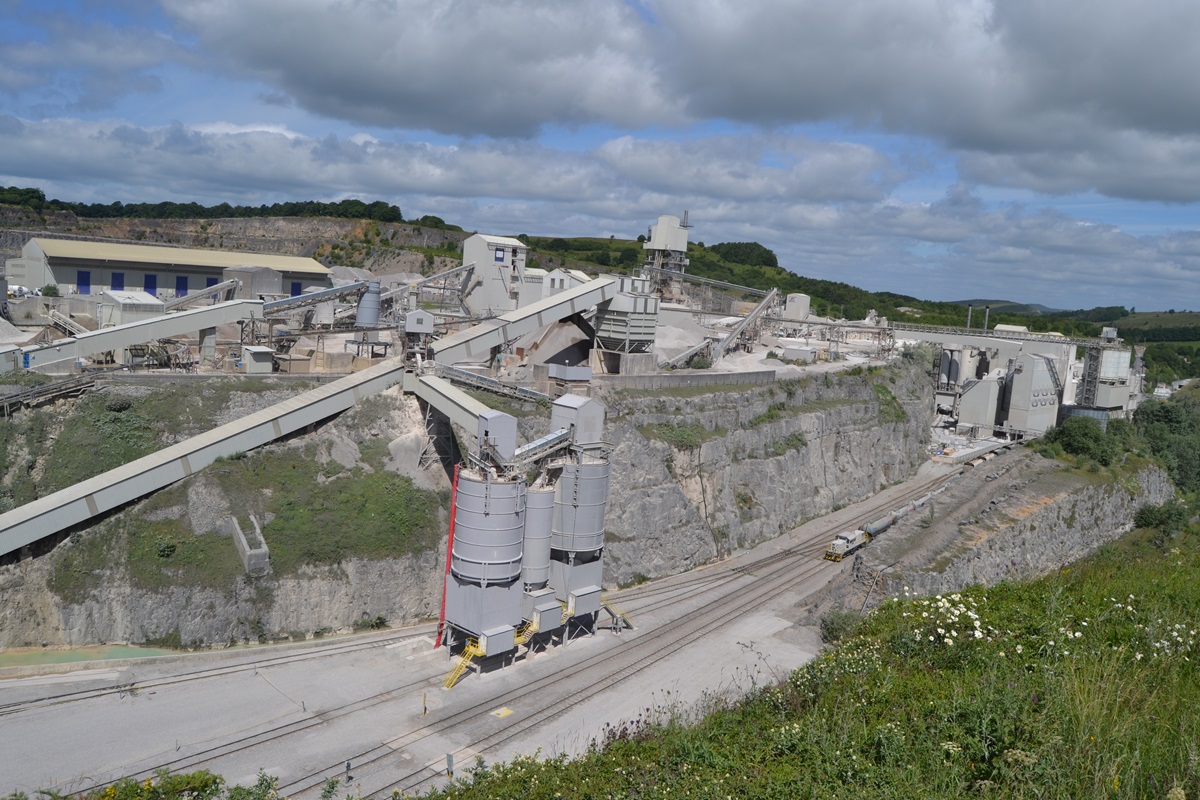
Given the ubiquity, longevity and heritage of the iconic Blue Circle cement brand it demands an industrial process to match and Tarmac’s Tunstead Quarry certainly delivers.
It is here that the manufacturer’s leading cement products make the entire journey from raw material to packaging, and the scale is truly awe-inspiring. It is the biggest plant of its kind in Europe, covering 340 hectares of the Peak District, and four times the size of nearby Buxton.
The unique quality of the Derbyshire limestone that has undergone 350 million years of geological processes to form has always been highly prized, and there has been a cement plant at Tunstead since as far back as 1890. Whilst its current operators are following in that fine industrial tradition, they are equally aware of their environmental responsibilities. As each level of the quarry ceases production natural habitats are restored, ensuring that the present-day custodians of this ancient landscape continue to work in harmony with this area of outstanding natural beauty.
On our visit, enough material was carefully blasted from a rock face in a single controlled explosion to satisfy just under one week’s production. Giant CAT 992 Wheel Loaders and the similarly imposing 100-tonne CAT mining trucks transfer that material for crushing. The site is serviced by no less than five railway sidings, dramatically reducing the number of trucks needed on the road, and the consequent CO2 emissions.
The guiding principle of Tarmac’s bagged products is consistency, and the chemistry is as precise as it is complex. From drilled samples before blasting to quality testing at multiple points, cement is required to meet exacting strengths. At the same time its ingredients are now engineered to reduce CO2 output wherever possible without impacting on performance. That’s a theme that is continued with the considerable amounts of energy that are required to power the site’s ferocious kiln. Here, Solid Recovered Fuel (SRF) – which is largely derived from residential and commercial bin bag waste that would otherwise be destined for landfill – is a far more environmentally friendly alternative to fossil fuels.
The Tunstead operation is also a demonstration of the circular economy in action. The crushed limestone has to be washed and the waste slurry is then recycled. Limestone is mixed with the other components of cement, including clay, shale, sand, iron ore and bauxite and ground in a mill armed with many thousands of steel balls until it is reduced to particles of no more than microns in size. Another ingredient – blast furnace slag – which is a by-product of the steel industry, reduces the amount of limestone required and, as a consequence, the embodied CO2.
The material is then moved past heat exchangers that expose the mix to 500ºC before it enters the real heart of the process – the kiln. It is here that a 12metre long flame generates a consistent and positively volcanic 1,500ºC temperature along this rotating steel tube’s entire length. This produces a chemical reaction between the ingredients, and a transformation into an entirely new material – clinker. The cement plant is fed by a constant supply of clinker from two huge silos. These grey nodules are then cooled down very quickly to 100ºC before being mixed again and milled to a fine powder.
Energy saving
Cement manufacture is an energy intensive process and it’s a reality that manufacturer’s such as Tarmac are acutely aware. What is evident from the work at the Tunstead facility is that careful thought has been given to address the issue at every stage. Whether it’s championing rail transport, using blast furnace slag, or targeting zero waste, whatever can be controlled has been. Added to that is the introduction of Portland Lime Cement (PLC), a blended product with an increased limestone content, and less clinker, that can reduce CO2 outputs by up to 10%. It is envisaged that this will ultimately replace CEM I as a more environmentally friendly option without any detriment to performance.
At the same time, it’s not all about brute industrial force because there is technological brains at work. A robot affectionally known as ‘Jack’ takes up to 150 quality control samples a day to ensure every bag of cement is as good as the last. A control centre allows two operatives to watch over the entire process, including the UK’s most efficient packing plant.
Tarmac is the market leader in terms of Packed Cement & Cementitious products in the UK and the Blue Circle brand remains synonymous with quality and trust. Tarmac also offers the widest range of Packed Products in the UK, offering customers a full range of aggregates, bituminous products, ready-to-use and specialist solutions, most of which can be sourced from merchants. Tunstead is also the home of Quick Set Concrete and Postcrete. The latter was introduced more than 20 years ago as a first of its kind and is testament to a long-standing commitment to innovation. Indeed, the Tunstead quarry itself speaks eloquently of a company that is dedicated to adapting its processes to satisfy customer demand and safeguard the environment.
For further information on the Tarmac range of packed building products click here