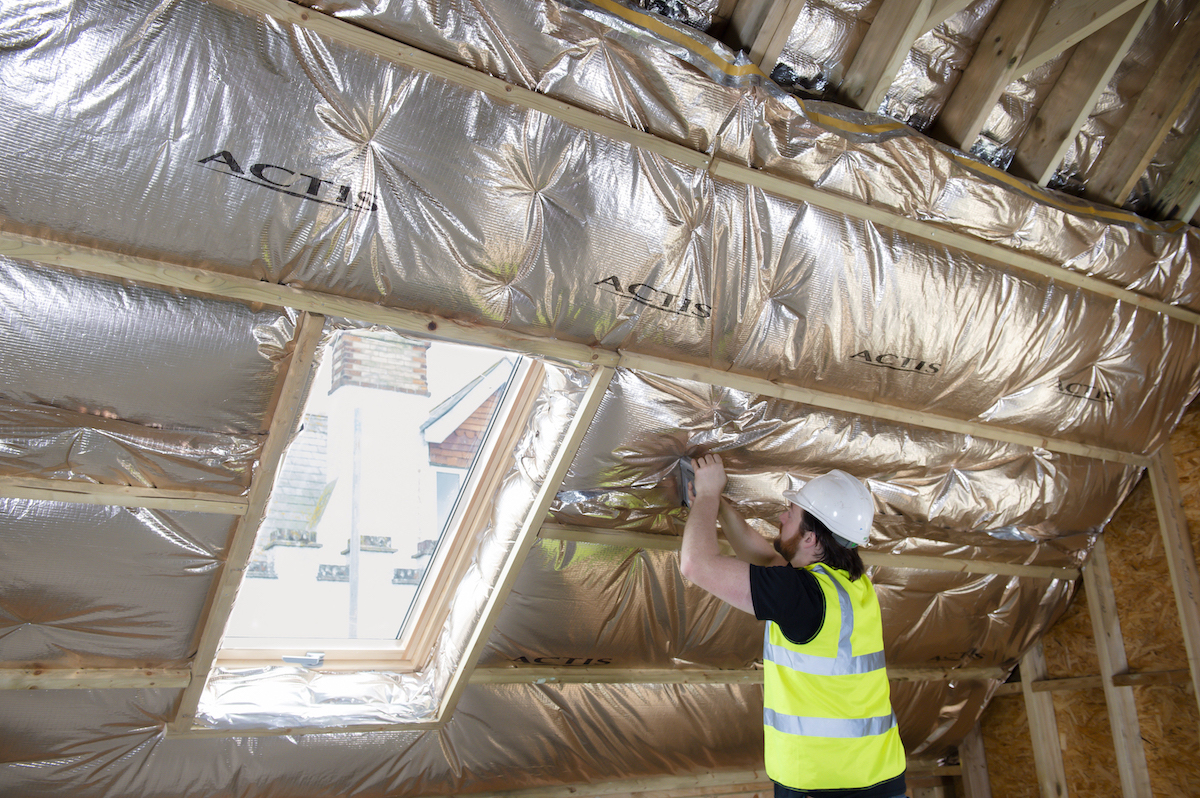
Actis outlines how you can save time, make life easier and hit Part L targets when carrying out extensions and conversions work
With the continued trend to reconfigure existing homes to create more space – perhaps for grown up children who can’t afford to move out – builders are looking for new ways to ensure conversions and extensions comply with increasingly stringent Building Regulations.
Creating a penthouse suite in the roof (aka a loft room with en suite!) for a nimble-footed twenty-something or a single storey rear extension for an older parent is bread and butter work for many builders.
Regardless of the size and scale of the project, the conversions or extensions need to attain specific thermal efficiency levels under Part L of the building regulations. And in each case, many builders say they find achieving this goal quicker, easier and more cost-effective by using reflective products created by insulation specialist Actis.
