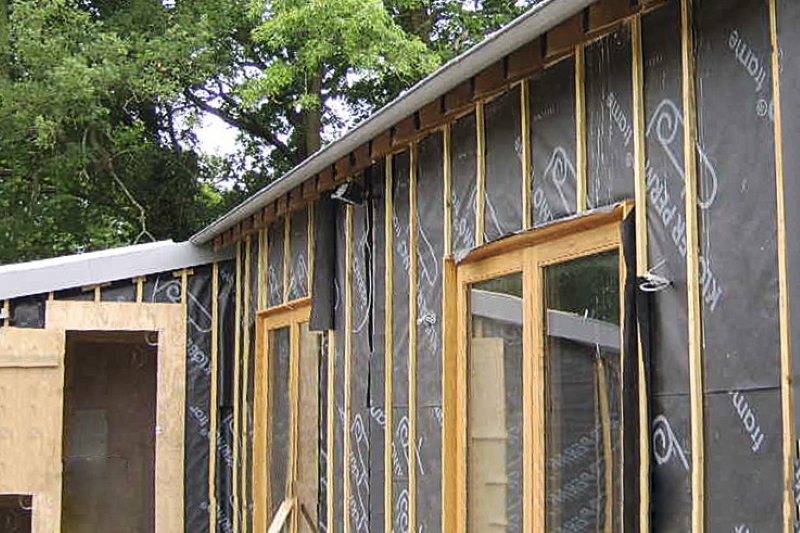
Klober writes how the UK timber housing boom could pose a health threat if air and moisture movement is not addressed at specification.
With the UK’s construction market set for change after the three largest housebuilders revealed plans to open dedicated timber frame factories, construction professionals are being urged to balance air tightness with ventilation at specification.
Klober is encouraging professionals to consider how components perform together to achieve air and moisture tightness while preventing condensation build-up. It comes ahead of anticipated growth for the UK timber market, in pursuit of net zero emissions.
Nick King, Portfolio Manager at Klober said: “Efficient buildings are the future. From a bill payers’ perspective, you don’t want to be paying to heat your property, for it to go straight out of the walls or roof. And from an environmental standpoint, preventing air leakage is a key priority. Therefore, construction professionals must carefully consider how they deliver homes that are efficient.”
The timber construction market continues to grow due to the speed of construction and the environmental benefits that timber presents, such as the ability to absorb carbon emitted during production. According to recent statistics, 92 per cent of new build properties in Scotland are timber constructions, and the rest of the UK is predicted to go in a similar direction.
“For a more efficient building stock, we need properties that are thermally efficient at their core,” said Nick. “In timber frame, this can be achieved by the selection and detailing of the internal membrane. When selecting roof and wall membranes, ensuring air leakage is reduced is important. That’s why opting for supporting accessories to create airtight seals around any openings or penetrations is also a crucial consideration.”
“However, this must also be balanced with ventilation. Failure to ventilate could cause internal condensation build-up in the roof space and wall cavities – which can be detrimental to occupant’s if they have prolonged exposure.”
British Standard BS 5250: ‘Code of practice for control of condensation in buildings’ stipulates rules for avoiding problems of high moisture levels and condensation.
“Maintaining a balance between air and moisture tightness and the right ventilation is essential. From a building fabric perspective, this can be achieved by opting for a vapour permeable membrane that allows the wall structure to breathe, while keeping it windtight and draught-free.”
For more information about Klober’s wall membrane, please click here.