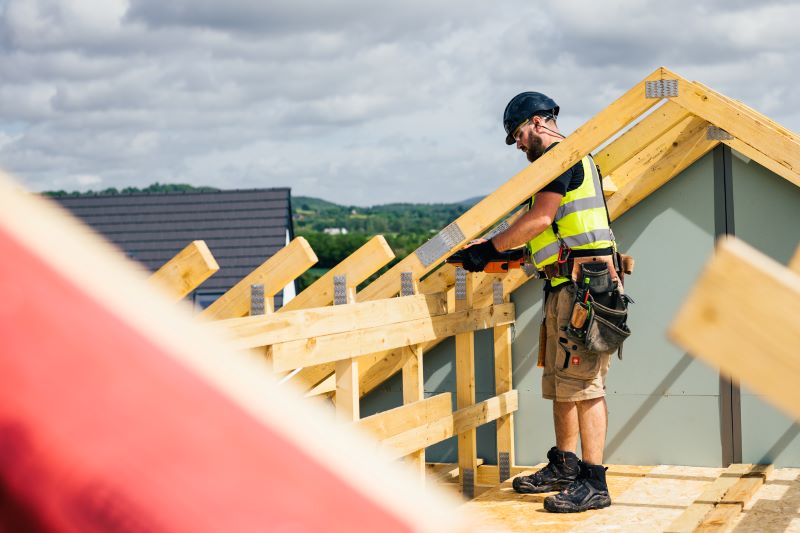

Liam Hale, construction director at Taylor Lane Timber Frame, explains more about timber frame as a modern method of construction and how it can save SME and micro builders both time and money.
Timber frame construction is increasingly popular with larger house builders and developers due to the many associated benefits, but did you know that these benefits can be appreciated whether you are building one or one thousand homes?
But first, what is timber frame construction?
Timber frame is an offsite construction method. This means that many of the elements – the walls, floor and roof – are precision-engineered in a factory-controlled environment, which avoids delays caused by inclement weather. Often the manufactured panels also include a membrane and insulation to help achieve the desired thermal performance. The component parts are then delivered to site for erecting.
What impact will this build method have on your business, overheads, and schedule? Let’s outline some of the advantages…
It’s fast.
Over the years timber frame construction has been synonymous with speed. It’s a fast yet high quality build method. Using timber frame can speed up the build programme by about a third. With organisation, a three-bed house can usually be air- and water-tight within a working week. It also enables other trades to start work inside the property before the brickwork is complete. This makes for a more predictable build programme and can help reduce costs.
It’s green.
Furthermore, as attitudes change and demands for better quality housing resonate across the land, timber frame is now valued for its environmental credentials. Much of this is down to sustainability. Timber is the only truly renewable building material and reputable suppliers will only use timber from PEFC or FSC certified sources. Typically, for every tree cut down, three or four are replanted.
Timber also has the lowest CO2 value of any commercially available building material. Trees capture the carbon and isolate carbon dioxide. This is retained inside the timber throughout its life as a structural building material, and beyond if recycled!
It’s future-proof
Timber frame is highly engineered and can offer extensive design flexibility. It lends itself to an abundance of tastes and property styles enabling you to meet most structural and visual requirements while adhering to the appropriate standards and regulations.
What’s more, smart design can future proof a property. Whether you are building a home for yourself, a one-off client or a small development, work with the architect to create an adaptable lay-out. Knock-out panels can be added for flexibility – turning a fourth bedroom into a walk-in wardrobe and dressing room for a master bedroom, for example. Or, with a knock-out panel and the foresight to use attic trusses, an integrated garage can easily become a room in the roof.
It’s accurate.
With optimised cutting technology timber frame doesn’t just save you time and labour onsite it also reduces skip waste. Our current wastage in production, for example, is between eight and 12 per cent, and we are constantly looking at ways to reduce this further. 100% of this is then diverted from landfill. Ultimately, our efforts and those of other timber frame manufacturers cuts down the number of skips required onsite which saves you money.
It’s energy efficient.
Perhaps now the most pertinent benefit – a property built with timber frame will remain warmer throughout the winter and stay cooler during the summer months. It can heat up quickly and retain that heat for longer. As a natural insulator, timber, when used as a build method, can help to reduce running costs and energy bills. For best results, set the required thermal performance early in the project. This will help determine the level of insulation needed.
And remember – it is far easier to achieve a low U-value (the measure used for thermal transmittance) with timber frame than traditional build methods. It can even go beyond Building Regs without filling the cavity!
SME Developer
Kinspire Homes is a SME developer based in Herefordshire. They are currently onsite with their fifth development comprising five houses and four house types, and a sixth site is being purchased. They have been a committed user of timber frame since day one…
“We went into our first project knowing that it was going to be a winter build,” says director, John Parker. “Speed was critical if we were to stay on schedule and within budget. We needed the properties to be dry as soon as possible, this meant looking beyond traditional build methods.
“We quickly identified timber frame construction as the solution, having weighed it up against the time taken to build in traditional brick and block, cost of brickies etc.
Kinspire are now building their fifth development and “…To be honest, it’s unlikely that we will go back to traditional building,” continues, John. “The speed and accuracy of timber frame has been extraordinary. The dimensions are pretty much spot on every time.
“We are proud to show prospective buyers around when the properties are under construction. They are able to see the quality for themselves, especially the timber frame which isn’t something you can see normally.”
For further information on Taylor Lane Timber Frame visit The Home of Taylor Lane | UK’s Leading Timber Frame Specialists (taylor-lane.co.uk).