Kent builder Alan Downes, who specialises in renovating individual properties, is one of those who finds says Actis Eolis HC – a two-in-one reflective insulation with an integrated vapour barrier – is a huge time saver. “The thing that makes Eolis especially good for loft conversions is its flexibility and the ease of installation, particularly over pitched roof angles, allowing for a really professional seal of insulation across the roof space.”
Eolis HC is especially useful when dealing with shallow rafters where headroom is at a premium. It removes the need to cut insulation between each rafter, a tricky and dusty task if using PIR board. And while it is thin enough to be used in low headspace zones, in part because it doesn’t require the usual 25mm air gap to avoid condensation, it also offers excellent thermal performance.
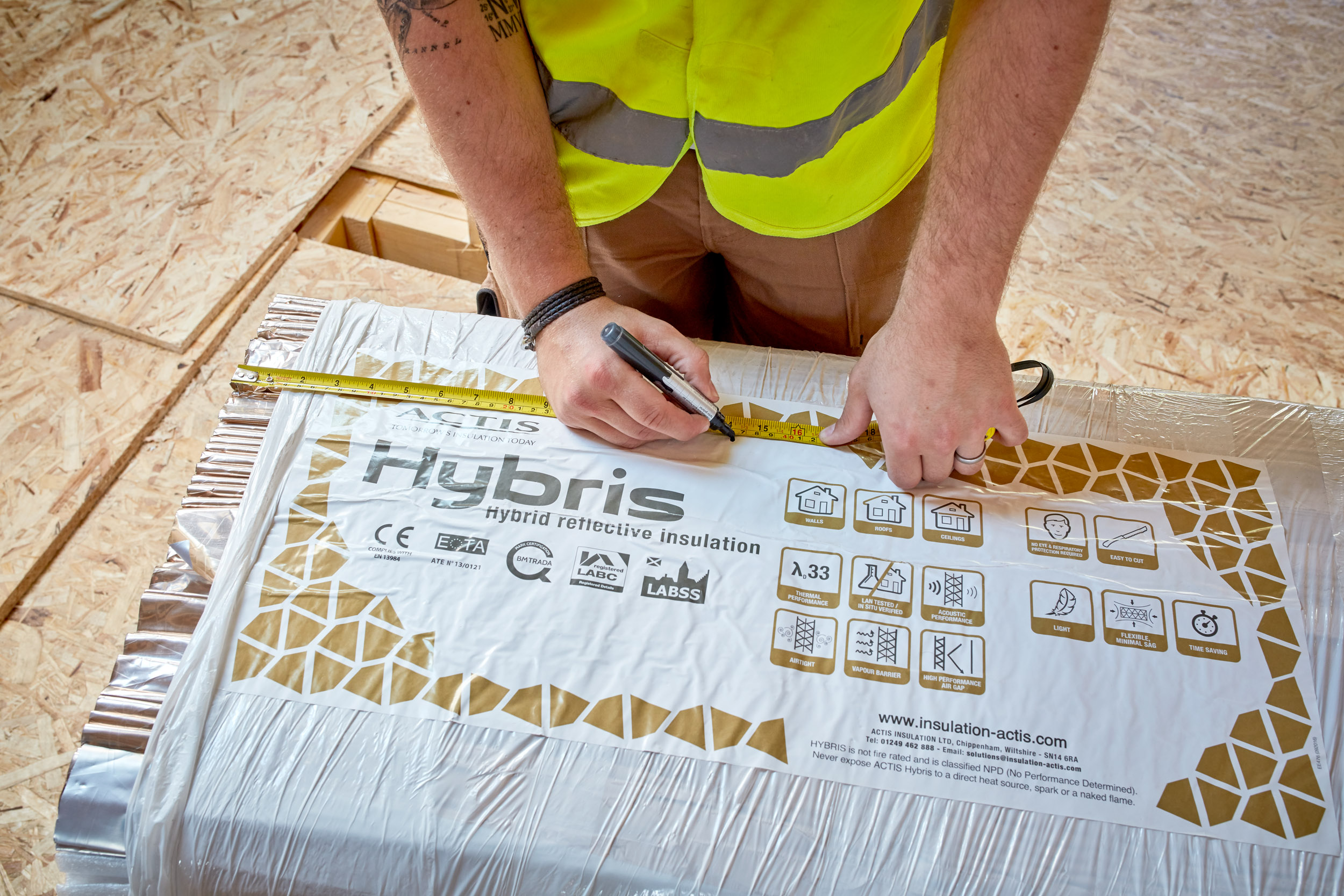
Time trials show that when insulating across timbers, using Eolis HC is at least twice as quick as using PIR board. At the grander end of the conversions scale is a 6,500 sq ft barn conversion in Northamptonshire whose owners enjoy minimal heating bills, courtesy of the Actis Hybrid range.
