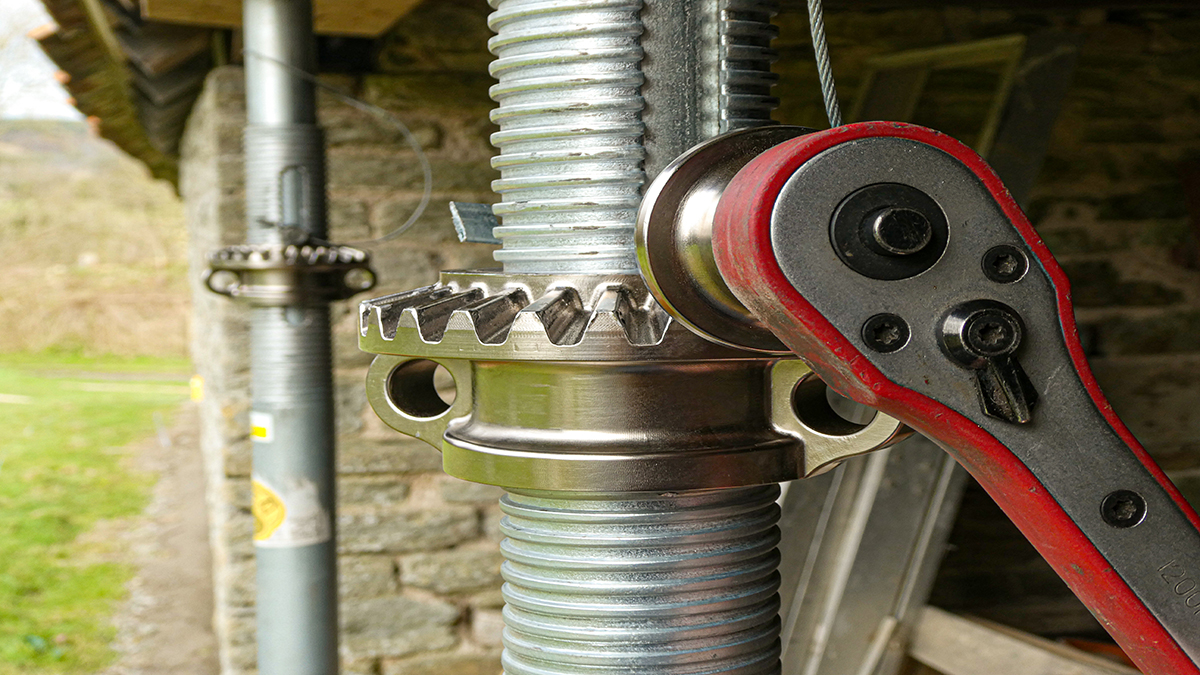
The art of creating temporary structures to support a building during its construction has been practised since ancient times and is generally known as falsework. Up until the turn of the 20th century almost all falsework was hand made from timber and had to be purpose built. However, in 1935 a Swiss born inventor named William de Vigier designed a steel support that could be manually adjusted to the desired height using a threaded collar. This enabled it to be quickly installed, removed and reused, which led to huge reductions in labour costs and material usage. De Vigier named his business “Acrow” after his solicitor Mr A Crowe who helped patent the idea.
Despite early scepticism within the industry, it soon became the go to product, being particularly effective in reducing the cost of temporary structures to cast slabs and walls of concrete, known as formwork. The company went on to revolutionise many aspects of the construction industry and its products soon become an industry standard with the term acrow becoming established as a generic around the world.
Sadly, that original business has long since folded but the overall design remains largely the same some eighty years on and is a key component in modern construction and renovation projects. The temporary supports now have standard threads and load capacities and are available in five common sizes, extending anywhere from between 1 and 4m.
Despite its universal adoption on building sites around the world, however, setting up steel supports are not without their drawbacks. It is a time-consuming process, labour intensive and sometimes fraught with the risk of injury. Spinning the collar to the right height requires physical effort and when threads are caked in dirt, rust and cement it takes significantly longer. Holding the support in the desired position while carrying out minor adjustments can be awkward for a one-man operation and pinched fingers between the metal sleeves or the handle is not uncommon. It’s not unusual also to see a hammer being used to make the last couple of turns but a mistimed glancing blow can lead to more physical and debilitating injuries.
It was with all these factors in mind that in 2021 an accomplished team of British engineers and designers decided that it was high time for the octogenarian acrow to have a major overhaul. Together they came up with a unique way to adjust the device using a cordless impact driver – the sort no self-respecting tradesman would been seen on site without.
Working on the basis that all conventional acrows have a standardised trapezoidal thread, the team designed its new pinion geared collar as a straight swap for an existing collar, enabling any size of temporary steel support to be easily retrofitted. Adjustment, if required, can also be made manually by using the incorporated lugs from the original acrow collar design.
With the patent secured, a company has been set up to bring the product to market and in tribute to the lead inventor’s late father-in-law Jim, the J-strut is now set to “collar” a new generation of steel support users.
For further information on the J-strut visit https://j-strut.com/