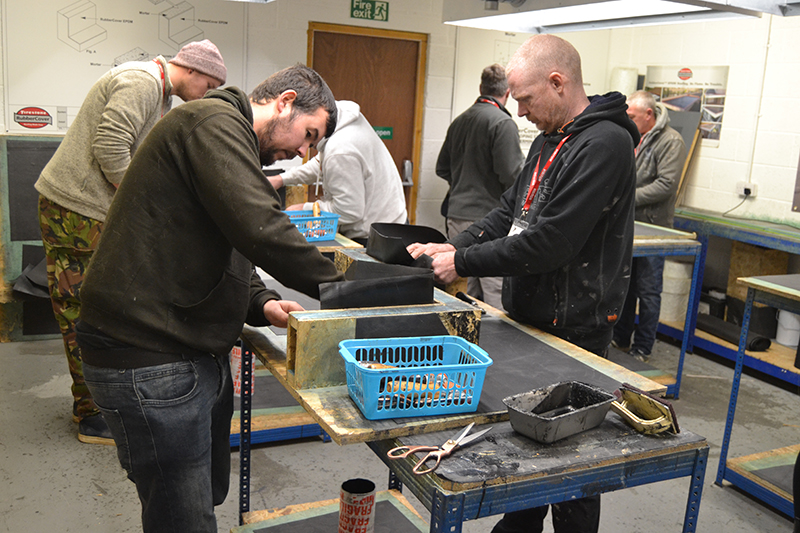
Get the rubber stamp from Firestone EPDM roofing experts Permaroof by attending one of the company’s training courses. Professional Builder’s Lee Jones finds out more.
One of the major motivations for any manufacturer to invest in training is to protect the reputation of its products – because install it incorrectly and the system itself could well take the blame. For precisely that reason, Permaroof, the UK’s largest distributor of the Firestone RubberCover EPDM roofing system, is a company that insists its approved installers do things its way. Indeed, its courses are now more than well established and, in the twenty years it has been training the roofing trades, more than 5,000 tradespeople and counting have now benefitted from its instruction and guidance.
Given that Permaroof’s MD and Chairman was himself a roofer, it is hardly surprising that his company wants to provide all the support it can to the end user – and champion the rubber roof concept in the process. A well-known product it may be, but the advantages of EPDM is still finding new followers, and taking market share from traditional bitumen solutions into the bargain.
Its cold application eliminates the health and safety implications of torch-on alternatives. Its resistance to temperature differentiation, ozone and UV radiation makes for an extended lifespan – with a 20 year warranty and over 50 year life expectancy on offer – whilst its flexibility and light weight make for straightforward installation. Add to that a perfect marriage with green roofs, or PV (photovoltaic) solar roofing and the case starts to become compelling. For the roofer, of course, any new technique is itself a business opportunity and, given that only tradespeople approved and trained by Permaroof can offer that two decade guarantee on an installation, embracing a new skill can quickly score on the balance sheet.
The Permaroof EPDM course attracts a mix of competencies, from those who have only experienced two or three rubber roof jobs, to the more knowledgeable. Whilst the product is designed as a one-piece system – with seamless sheets up to 15.24m in width and 61m long available – the devil really is in the detail. Our trainer, Rob, can command more than 30 years of rubber roof experience, and his main mission for the day is to initiate his learners in the art of ensuring a waterproof finish around roof furniture, as well as the likes of terminating at brickwork with the use of wall flashing trims, or at the fascia with the supplied back plates. All of these will present their own challenges but, once mastered, this is a system that has speed of installation and longevity in situ very much in its favour.
The floor mounted flat roof rig in the well-equipped and purpose-built training centre at the company’s Derbyshire head office and distribution centre features an OSB (Oriented Strand Board) timber deck, a material which is recommended in order to achieve smoother joints and a superior finish. Whilst there are two versions of EPDM, the Standard Grade at 1.14mm thick, and a Premium at 1.52mm, they are both laid in exactly the same way – the only difference being a warranty that rises to 25 years on the latter. A warm roof requires insulation and subsequent overboarding, but in either case Sterling board is the answer.
An EPDM Rubber Roof installation is a two-man job and trainees are split into pairs for the practical elements. Any building job is rather like driving a car – you might think you’re a master behind the wheel but bad habits are stealthy creatures, and the years can see them creep in unawares. Even the most experienced might benefit from a reintroduction with best practice, not to mention any new developments in the system itself.
Make use of your customer’s lawn to roll the rubber out to relax whilst you’re doing your prep work on the roof, for instance, and ensure that you are aware of just how to handle the adhesives and fixings needed to ensure a water-tight finish. For the main lengths, contact adhesive needs to be applied on both surfaces – board and rubber – but, as a water-based system, it should only be laid in an ideal temperature of 5ºC or more. It is instant grab, which offers no wriggle room in laying, and should be applied in the centre working outwards, before brushing the surface to achieve full contact.
The EPDM concept originated in the US, and has been developed to work with a specific and complementary class of adhesives, and for angle changes – such as around elevations – a contact bonding adhesive is the answer. The most critical areas will always be where tape is required and a large part of the course is dedicated to this aspect of a job. None of the Firestone-supplied tapes will adhere to the EPDM without the application of a primer, which is first brush-applied to the rubber and allowed to go touch dry. The amount of equipment required to install an EPDM roof is minimal but a 50mm seam roller – with the addition of 5mm penny roller for finer detailing – will do the job of fully adhering the tape to the primer-coated area of rubber.
Provided the technique is mastered, the seaming technology of the tape is well proven, and course attendees are taken through a full range of applications, whether it be circular dressing tape for use around an external corner detail, or directly applying primer to brickwork and adhering to brick, blockwork or lead – special adhesives are even now becoming available that allows application to tiles. Perhaps the most challenging aspect of the day for attendees is pipe detailing and considerable time is spent ensuring that the class is fully conversant with the approved method.
External and internal corners are also addressed, and in every instance the aim is to ensure a water tight seal. Firestone has been utilised in major projects where the material is fully submerged in water – so get the installation right and the vagaries of the British climate will present no problem.
Once the course is complete Permaroof prides itself on the amount of support it provides installers in the field. Not only that but the training team can also undertake courses at other locations, whether that’s on site or at a builders’ merchant.