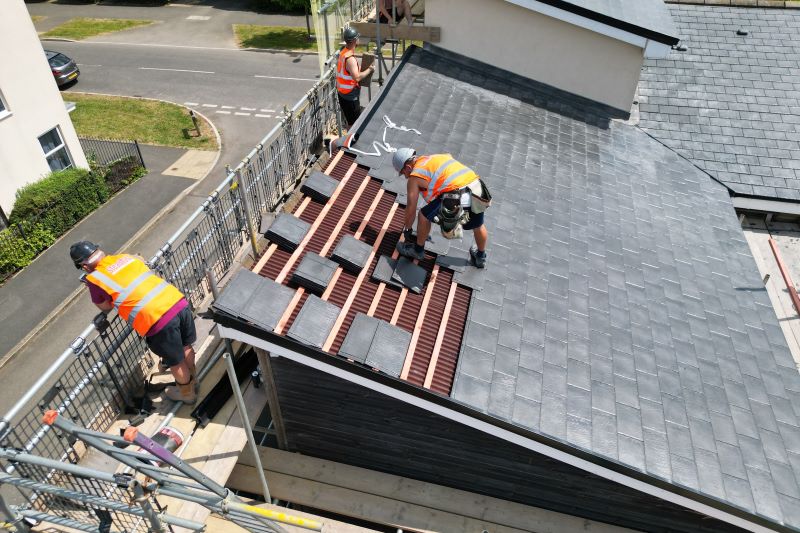
Ardit Strica, Technical Manager at Onduline Building Products, talks about sub-roof systems and why they’re a good option for contractors.
Architectural styles have been limited over the years by the constraints of traditional roof tiles. Tiles must be installed at a certain pitch, as stated by the manufacturer, to protect the roof from water ingress, meaning there are limitations when it comes to low pitch roofing.
With this in mind, when planning a domestic extension, a standard roof pitch may not be suitable. This is often because existing features, such as first-floor windows, get in the way and a lower pitch is required to work around them. Also, many homeowners prefer the aesthetic appeal of a low pitch roof over a flat roof.
However, many roofing supplies are designed for traditional roof pitches, and many contractors are accustomed to working on roofs with higher pitches. This is why there is a need in the market for an easy-to-use low pitch roofing solution. With low pitched roofs there are fewer tiling options and sometimes, depending on pitch, there might be no tiling options at all. This is where a ‘sub-roof’ can come into play.
Sub-roof systems have seen a rise in popularity within the market over the last few years, allowing contractors more freedom when it comes to roofing projects. A sub-roof is an additional protective layer within the roof structure which acts as the primary waterproofing layer under the tiles when the minimum tile pitch cannot be met, acting as a barrier against potential leaks and allowing the tiles to be a secondary aesthetic waterproofing layer.
There are different types of sub-roof systems. Flat sub-roofs are typically developed with non-breathable felt, which can be prone to a higher risk of moisture being trapped beneath the membrane, thereby rotting the timber underneath.
More recently, corrugated sub-roof systems have been developed, offering greater protection and advanced longevity of materials. Due to the corrugations within the sub-roof, there is increased ventilation and airflow both above and below the sheet and tile battens positioned above the corrugations allow moisture to drain to the eaves which, with the enhanced ventilation, maintains excellent moisture control within the cavity.
Not only does a sub roof help to meet the demand for maximising living space, as the low pitch means the roof void can be minimised, it also enables traditional tiles to be used in situations where they wouldn’t have been able to be utilised previously, such as extensions or large roofing projects, greatly enhancing the aesthetic quality of a property.
What are the benefits of a sub-roof system?
As the sub-roof system acts as the main waterproofing element of a roof, it means that the original aesthetics of a building can be preserved. Existing tiles can be re-used, or reclaimed tiles, which can save on cost and time, as well as reducing the carbon footprint. This ensures that the traditional look and feel of a property remains the same.
Integrating a sub-roof system provides an extra guarantee and protection should there be any cracked or broken tiles, a low pitch or incorrect fitting of tiles. The increased ventilation and performance this offers means that the roofing material will remain in good condition for longer.
Onduline, the lightweight roofing systems specialist, has recently launched its new and unique sub-roof system, ISOLINE LOW LINE – the only system in the UK to be BRE tested and BBA Accredited to as low as 10o with a 30-year guarantee. This lightweight bituminous underlay sheeting has been rigorously tested and is proven to be at least three times less likely to leak compared to a traditional tile system.
To find out more about Onduline’s range of products visit Onduline: lightweight roofing, cladding and construction materials.