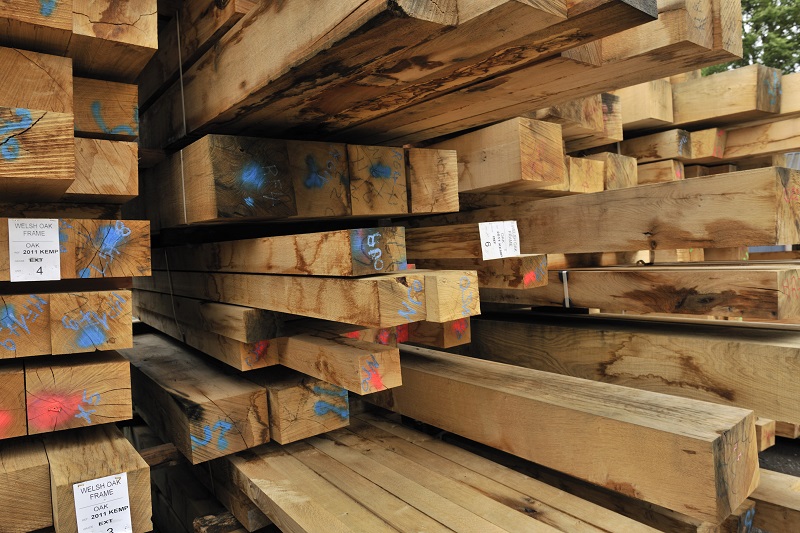
The investment in an advanced machine, capable of planing all four sides of an oak beam at once, to produce a perfectly square beam, is helping Welsh Oak Frame to answer the ‘man vs machine’ question found in many handcrafted joinery businesses.
Welsh Oak Frame, based in Caersws, mid Wales, manufactures and erects high quality timber frames for custom-build housing developers and self builders across the UK. The company combines traditional joinery skills and modern methods to ensure compliance with the latest Building Regulations.
The new machine, from Hundegger, incorporates the most advanced German engineering technology and is capable of taking a natural sawn oak beam, which can be easily ‘out of true’, and in one pass through the machine, can plane the four sides into a perfect square to pre-set dimensions entered into the control panel. The machine also produces a very smooth surface finish, requiring minimal additional preparation.
Sizing
Accurate sizing in the beams is critical in timber frame manufacturing, as it is around this datum set that all the other calculations for joint and detail dimensions are made.
Mark Jones, General Manager for Welsh Oak Frame, said: “Frankly it would be virtually impossible for any skilled craftsman to achieve the same dimensional accuracy and finish in anywhere near the amount of time and with so little waste. Yet at the same time, it is the traditional handcrafted skills we use in other parts of the frame process, especially around the joints and pegs, that make the difference and bring out the true character and individuality of the timber – that’s what makes each frame unique.
“It is a delicate balance. With ever more stringent Building Regulations demanding closer tolerances in building, especially at the interface of different materials in the structure, we have to be as precise as we can be in many areas, and that’s where the investment in advanced machinery is vital. Yet, there is still no substitute for the human eye and a feel for ‘what’s right’, built up over years of hands-on experience, when it comes to getting the best character out of each piece of oak and the overall frame.”