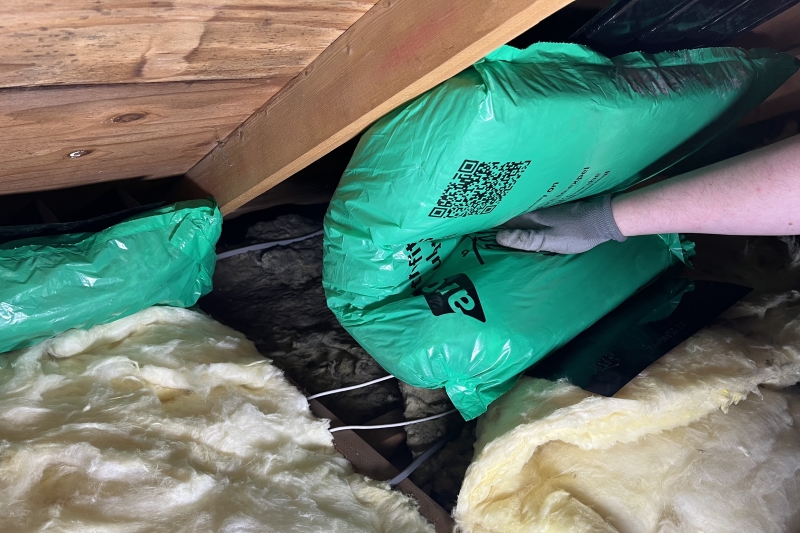
Dr Alex Boote, Product & Innovation Manager at ARC Building Solutions, discusses the importance of eliminating thermal bridging in housing stock.
Mould and damp – a consequence of thermal bridging – in UK housing continues to be a major issue affecting the built environment. Ranging from structural damage to serious health concerns, the repercussions of thermal bridging can be catastrophic.
As the UK moves towards a net zero future – and with energy costs rising and fuel poverty accelerating – the demand for warmer, more efficient homes is at an unprecedented level. Today, more than one–fifth of the UK’s carbon emissions stem from homes with poor energy efficiency.
A critical factor in improving energy efficiency is proper home insulation to minimise heat loss. Currently, the government is largely investing in retrofit installation, offering grants to improve homes with poor energy efficiency. However, while the allocation of government funding is positive, if insulation is poorly installed, this can lead to thermal bridging in housing, creating minimal impact or potentially, worsening the issue.
Thermal bridging commonly occurs when there is a localised weakness or a discontinuity in the thermal insulation of a building in areas such as the eaves – the joint between the roof and the wall – resulting in heat loss at these points.
Where the eaves junction is not properly insulated, cold spots form, resulting in condensation and damp. The moist air produced from exhalation, cooking and cleaning will condense at these thermal bridges, creating the ideal environment for mould to proliferate. The mould growth will not only damage the building and any item within the affected room, but it also poses a serious risk to the occupants’ health. If left untreated, mould can cause respiratory complications and, in the worst cases, death.
While much focus is given to insulating walls, roofs and windows, the eaves junction is all-too-often neglected. The difficulty in accessing and properly insulating the area results in inadequate insulation practices, exacerbating the chances of thermal bridging occurring. The result? High energy bills due to poor energy efficiency and the prospect of detrimental health risks due to mould and damp growth.
PAS2035, the framework for retrofit standards, specifies government funded retrofit projects require thermal bridges to be treated; this is solved by specifying our retrofit products. This framework plays a significant role in ensuring the quality of the retrofit is achieved and a higher standard of energy efficiency is met.
Although the eaves detail may seem like a minor aspect in building design, its impact on the overall comfort and health of a home really is significant. With the use of innovation, this problem can easily be addressed. As a leading manufacturer of fire and thermal solutions, we’ve developed the Retrofit Eaves Insulator, designed to address the major issues thermal bridging poses in existing properties. This product provides essential insulation at the wall plate while ensuring the necessary ventilation into the loft space is maintained through the 25,000 mm² vent tray, discouraging the formation of damp and mould through maintaining proper insulation in the building’s thermal envelope – all without compromising ventilation of the loft space.
Historically, the eaves junction would typically be insulated by installing glass wool into the area. However, this method has often blocked the crucial ventilation path, resulting in condensation build-up in the loft space, which contributes to the problems we are seeing in many British homes. Whilst some installers will have attempted to estimate a ventilation gap whilst fitting the insulation, it is very difficult to ensure the appropriate path is maintained over time.
The Retrofit Eaves Insulator is folded in half and inserted into the eaves junction, and as the product recovers, the insulation fills the gaps between the building elements, and the ventilation tray is pushed against the roof felt, guaranteeing a tight fit to the roof pitch, regardless of angle, and assuring a ventilation gap.
The new Part L requirements, which cover the conservation of fuel and power in new build properties, emphasise a greater focus on improving energy efficiency through correct primary eaves junction insulation – solved by specifying the ARC Eaves Insulator. However, Part L compliance doesn’t just mean achieving correct insulation. In fact, one of the most significant changes to the regulations in 2022 (Appendix B7.3.b) now requires on-site audits and evidential photographs to be recorded during inspections of the eaves detail. This added accountability on installers ensures thermal bridging cannot be neglected and installations are assessed retrospectively by Building Control.
By proactively addressing the challenges of thermal bridging and improving eaves junction insulation, housebuilders will not only be meeting regulatory regulations but also supporting the UK’s broader goal of reducing carbon emissions and becoming net zero by 2050. Eliminating thermal bridging in the future housing stock is the key to creating healthier, more energy-efficient homes.
For further information on ARC Building Solutions Retrofit Eaves Insulator visit Retrofit Eaves Insulator – ARC Building Solutions.