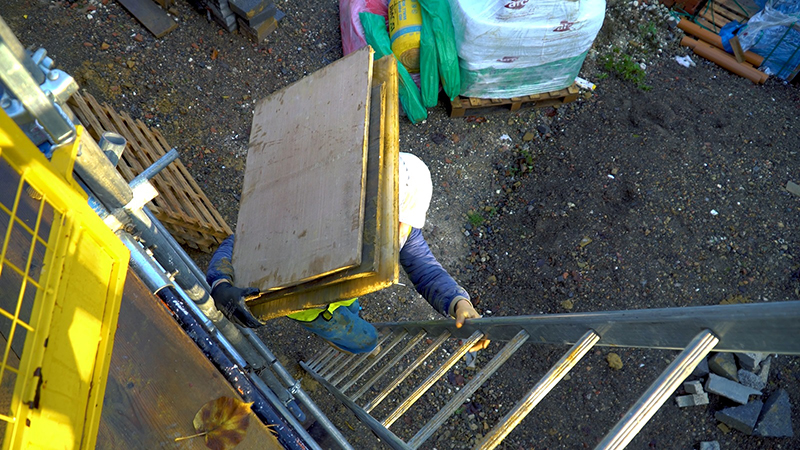
Professional Builder meets the bricklayer behind the Flexi Block Spot.
They say a leopard never changes its spots…….. but what about a bricklayer.?! That’s a question which has been troubling brickie Marc Foley for years and one which he believes he is on the brink of answering in the affirmative.
It’s generally accepted that the first bricks were laid more than 9000 years ago in Southern Turkey and, ever since, the bricklayer’s tool kit has largely comprised a trowel, a level and a fair modicum of dexterity. Oh and of course, the humble spot board to keep the all important mortar close at hand. More often than not a random piece of wood or ply off cut usually does the trick and in truth its one of those taken for granted items, a bit player in the overall scheme of getting the wall up. It’s a scenario routinely played out on thousands of building sites everyday but one that if bricklayer Marc Foley has his way, the industry will soon, quite literally, be spotting a very different way of going about its business.
He told us, “Like all brickies, the priority has always been totally on laying as many bricks as you can to a given standard in a day and leave the muck and bullets side of things to the labourer. Their role is crucial to ensure a ready supply of bricks in the right place and a constant supply of workable mortar. So far so good, but that’s where even the best ones are let down by the tools of their trade, makeshift spot boards. These are constantly exposed to the rough and tumble of the site, harsh weather conditions and the effect of the mortar itself rendering them very quickly not fit for purpose.
“It’s not the labourers fault of course, just the way its always been done, but the knock-on effect to the project is enormous – especially on big sites. For one thing the boards are heavy to lift on to the scaffold, absorb the water which in turn dries out the mortar and makes it less pliable for the brickie to use. Being random off cuts, they are often different sizes, either too small to contain enough mortar and need constant topping up or too big and block the scaffold. I put up with it myself for years and suddenly had a moment a couple of year back when I decided there had to be a better and safer way.
“The answer is the Flex Block Spot, a high quality rubber cover which sites over a standard pile of bricks or blocks and provides a perfect clean non absorbent surface for the mortar. They are extremely pliable and light, a labourer can easily carry up to ten in a bag onto the scaffold and of course at the end of the day can be washed down and left in place for the next day’s building . They will also provide frost and driving rain protection over night.
“After working through a number of designs and approaching some potential manufacturers we came up with prototypes which I used on my own sites and put out to some other builders I know in the area. The feed back was tremendous, usual stuff of being so simple why didn’t we think of its ourselves. Now with a patent and packaging in place we are ready to tell the world about it.
“Of course I am under no illusions that we can change so many years of practice over night. Bricklayers are a conservative bunch and with good reason of course but I really think we have something which will improve their ability to lay more bricks per day which in turn means greater productivity and of course profitability on the job.”