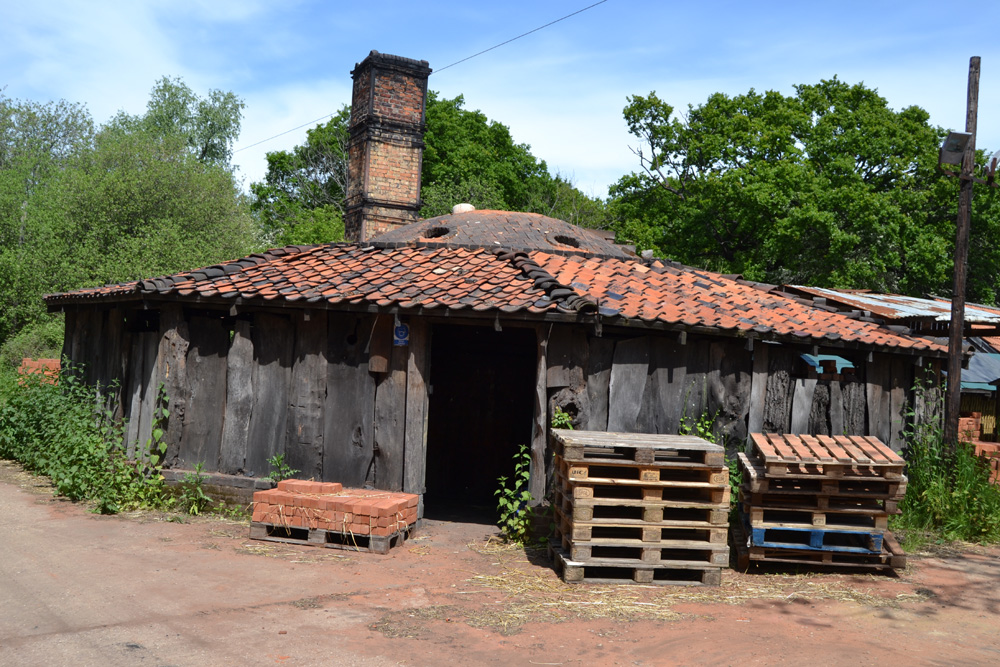
Bulmer Brick and Tile is maintaining the traditional brick maker’s skills. Professional Builder investigates.
The humble brick is so ubiquitous that we might be in danger of taking it for granted, but there is an art in the making of this most traditional of clay building materials, and its most skilled exponents can be found in a quiet corner of Suffolk. It is here, since as far back as the 1930s, that the now 86-year-old Peter Minter, and his father before him, have been producing the highest quality masonry under the Bulmer Brick & Tile brand, and today they are recognised as a leading name in the conservation and restoration sector.
There has been a clay quarry and brick makers’ yard at this eponymous Suffolk location since as far back as the 15th century, and many of the techniques used then are still maintained. The company operates two down draught kilns, where coal is fed into fire boxes around the circular, brick built structure. Heat then radiates upwards and is sucked down through a central flue to the stacked bricks below. The two Bulmer Brick and Tile examples can each accommodate up to 12,000 bricks at a time.
“It takes three days to load the kiln and, given that how the pieces are stacked can have a significant impact on the final colour, it is a process that requires considerable experience to get right,” explains Peter. “It then takes a further three days to fire the kiln, with up to 4 ½ tonnes of coal used for each firing, taking great care to maintain the optimum temperature throughout. That’s followed by another three for it to cool down, and a final three to unload.”
Even before then, however, the hand thrown clay bricks are stacked for drying which, depending on the weather, can take anywhere between 3 – 6 weeks, which means a single brick will have experienced a journey in time of two months or more before it reaches the builder.
Bricks shrink as they lose moisture so the drying time also has to be carefully regulated to prevent cracking, with humidifier equipped indoor areas utilised in the winter months, and damp hessian sheets made use of in the heat of the summer. Like any industry, the brick maker’s craft has its own ancient vocabulary, and the pattern of stacking for drying is known as skinking. These initially yellow pieces, when subjected to the 1,000ºC heat of the kiln, will then see their iron content oxidise, turning the beautiful red that is characteristic of a Bulmer brick.
Before mass production overtook local manufacturing, almost every village and town would have had its own brickworks, and Bulmer is a survivor of that bygone age. Some of these yards would have been producing bespoke pieces that have never been made before or since, whilst brick sizes would vary enormously depending on the period, but Peter and his team are on hand to reproduce whatever a client requires.
“Because of the varied dimensions of the pieces in the kiln every firing is different. Most of the time we make to order, and if a customer supplies us with an example, or a drawing, we can make it. In fact, we produce far more shapes and sizes than anyone else, and can supply a single brick if required. To achieve those shapes, clay is thrown into wooden moulds of our own making, and we have over 8,000 moulds in stock, with more fabricated in our workshops every single day.”
Bulmer Brick and Tile is also one of the few companies that still supply red rubbers – oversized bricks that can be cut down to the dimensions suited for decorative chimneys or gauged arches. The seam of clay around the village of Bulmer is amongst the finest in the country, which is why its brickmakers are not required to add anything other than water, whilst it is also milled in order to crush the iron pyrites that might blow the brick in firing.
In order to produce a very pure brick that can be more easily cut, however, red rubbers are washed and sieved to remove the small impurities that might be present. “Everything about a red rubber is labour intensive, and, because many tradespeople will not have the means to cut them on site, we can also shape the finished brick to the required size,” Peter declares proudly.
“The raw material is mixed with water until it is the consistency of a liquid, and then strained. The water is then squeezed back out of the clay, and it is left to settle before being hand thrown into the moulds. Because the clay is a denser and finer material than you would find in conventional handmade pieces, it has to be dried slowly in a carefully temperature controlled indoor environment.
“The main sizes we produce are 9 and 10½in., but we can supply a red rubber to whatever dimensions a customer specifies. We also use only the one type of clay we quarry on our own site, and that makes our product unique. We supplied all of the red rubbers for the arches in St Pancras station, for instance, and our pieces are used on the most prestigious projects in the country.”
Indeed, the high quality materials that Bulmer Brick and Tile produces lay seamlessly in some of our most precious heritage buildings. At the time of our visit, orders were being completed for Kensington Palace, Hampton Court, and Westminster Abbey, for example, but where there is a period property or listed building that requires a brick conservation solution then Bulmer can find the answer.