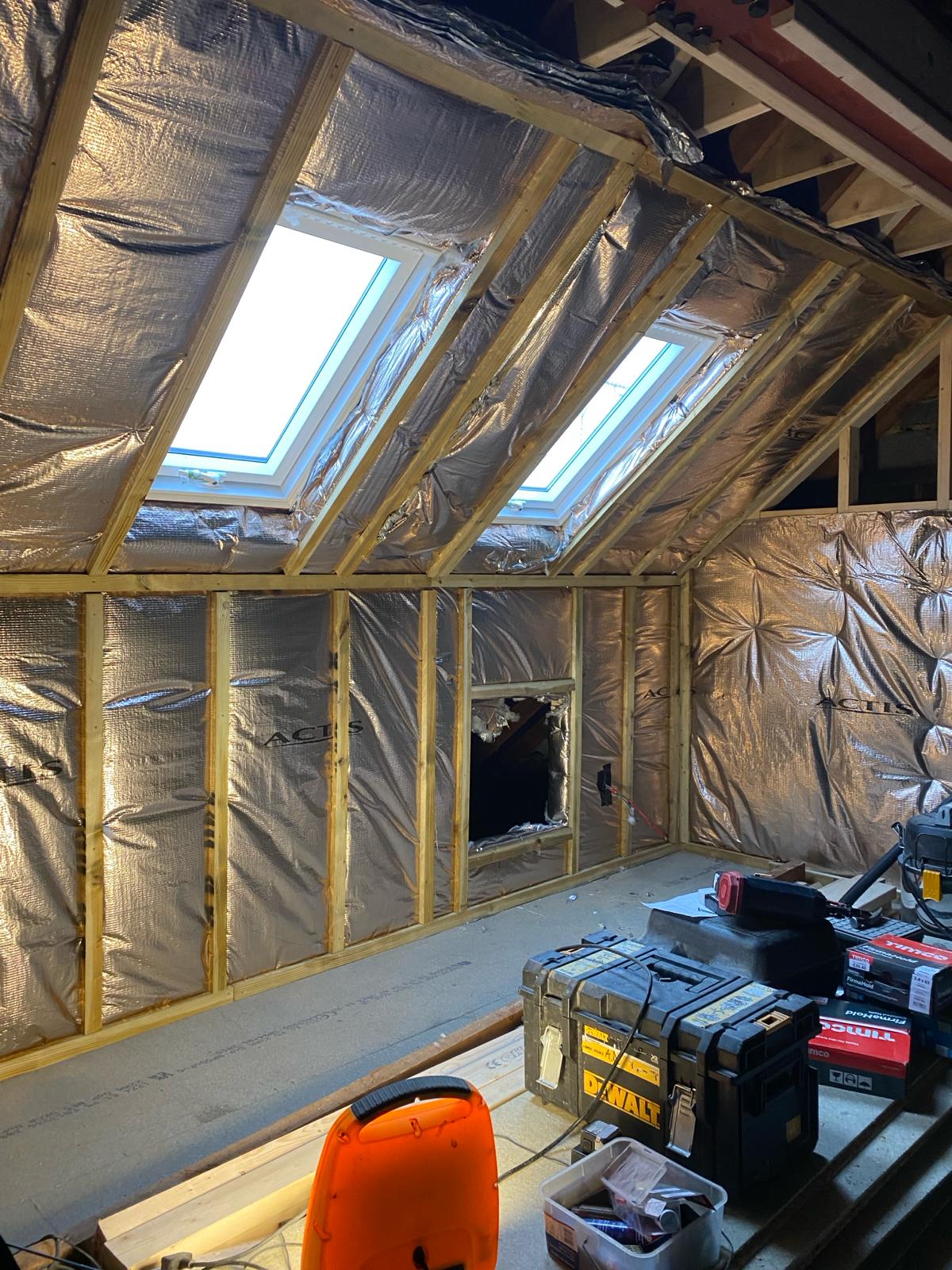
Created by architectural designer Stuart Ellis, the external walls were fitted with an 89mm stud and a combination of 50mm honeycomb style insulation Actis Hybris, insulating vapour control layer Actis H Control Hybrid and insulating breather membrane Actis Boost R Hybrid to achieve a U-value of 0.19W /m2K.
