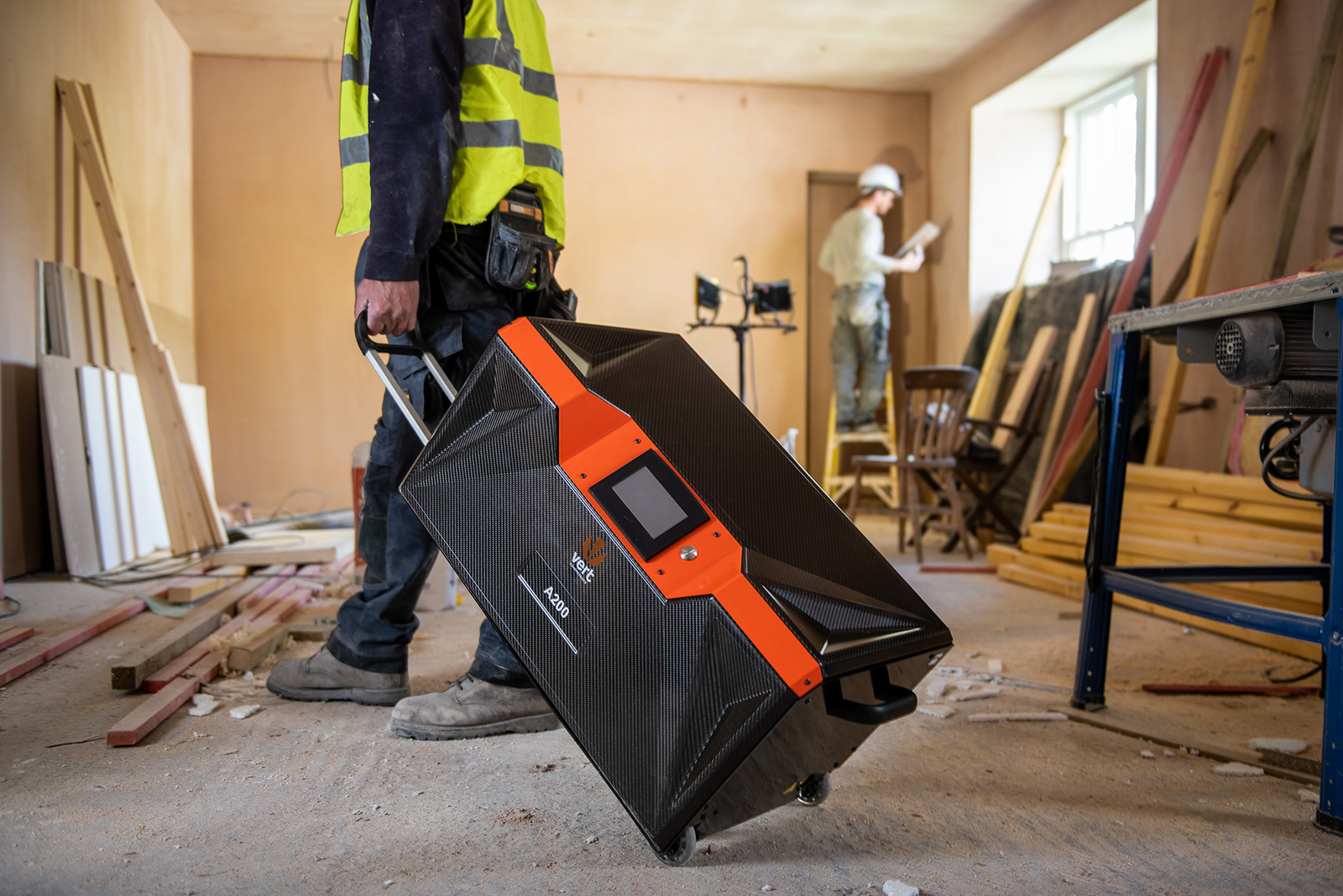
Nicol Low, COO at Vert Technologies, explores how new portable compressor technologies can help building professionals efficiently carry out works for longer with less noise pollution.
The ongoing COVID-19 pandemic has led to a strange situation for the construction industry. Though contractors and builders were some of the first allowed to return to work, and most have been extremely busy, social distancing restrictions on sites and in customers’ homes has made completing jobs harder.
But with these restrictions finally being dropped, the situation may change very quickly for those working in construction, with pent-up demand potentially leading to another boom in the sector. Consequently, it is vital that building professionals have confidence in the tools and utilities they need to carry out tasks efficiently and effectively. This is especially the case when we consider deadlines are becoming increasingly tight, and builders looking to bounce back from a COVID-impacted 2020 seek more work.
Traditional compressor issues
It is, therefore, vital that building professionals review areas that could lead to less efficient operations. Compressor units supplying air to hand tools is one such place, as traditional models can throw up multiple obstacles to continuous working, especially around noise and performance levels. Considering compressed air is vital for a wide variety of hand tools used in building work, including framing nailers, brad nailers, angle disc grinders, sanders and torque and impact wrenches, ensuring a reliable and quiet compressor unit is extremely important.
Specifically, because the traditional dry-running compressors used to power these tools are not designed with an internal cooling system, they are prone to dangerously overheating. This can result in a domino effect – resting the compressor so it can cool down affects its duty cycle, which in turn adds more time into the job and pushes build deadlines back. Worse still, contractors who are unfamiliar with the need to rest overheated compressors could use them continuously, eventually causing a breakdown and further disruption, not to mention the added expense of having to regularly replace a compressor unit.
The problem with noise
Noise pollution presents another concern for traditional compressed air units. Because traditional models use piston compressors to create high-pressure air, the action of the pistons accelerating and decelerating, along with valves opening and closing, can be very loud. These compressors often create noise between 92 and 95 decibels, exceeding the 65-decibel threshold for works up to 11pm, as laid out in Part 1 of the Code of Practice for Noise and Vibration Control on Construction and Open Sites.
Because of this, building professionals operating hand tools may be unable to work later into the evening, further impacting the ability to complete works on time. These concerns over noise also extend to operator health, with The Control of Noise at Work Regulations 2005 saying workers regularly exposed to noise levels over 87 decibels must wear ear protection. Traditional compressor units can therefore pose a risk to health, as well as project deadlines.
Conical rotary compressors
With this in mind, it is clear that new solutions are needed in the compressor space to avoid disruption and allow building professionals to confidently carry out work within specified dates. One innovation that could solve these noise and performance issues is the Conical Rotary Compressor (CRC) technology from Vert Technologies. Consisting of one rotor placed inside the other with both turning in the same direction to compress air as it travels down the conical screw, the CRC can deliver high pressures, alongside low-vibration and low-noise performance.
Crucially, unlike quiet rotary screw compressors that lose efficiency when used in smaller sub 2kW systems, the CRC can be scaled down without performance loss. Put into Vert portable compressor unit models like the new A200, which provides an air flow of 200lpm suitable for multiple hand tools, at 62 decibels – within the threshold required for evening construction work.
Its internal oil cooling system and separator, together with heat-responsive fan technology, also takes away overheating risks, instead allowing a 100 per cent duty cycle. When combined with the quieter, non-piston CRC design, this means building professionals can work continuously and without interruption with a long-lasting compressor unit.
In conclusion, the rush of activity the construction sector has experienced post-pandemic has made it vital that builders and contractors find ways to do the same quality work, faster. Air compressors are one area in which efficiencies can be made, with loud, low-performing traditional models being replaced by smarter solutions like the CRC technology.
For more information on portable compressor technology from Vert Technologies visit https://www.vertrotors.com/