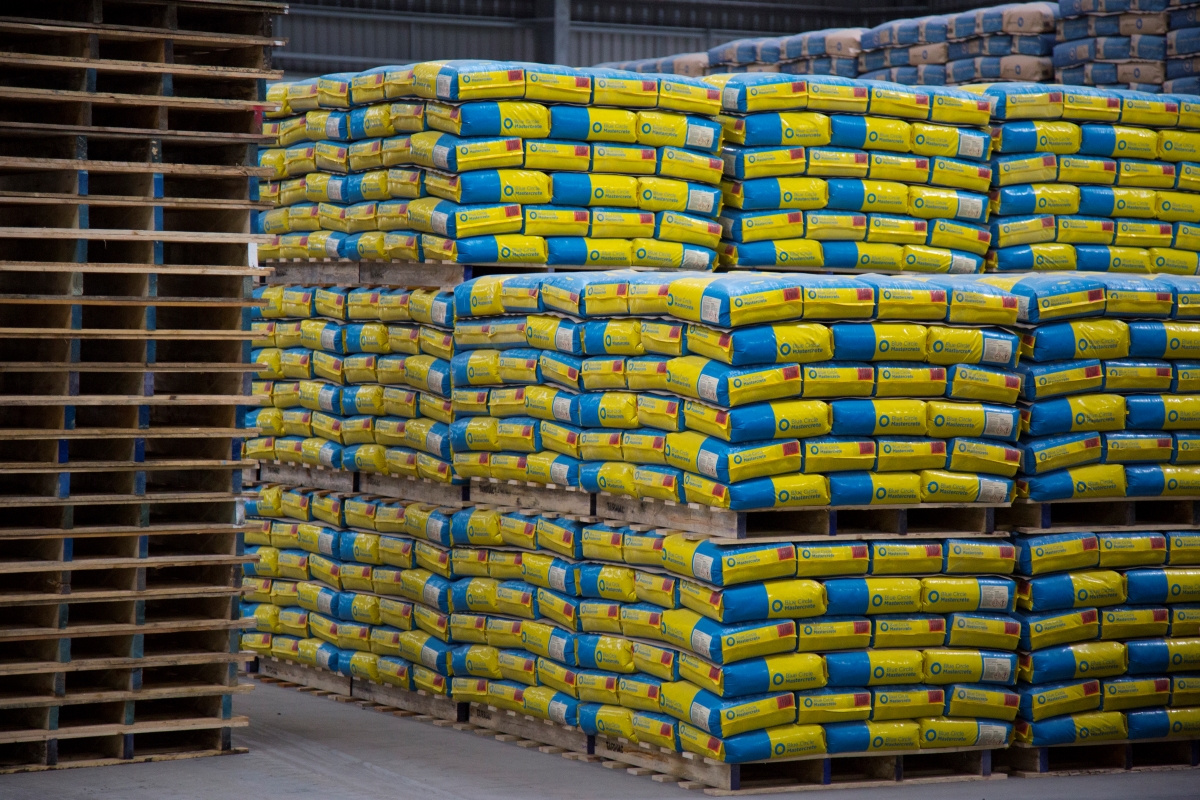
Garry Gregory, packed products director at Tarmac provides insight into the industry’s perspective on sustainability and the five key pillars that underpin it.
Production
Sustainable production of cement involves a multifaceted approach aimed at minimising environmental impact across the entire process. It encompasses implementing energy-efficient technologies, optimising raw material extraction, minimising waste and reducing carbon dioxide emissions. Moreover, embracing alternative fuels such as biomass, waste-derived fuels or electricity throughout the production stages, not only reduces reliance on fossil fuels but also contributes to lower carbon emissions.
At Tarmac, we are optimising our manufacturing at each site so we can make improvements where required. This includes introducing alternative fuels to remove the need for fossil fuels during the production stage.
In 2022, Tarmac introduced the UK’s first battery electric mixer truck as part of our commitment to net zero. As Tarmac procures 100% of its site electricity from clean energy sources – wind, solar and hydro power only – the new vehicle operates as a carbon neutral solution. Since then, we’ve continued to build on this. In fact, by the end of 2024, Tarmac will be on track to operate the largest electric HGV fleet in the UK construction sector.