“Using Actis products is the thinnest way to achieve the desired U-values – and it’s really easy to fit. Using PIR board alone would have made the walls around 25mm thicker,” explained Stuart. There’s also less waste than PIR board, and it has the added benefit of taking up very little skip space.
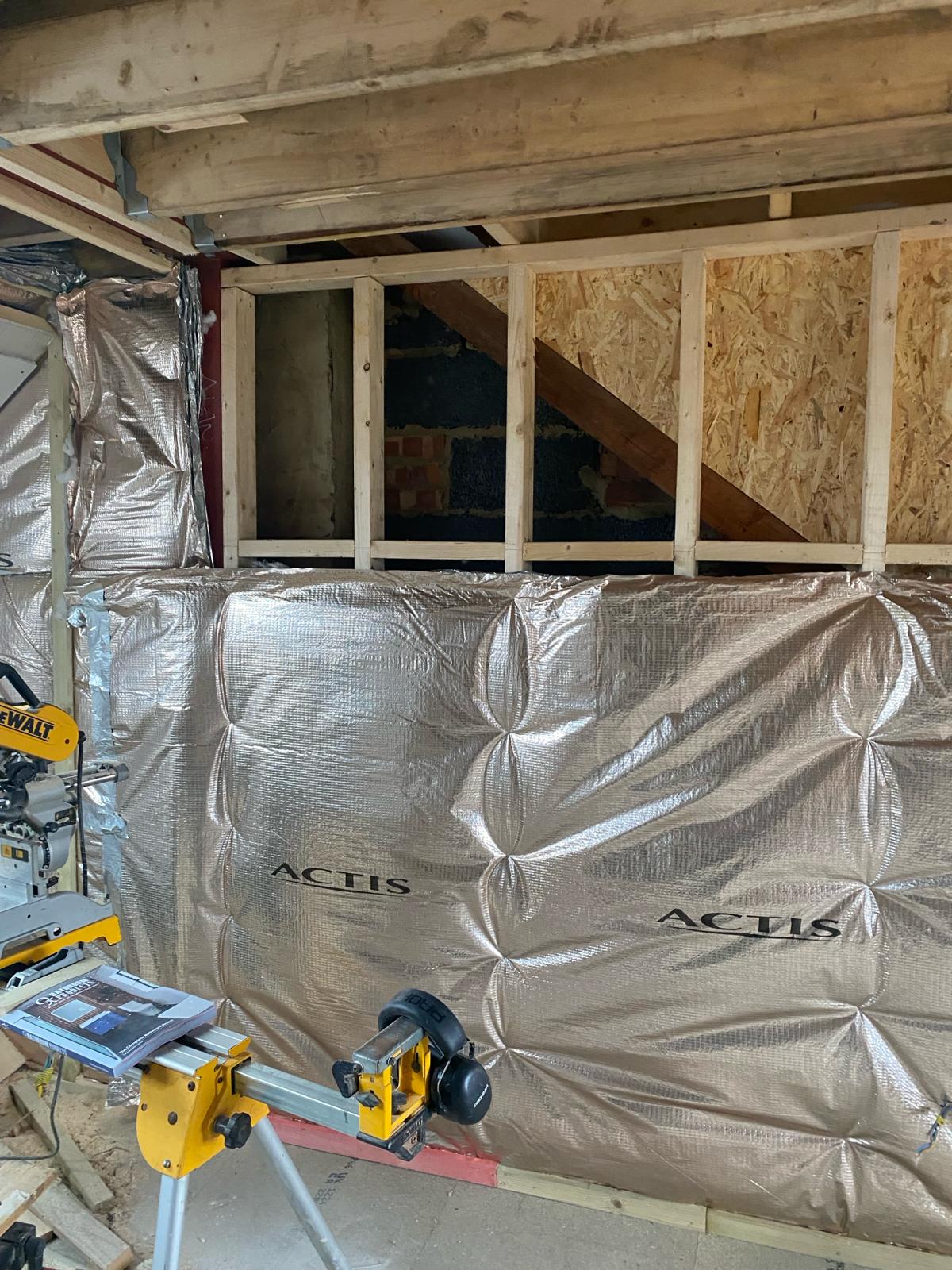
“I specify for a lot of listed buildings, which are really cold, so I build a stud wall inside into which to put the insulation. Obviously, I need to ensure the building is correctly ventilated to avoid condensation, so external