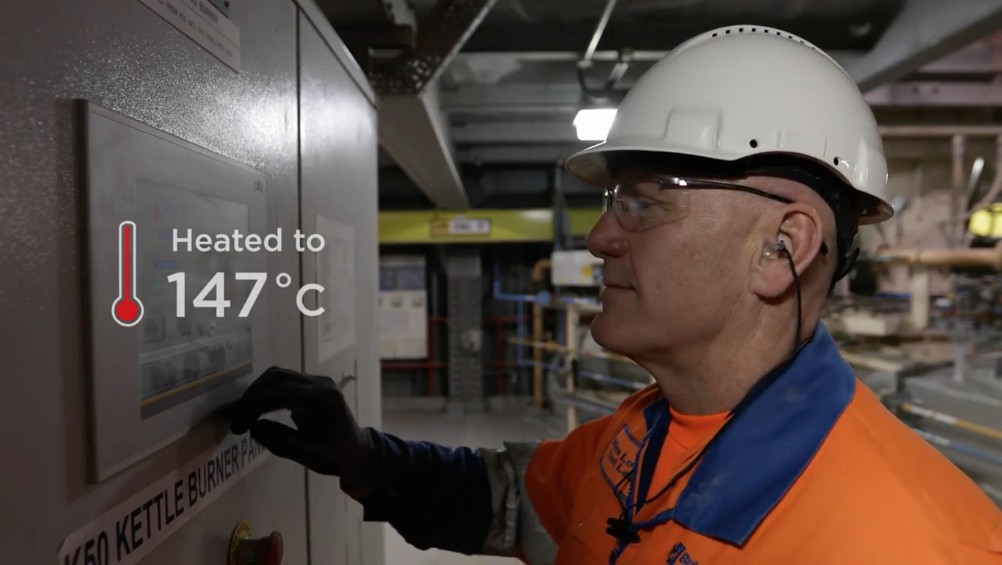
In our new series from British Gypsum, we explore the different ways a manufacturer contributes to an installer’s objective of doing a great job. First up, we take a peek inside the mines and learn more about the process of making its plaster products a reality – meeting two mining heroes along the way.
The process of producing gypsum products from rock to room is fascinating. With mining operations dating back to 1876, British Gypsum now operates three gypsum mines across the UK that specifically support the manufacturing of plaster. The plant at Barrow-upon-Soar in Leicestershire is the largest and most technologically advanced plaster plant of its kind in Europe. Since it first opened in 1992 it has the capacity to supply one million homes with plaster in a year. The plant at Kirkby Thore, Cumbria has been manufacturing Thistle plasters and plasterboard continuously since 1910 while British Gypsum’s third plaster plant is located on the same site as the company’s Head Office in East Leake.
To get a feel of what it’s like to work at a British Gypsum mine we spoke to Senior Mining Engineer, James Davies from the company’s Central Geological and Mining Services Department and Mine Production Manager, Alex May who works at the company’s Kirkby Thore site. Together, they have over 50 years of mining experience and are better placed than most to offer an insight into what it’s like to work for British Gypsum, what life is like working in a mine and how the process of manufacturing plaster has changed over the past 100 years.
Plaster starts its life 300ft underground, where it was formed 180 million years ago, and ends up on the walls of our homes. Here, James Davies explains the operation in simple terms: “To begin with you need a source of gypsum – in the UK most of the gypsum deposits are underground and require mining.
“Once we’ve extracted the gypsum from the mine using a continuous mining machine, we must crush it below ground into a manageable size before we can move it to the surface. This is where we grind it, ensuring it’s reduced to a fine powder. After that, we heat it in order to remove any remaining water – a process known as calcination. Once this is done the product is now in a state commonly known as ‘Plaster of Paris’. We have the ability to grind the plaster to different levels of fineness, as well as the option to insert additives to modify the workability and performance of the finished product before it moves onto the bagging process.”
James and Alex have multiple responsibilities in their job, but their primary focus is always safety. Speaking on the importance of protecting staff, Alex commented: “Mining is a hazardous role, so it’s essential that safety is always top of our priorities. We’re constantly striving to improve our operations, but also have to ensure we’re hiring competent people who will be able to approach the procedures with the necessary judgement.”
For James, no two days on the job are the same: “I’m constantly doing different things, to the point where it’s almost impossible to say what an average work week looks like. One day I might be exploring gypsum reserves to make sure we have continuity of supply and then the next I might be looking at the remediation of sites.”
It’s similar for Alex, who enjoys the varied nature of his job and the environment in which he works: “Every day is different, there’s a lot going on in the mine and it’s important I have a grip on the various aspects of the operation. Taking this approach means I can become better acquainted with my fellow team members. I only recently joined British Gypsum and already I have sensed a real level of camaraderie throughout the team and it has blown me away. I’m really impressed with the people and how engaged and involved they are at every stage of the process.”
As experienced mining professionals, James and Alex will have noticed the improvements and upgrades to mining processes over the years. By modernising practices and introducing new machinery the job of creating plaster has become much more efficient and safer. With British Gypsum having celebrated its 100th anniversary last year, we asked both how they feel the industry has transformed over that time.
For James, the changes have been very noticeable: “There has been a massive shift in the last 100 years. When British Gypsum first formed, mining was a labour intensive job and almost everything needed to be completed by hand. There has been a lot of money spent on modernising practices and we’re in a position where a lot of mining tasks are now operated by machinery. There have also been massive improvements made in safety.”
Alex agrees that there have been big advances in the field, but admits some things never change: “The principles remain the same, but it has become much safer. In comparison to the beginnings of the industry every process has had technology embedded within it, which has made the sector less dangerous and more efficient. It has not happened by accident, there has been a huge investment made by companies such as British Gypsum and the Saint-Gobain Group in both people and equipment and we’ve all benefitted from that.”
Together James and Alex are contributing to the world-class operations across British Gypsum’s sites. The company became the first UK gypsum manufacturer to achieve BES 6001 ‘Very Good’ rating, which increased to ‘Excellent’ in 2014. In 2018, it was once again named a Business Superbrand.
With over 100 years’ experience in plaster, British Gypsum supplies over 3,500 stockists throughout the UK. Skilled tradespeople use these products to create unique, welcoming and practical spaces.
For more insight into the plaster mining process, watch British Gypsum’s video.