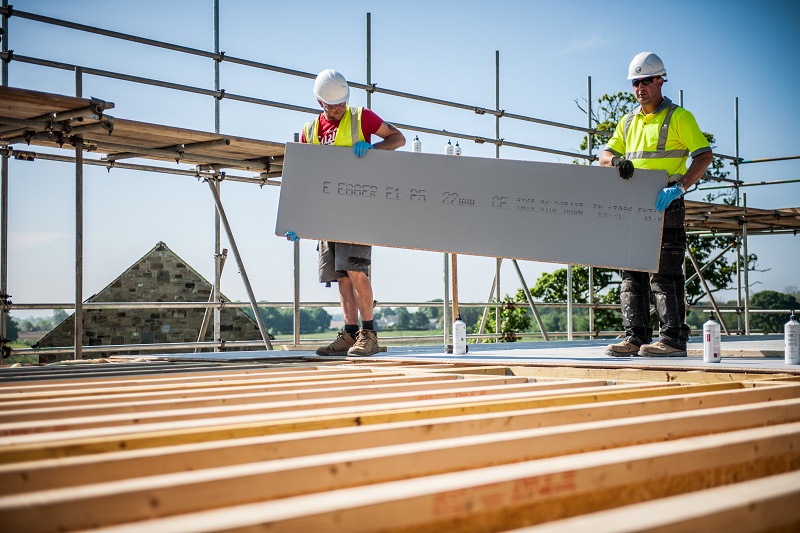
Reasons to be Chipper
The Romans may have long since departed but the town of Hexham is still wall-to-wall with logs! Professional Builder visits a company for whom the chips are never down.
Nearly 2,000 years ago, the Romans would light bonfires in these parts to warn of impending attacks on their infamous wall from marauding tribes occupying the untamed lands to the north.
Happily today, the vast acres of woodland surrounding the historic town of Hexham are being put to an altogether more productive use, and the constant plume of harmless steam emitting from the vast Egger factory is a reassuring message to the locals that all is well in the world of the region’s most significant employer.
In fact, they have been making wood-based panel products on this site in the northern extremes of England for more than 30 years, and many of our more mature readers will fondly recall the Weyroc brand with all things chipboard.
Acquired in 1984, the factory is today an integral part of the Austrian-based Egger Group, which with 17 plants throughout Europe is one of the largest privately owned chipboard manufacturers in the world.
Back in 1961 in the Austrian town of St Johann, things were a little different to say the least with an output of no more than half an articulated lorry of basic chipboards per day from a handful of employees.
Now, thanks to an eye for opportunity, and an unwavering commitment to invest strongly in the latest technology, Egger currently boasts over 7,700 employees, produces around 740 artic truckloads per day, and turns over more than 2.34 billion Euros each year.
Investment
It is in Hexham, however, where some of the most dramatic improvements in output have been achieved in the past decade, thanks in no small part to more than £250m of investment in making the site both more efficient and eco-friendly. When Egger took over 30 odd years ago, production capacity was around 60,000m3 and employees totalled 130. Last year that had risen to 650,000m3 and in excess of 650 employees.
To feed the insatiable appetite of this behemoth of a factory, more than 120 loads of raw wood-based material from carefully sourced plantations in the region are delivered to site with roughly 130 loads leaving the same day with finished product. These mind-boggling statistics are possible thanks to what, at over 48 metres, is regarded as one of the most technological chipboard presses in the world. Logs, sawmill residues and recycled material are taken through a journey of chipping, drying, resin mixing, steam injection and pressing to provide a variety of boards for a multitude of uses both in construction and the furniture making industries. Nothing is wasted, thanks to significant investments in recycling facilities, which provide a constant supply of reusable clean material, and an on-site heat plant to burn excess material, which is ultimately fed back into the production process.
Whilst the enduring popularity of chipboard as a general purpose material for the building trade has never been questioned, Egger is clearly aware of the need for the product to constantly evolve to meet both the challenge of competitive products and the changing demands and regulations of the building process.
One of the most significant developments in recent years has been the introduction of the company’s advanced structural flooring system. At its heart is a portfolio of boards and adhesives, together with a method of fitting them that, when combined, offer what the company considers to be the best method of installing a floor currently available to the builder. What’s more, it comes with a lifetime guarantee.
Other innovations include the Peel Clean Xtra product for protection from site traffic and wet trades which, thanks to an anti-slip polythene film, prevents moisture ingress and leaves a polymer sealed surface on top of the board on completion.
For even greater peace of mind, the system offers Egger Protect, a permanent dual surface protection option on site for up to 42 days. It can even be laid during light rain conditions with disruption to the build process kept to a minimum.
At the heart of all this innovation is the backbone of the Egger range, the P5 Tongue and Groove Enhanced moisture resistant board for residential applications.
Specified by the NHBC for new build properties, it is ideal in dry conditions for domestic flooring, renovations and refurbishment as well as damp or humid environments such as bathrooms and kitchens.
Every board is created using diamond tipped tooling to provide a constant T and G profile and ensure a tight joint every time.
As Category Manager (Building) Dan Soulsby proudly explained: “We can only achieve this thanks to exceptionally high quality and consistency of our board. To test its mettle, Egger P5 is firstly conditioned in our lab, then immersed in water for 70 hours at 20°C then frozen at between -12°C and -25°C for one day then dried in an oven at 70°C for another 70 hours. As if that wasn’t enough the samples are then cooled for 4 hours before the whole process is then repeated another two times!”
He adds: “This year has also seen a further £5m investment in a state of the art T&G facility which will allow us to increase our capacities, flexibility and produce our Peel Clean Xtra board in house.”
Peel Clean Xtra and Protect are not the only added value product Egger can offer, however. The manufacturer’s Decorative Protect Structural Flooring features an attractive moisture resistant oak effect wood grain suitable for use in humid conditions, whilst those involved in timber frame construction can call upon a range of products such as Egger OSB3 and OSB4 board as well as a 30mm OSB HDX panel for industrial flooring and mezzanine uses.
Comments Dan: “The majority of visitors to the Hexham facility are amazed, firstly by the sheer scale of the operation with logs and chips as far as the eye can see, but also that after all these years chipboard is still used in such vast quantities for a diverse range of building applications. Any negatives over these past 30 years have largely been as a result of inferior products coming on to the market and using boards in ways in which they were never intended.
Having said that, the chipboard of today is a vastly different proposition to those available even ten years ago. Through the ups and downs of the construction market, Egger has continued to invest in every part of the process, scrutinising and refining to produce a product which is equipped to meet the more exacting requirements of a construction industry under increasing pressure from ever more stringent Building Regulations and time restraints.”
Thanks to Egger, in one respect at least you can have chips with everything these days and still be in a very healthy place!
For more information on Egger click here.