air bricks can be added to ensure the stone can still breathe. I believe this is the way forward for listed buildings.”
And many builders find Actis products essential in enabling them to balance preserving England’s architectural heritage with meeting Part L regulations.
Brian Taylor from Tonbridge-based TW Projects is rebuilding and extending a historic hoppers’ hut in East Peckham to create a 150 sq m single storey home which combines the bucolic charm of 19th century rural living with thermal comfort. He’s using two layers of honeycomb 105mm insulation Hybris in the roof to achieve a U-value 0.15 and insulating breather membrane Boost R Hybrid, 140mm Hybris and 50mm of PIR in the walls of the timber frame extension and the stud walls created within the original structure to achieve a U-value of 0.14.
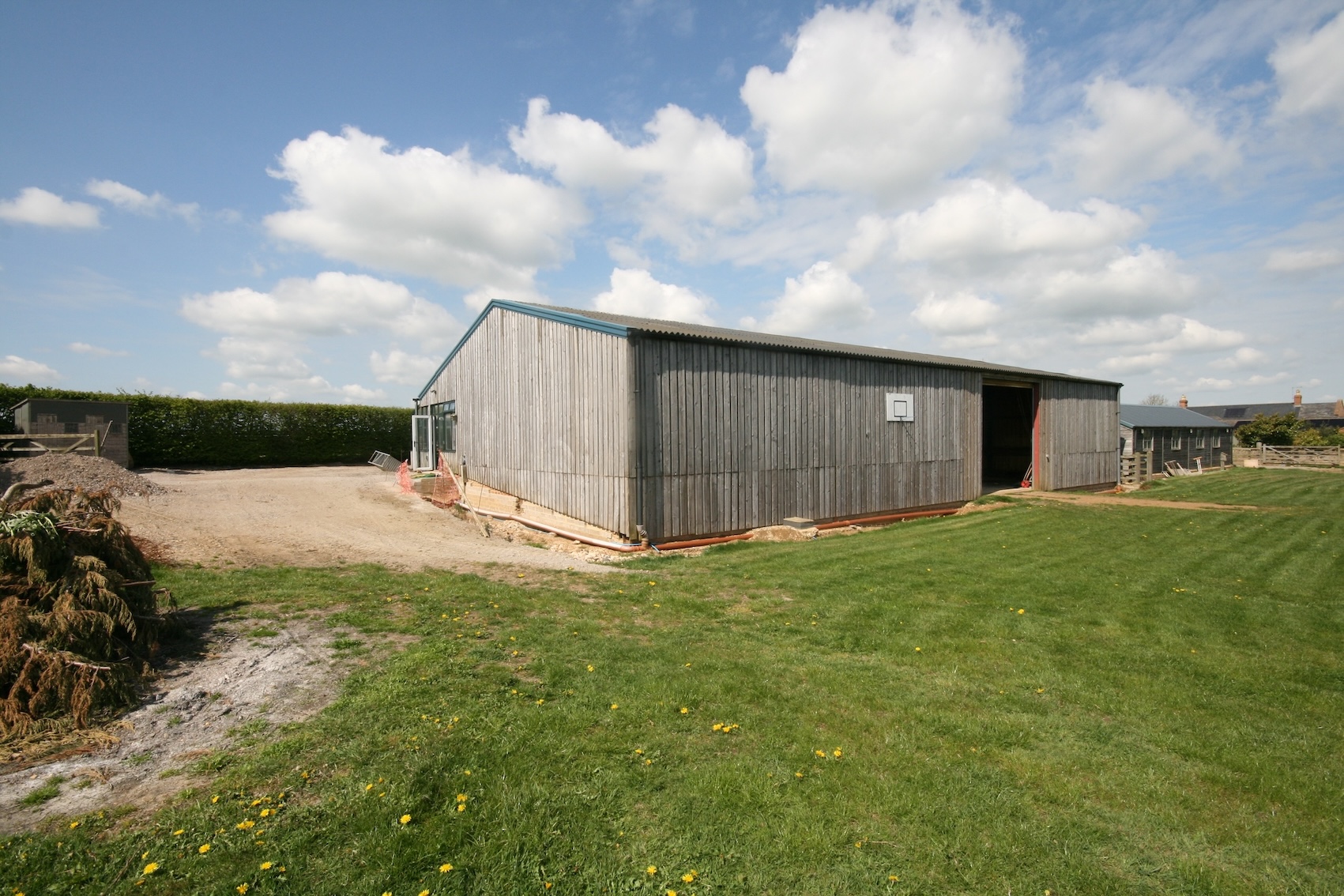
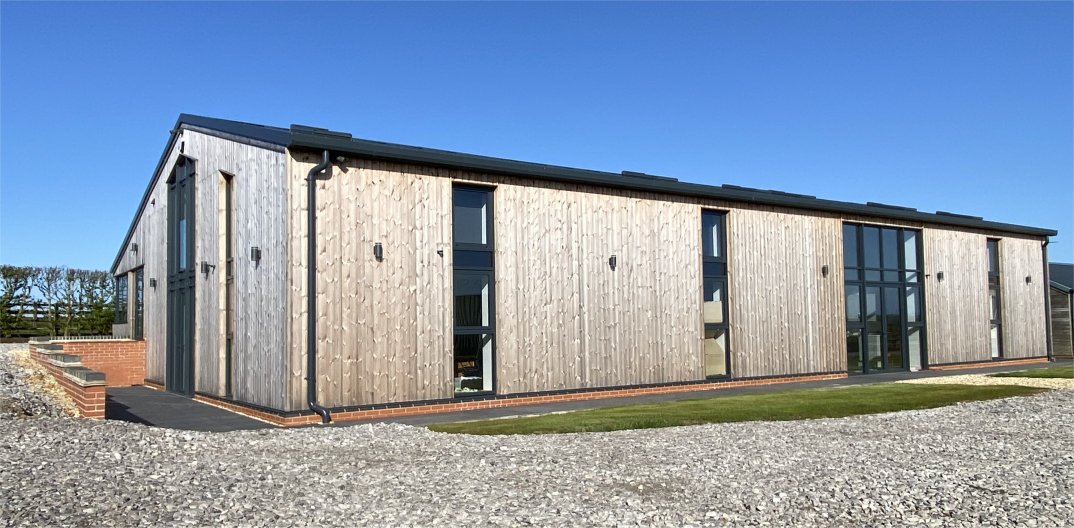
Brian explained: “We’ve been using Actis Hybrid products for years because they’re so quick, clean and easy to use – and are thermally brilliant.”
For further information on Actis Insulation visit ACTIS Insulation – Tomorrow’s insulation today.