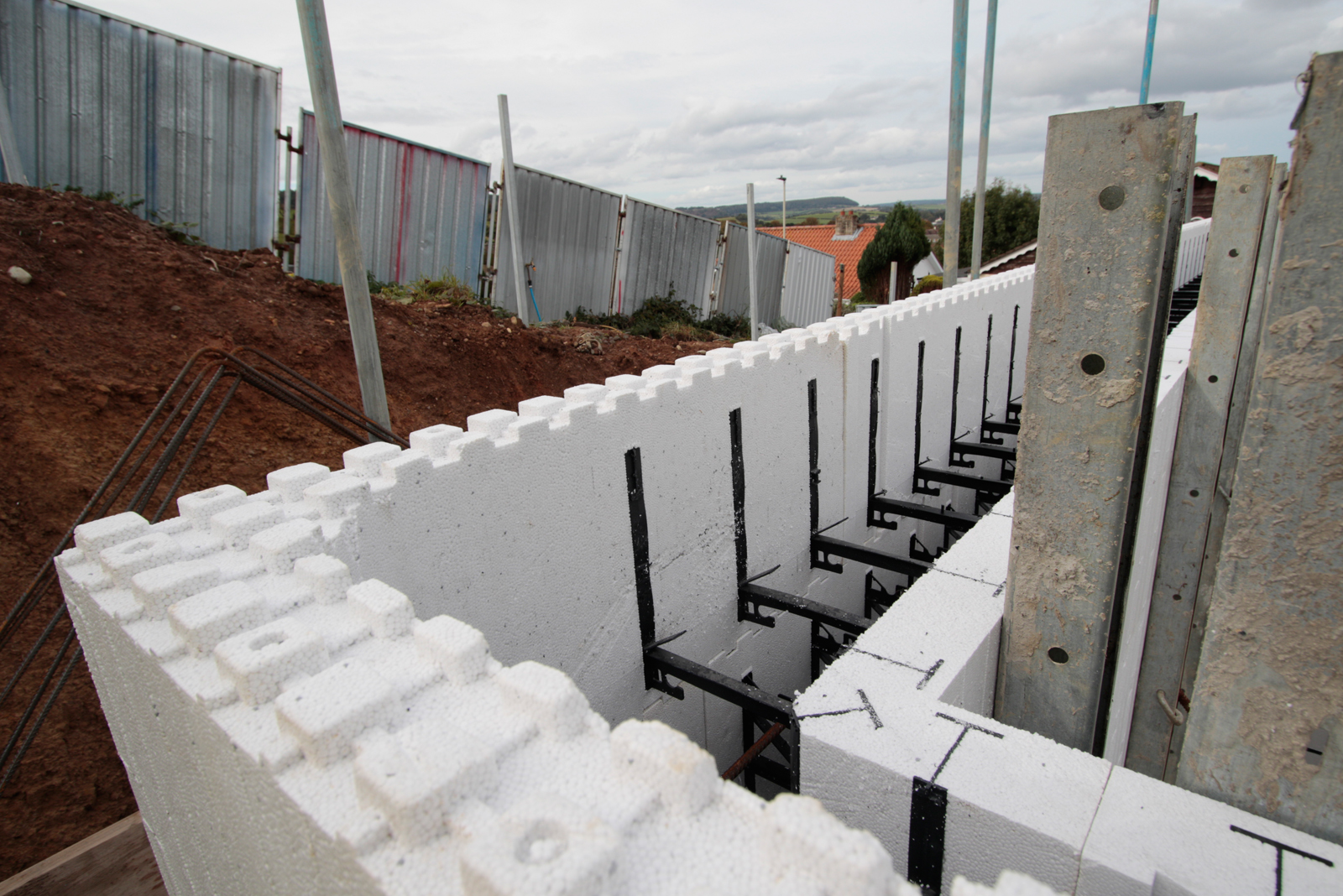
Jackon Building Systems has been selected for the first ever ‘Passive House Standard’ dwelling in Scarborough.
The manufacturer of insulated concrete formwork (ICF) solutions was chosen for both the foundations and external walls to help achieve Scarborough’s first ever passive house standard private dwelling, achieving a net positive, zero energy home.
Designed by Architects Samuel Kendal Associates, this three-storey sustainable family home is embedded deep into the Scarborough Hillside, and comprises a semi-submerged basement housing a garage and music room, a lower ground floor for three large bedrooms and a top floor consisting of a large open plan kitchen and living spaces.
The company’s Jackodur Atlas raft foundation and Thermomur ICF, were the client’s preference and were chosen for their versatility, energy efficiency, speed of construction and cost effectiveness to help them achieve their aims of becoming net zero.
The specialist ICF contractor Bondmor, working closely with the ICF manufacturer, and the leading approved distributors in the North of England ICF Building Solutions, utilised Jackodur Atlas for the foundation of the build. Bondmor and ICF building solutions worked hand in hand with the architect and the clients prior to construction to design the building around the systems to minimise wastage and increase on-site efficiency. Jackodur Atlas was the ideal choice, as a zero waste, fully bespoke, cut-to-size foundation system helping achieve U-values of 0.12 Wm²K and a compressive strength of 500 kPa. The design of the XPS system assisted the contractor in constructing the foundation in a matter of days, eliminating all thermal bridges whilst maintaining high performance insulation values with zero waste.
Thermomur’s 350HD blocks were utilised for all the subterranean lower ground floor walls. Selected for its 200mm concrete core paired with its energy efficient properties (U-value 0.22 Wm²K). Bondmor were able to construct the 6m retaining ICF walls quickly without the need for additional structural support from further retaining methods, saving the client time and money. The blocks were externally clad with the same manufacturer’s 100mm XPSK300 to seamlessly line up with the Thermomur 450 blocks above in order to achieve a U-value of 0.09
Chosen for its high-performance insulation values and its cost effectiveness compared with other similar building systems, the above ground exposed walls were installed with Thermomur 450 achieving U-values of 0.11 Wm²K. This wall structure far exceeds the requirements of today’s Building Regulations and surpasses Passive House Standards (U-value 0.15 Wm²K).
Bondmor were able to effectively construct the ICF walls and openings to allow for ease of follow-on trades. Pockets were built into those walls to allow for the universal beams to support the block and beam floor structure, openings were squared and formed to pre-determined window dimensions. This allowed the client to reduce the lead time on the window manufacturing and installation. Gable ends were cut to precise angles to allow structural bearing for the SIPS roof panel. Penetrations were installed for all service locations prior to concrete placement. The ICF systems the company produces are metric dimensions with internal and external fixing points running vertically through the blocks every 150mm.
The system took just 27 days to construct, and the clients were very impressed with the speed and efficiency involved. ICF construction is fast becoming a widely recognised modern method of construction for developers and self-builders. It integrates both insulation and concrete in one permanent formwork solution that provides many offsite, onsite and end-user benefits. These include high performance insulation values and significantly improved airtightness, leading to reduced heating and cooling requirements, excellent acoustic performance, improved fire resistance, enhanced capabilities in extreme weathers with added benefits of reduced maintenance, as well as being accepted by mortgage lenders, home insurance and planning departments.
Jackon brings over 60 years’ expertise in EPS and XPS manufacturing to this market. Jackodur Atlas is manufactured from XPS (extruded polystyrene), while Thermomur uses EPS (moulded expanded polystyrene) to create the formwork. The two systems fully integrate, leading to a reduction in the need for extra on-site labour.
For further information on the range of Insulated Concrete Formwork (ICF) solutions from Jackon visit https://www.jackon-insulation.co.uk/