mixer to prepare your first bucket of levelling compound. That is to check the subfloor for the presence of excess moisture; a hidden menace that continues to be the number one cause of flooring installation failures.
The cause of moisture may be rising damp or water ingress, especially in older homes where a damp proof course may not be present or may have been breached. In new homes it is likely to be residual construction moisture in the screed (a sand/cement subfloor dries at an approximate rate of 1mm per day).
Moisture in a screed will rise to the surface and then become trapped under the floorcovering. With nowhere to go, it will attack the adhesive used to adhere the floorcovering, resulting in vinyl floors blistering or tiles lifting. It can also lead to bacterial growth, presenting a health hazard for occupants.
Excess subfloor moisture is not always readily detectable, and you cannot rely on touch or smell to ascertain whether or not it will become an issue. The only sure way to tell if moisture is present or not is to use a moisture meter or digital hygrometer.
A hand-held moisture meter, used at various points around a room, will indicate if moisture is present or not. But to get an accurate reading of moisture levels, a digital hygrometer should be used, again, at various points around the room.
Measured in terms of relative humidity (RH), the moisture content of a subfloor must be below 75% RH (this is reduced to below 65% if wood flooring is being installed). If excess moisture is detected, the application of a single-coat, epoxy resin damp proof membrane (DPM) will provide protection up to 98% RH. Failure to check for moisture and deal with it appropriately not only risks compromising the integrity of the subfloor, but also risks damaging your reputation. It’s not worth taking the risk.
Once the moisture level has been checked and, if required, a DPM has been applied, the installation of the levelling compound and floor covering can proceed, starting with the use of a primer to promote the adhesion of the levelling compound to the subfloor or DPM and also to prevent the unacceptably rapid drying of the levelling compound when applied over absorbent subfloors.
The result: an LVT installation with all the ‘Wow! factor’ you could ask for and, importantly, one that will keep its tip top appearance throughout its lifetime.
For further information on Setcrete visit https://setcrete.co.uk.