In addition to making the transition to zero tailpipe emissions, electrification can reduce noise and vibration, while contributing to improving air quality, particularly when operating in urban areas and low and zero emissions zones.
Process
The concrete and cement sector currently accounts for seven per cent of global carbon emissions, predominantly from the chemical reaction that creates cement and the energy required to do so. However, the industry must also look at the bigger picture. Applying automation, reducing physical administration and optimising digital solutions will substantially reduce the carbon footprint of product collections and deliveries in a way that is streamlined, robust and easy to use.
For instance, our roll out of electronic payments by customers removes manual intervention and taking paper out of the process and electronic proof of delivery (EPOD) is reducing the number of vehicle movements and time spent on site. In turn, this reduces the amount of carbon emissions during the processing stage.
Additionally, sustainable processes focus on waste reduction and recycling initiatives, ensuring that by-products and waste materials are utilised effectively rather than being sent directly to landfill. By embracing sustainable processes, the cement industry can achieve a balance between economic growth and environmental stewardship, paving the way for a more resilient and environmentally conscious future.
Product
In the cement industry, sustainable products are often characterised by stringent environmental standards and their capacity to minimise carbon emissions throughout their lifecycle. Such products typically adhere to certifications like BS8500, ensuring they meet specific criteria for reduced environmental impact.
Sustainable cement products often incorporate alternative materials or additives that reduce the clinker content, a primary source of carbon emissions in cement production. Moreover, innovative formulations and manufacturing processes aim to enhance durability, longevity, and performance while minimising resource consumption and waste generation. By prioritising sustainability in product development, the cement industry strives to offer solutions that not only meet construction needs but also contribute to a more environmentally responsible built environment.
One key step on our route map is to move all ready-to-use Blue Circle products from CEM I to CEM II over the next 12 months. This will deliver up to a 15% reduction in CO2 emissions.
However, alongside creating more sustainable solutions, it’s important to consider how they are packaged and transported. When done correctly, very little product will get damaged during transportation and end up going to waste.
Packaging
There are very few materials more present in packaging than plastic. In fact, 34 per cent of the 90 million tonnes of construction waste generated each year is derived from materials used to package products and materials.
However, the focus on sustainability extends beyond just reducing waste. A plastic packaging tax (PPT) was introduced in April 2023 to incentivise businesses to use recycled plastic in packaging. This means that companies that manufacture in the UK or import into the UK at least 10 tonnes of plastic packing within a 12-month period need to pay PPT.
At Tarmac we’ve recognised the need to go beyond just meeting regulatory requirements and are actively seeking ways to reduce our environmental footprint. We were the first cement manufacturer to produce 50% recycled bags, and we’re actively working towards developing a net-zero packaging solution within the next few years. By prioritising the use of recycled materials, we’re not only reducing our reliance on non-renewable resources but also minimising our contribution to the growing issue of plastic pollution.
Placement
The placement and transportation of cement requires reinventing traditional delivery methods, reducing road deliveries, and expanding the use of alternative fuels.
Across our Tarmac business we have made great strides transitioning the mode of transport from road to rail wherever feasible thus reducing overall road deliveries. To further supplement this, we constantly strive to maximise the amount of product we deliver on every vehicle. As an example, in our Packed Products business, by working closely with our hauliers and customers, and through clever logistics planning, we have increased our delivery load fill by c.10%, which has taken 1,400 deliveries off the road every year. When vehicles are delivering our products, we then work closely with our hauliers to ensure their impact is minimised, by encouraging the use of alternative fuels and the adoption of efficiency technologies.
Alongside this the industry should be embracing positive change by taking advantage of opportunities, such as circularity of pallet use which promotes the reuse and recycling of pallets, in turn reducing waste and minimising environmental impact.
One thing is clear, achieving net zero can only be achieved by looking at every area of a business. Reaching net zero carbon emissions will require more than just a commitment from cement and concrete manufacturers, these efforts also need the collaboration of the wider construction industry, academia, government bodies and customers across the entire value chain.
Tarmac Blue Circle is now offering more support to its customers through its brand-new website. For more information visit www.tarmac-bluecircle.co.uk.