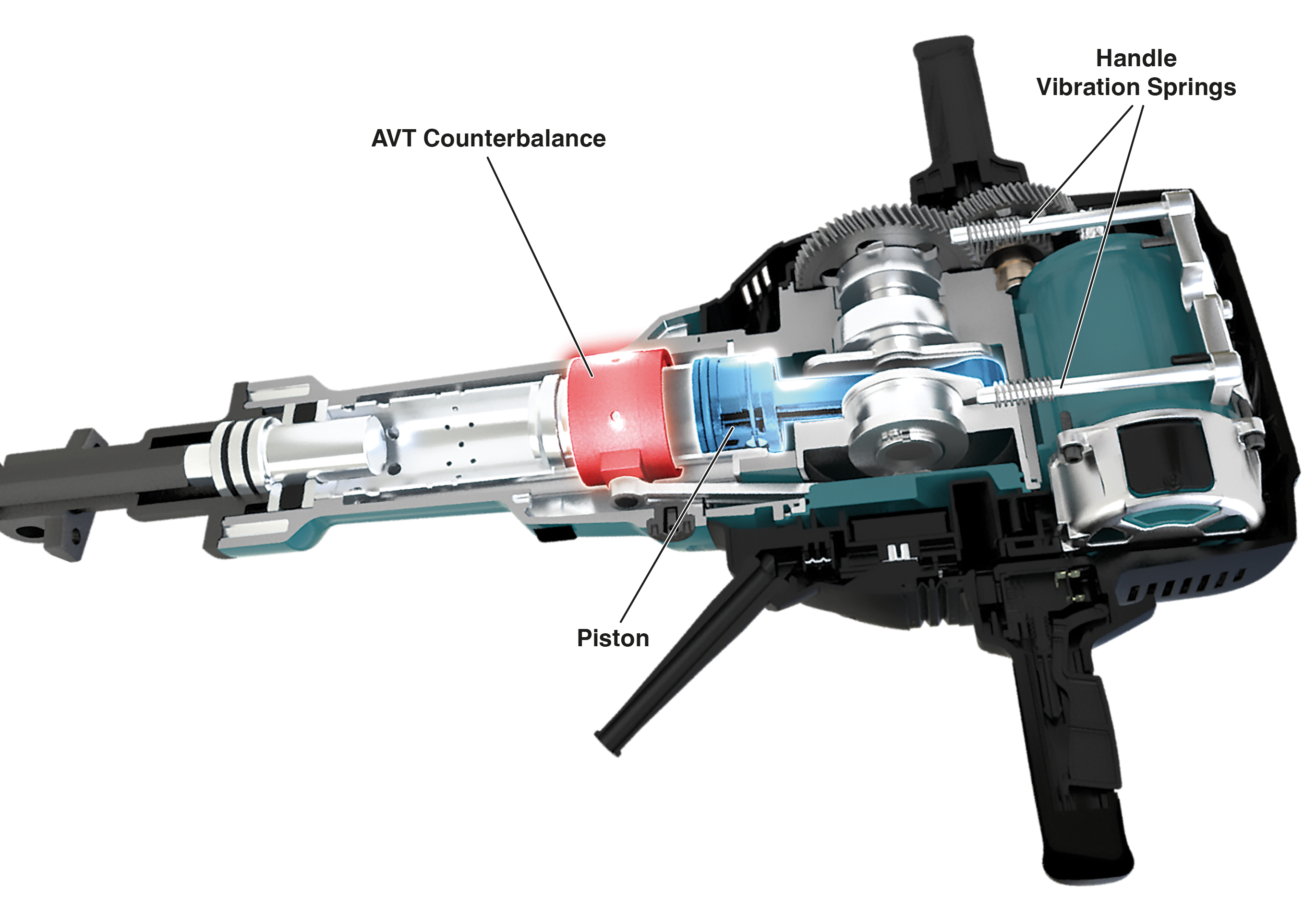
In the latest part of our series on power tool technology, Charles Shaw at Makita looks at the dangers of vibration and the innovations that allow tradespeople to reduce their exposure.
All power tools produce some level of vibration when in use. This is typically much higher for tools such as reciprocating saws, rotary hammer drills and breakers where the nature of the machine’s action exposes the user to increased vibration. Frequent or prolonged exposure to high levels of vibration can cause a number of health issues including permanent bone damage and Hand Arm Vibration Syndrome (HAVS), which encompasses conditions such as Vibration White Finger and Carpal Tunnel Syndrome. Sufferers commonly experience painful, tingling or numb fingers and hands as a result of damage to the nerves and blood vessels. It can also result in weakened muscles, lower grip strength and reduced dexterity, which can make day to day tasks increasingly difficult both in the workplace and in domestic and social environments.
Since July 2005, when the Physical Agents Directive became law, manufacturers had a duty to advise the users on the expected vibration emissions through the tool’s intended usage. This level and the usage time are then used to calculate the daily exposure (given in points) in line with the guidance given by the Health & Safety Executive (HSE). The Health and Safety Executive has set two levels, the Exposure Action Value (EAV) at 100 points and the Exposure Limit Value (ELV) at 400 points. For some tasks and tools just 15 or 30 minutes of trigger time in a day will place you above the EAV where steps need to be taken to reduce the exposure to vibration and as little as an hour per day may exceed the ELV.
However, to help address the risk, many modern power tools feature technology designed to significantly reduce vibration and so reduce the risk and improve performance and productivity from the tool usage. For example, tools within the Makita range feature Anti Vibration Technology (AVT), a combination of innovations that operate together to reduce vibration while, in many cases, increasing the effectiveness of the machine.
Rotary hammer
For example, in a rotary hammer, a piston within the machine is used to deliver the percussive force to assist with drilling into or chiselling masonry and concrete. Without measures to counteract this force it can produce high levels of vibration. The Active Dynamic Vibration Absorber mechanism found in Makita’s AVT rotary hammers works by transferring air around a series of chambers which, in turn, pushes a counterbalance in the opposite direction to the piston. This cancels out the energy of the piston that would otherwise cause the vibration.
The AVT system also features a dampener spring, which absorbs the reaction force of the striker bolt impacting inside the machine. The final element of Makita’s AVT is the vibration absorbing housing. The connection point between the handles (both main and side handles) and the body of the machine have been engineered to prevent the vibration being transferred to the user. Springs integrated into the handles, cushion the force and mean that the user is effectively isolated from the movement of the machine.
The Makita AVT breakers and demolition hammers feature similar technologies. The counterweight mechanism and vibration absorbing housing off-sets and isolates the force produced by the machine to reduce the damaging vibration. The ‘soft no load’ function also automatically lowers the motor speed when idling to reduce vibration of the tool body. This further decreases the amount of vibration transferred to the operator’s hands over the course of a day and helps minimise the deflection of the chisel bit from the aiming point when chipping.
A good example of how this innovative technology benefits the user can be seen in the new HR4013C. This rotary hammer incorporates the AVT technology, which reduces the vibration levels by 80 per cent compared to previous models to only 4.5m/s2 and increases impact energy by over 50 per cent. The Exposure Limit Value of the HR4013C is a staggering 9hrs 53mins of constant trigger time.
The dangers posed by vibration should not be underestimated, especially for those operating tools for extended periods of time. The risks can be managed through a combination of reducing time on the tools, job rotation where possible and selecting tools that include features to lower the vibration levels. Ultimately, reducing the amount of vibration you are exposed to during the working day can help improve productivity as it increases the amount of time the tools can be operated safely.
Check out Makita’s vibration calculator.