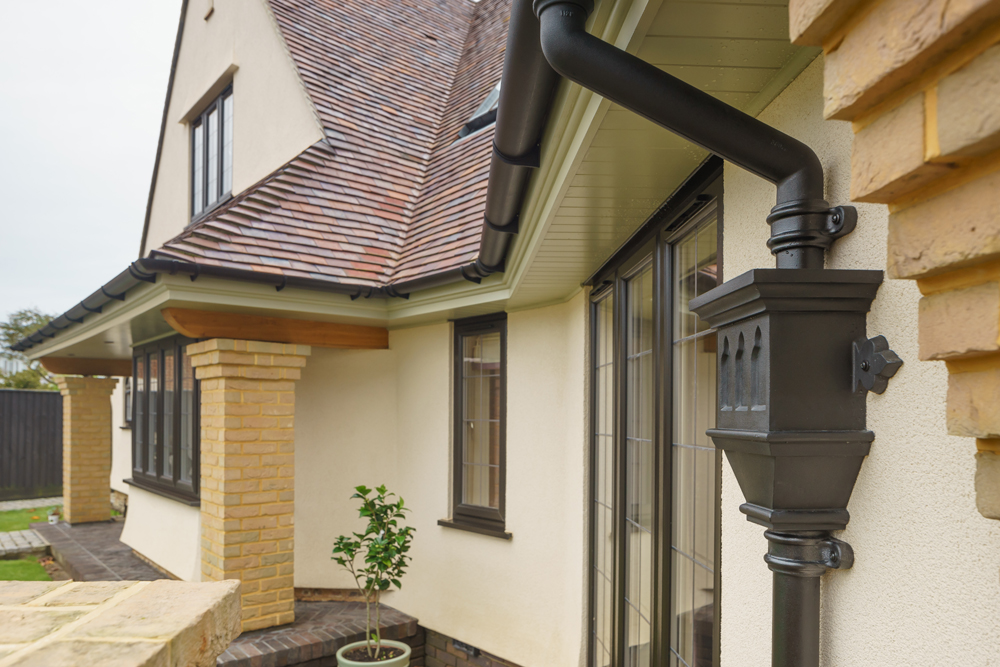
Paul Wadsworth, specification manager at Brett Martin discusses the benefits of cascade rainwater solutions, and gives an uncomplicated, step-by-step guide for self-builders to install these efficient alternatives to traditional cast-iron designs.
For over 150 years, cast-iron rainwater systems have been a core component of a building’s fabric. However, as building design and efficiency has radically transformed over time – rendering cast-iron expensive and time-consuming to work with – contractors and their clients are seeking alternatives.
At a fraction of the price to buy, install and maintain, modern plastic materials are an alternative to aluminium or cast iron rainwater specification to deliver projects under budget and ahead of schedule. It’s why the cascade rainwater and soil system from Brett Martin Plumbing and Drainage fits the bill perfectly.
Ease of installation
With significant additional weight, cast iron drainage systems can be heavy and difficult to install. Contractors must also be extra vigilant regarding health and safety and will require more time to lift and fix the system – leading to increased costs and potential delays in the installation process.
Almost every job will require both gutter and pipe lengths to be cut onsite using specialist tools. To ensure long-lasting durability, they need to be fully finished on site using a primer, undercoat and topcoat, to ward off corrosion. Even if the system used is delivered pre-painted, any cut lengths, or site damage to the finished surface, must be protected to the same level by the installer. It should be noted that, in some cases, if the level of protection applied on site is deemed insufficient, any guarantee offered may be, quite rightly, invalidated, leaving the installer liable.
Because the plastic ranges are so much lighter than cast iron, installation at height is less hazardous, being effortless to lift, easy to manoeuvre, simple to cut and quick to fit. The systems also benefit from external fixing lugs, enabling easy power tool access, which further speeds up installation. All gutter fitting joints have integral seals and flexible retaining clips, allowing the gutter lengths to simply click into place. No extra-cost fixing kits or nuts and bolts are required to make gutter joints, as with most traditional systems.
Benefits
There are an expansive choice of options and gutter profiles available for domestic new builds to suit most requirements. From the domestic style of gutter to high capacity systems for larger scale commercial projects, plastic rainwater systems have been carefully designed to emulate original features, dimensions and detailing.
Once installed, the system is low maintenance as, unlike cast iron, it is not vulnerable to rusting or corrosion and does not require regular sanding, priming or repainting to protect it from the elements.
Step 1 – Planning and preparation
Plan carefully. Ensure you have the right tools for the job and relevant personal protection.
Step 2 – Fitting running outlets
Fix running outlets above the drains or gullies where the water will drain into using 25mm x 5mm corrosion resistant screws.
Step 3 – Calculating fall
Guttering should be installed with a downward fall towards the rainwater outlet – 1mm for every 600mm. The running outlet should be at the lowest point on the gutter run.
Step 4 – Fitting fascia brackets
Fix the first fascia bracket furthest from the outlet at a position on the fascia to allow for the required fall. No more than 100mm from the end of the fascia board. Stretch a line taut between the fixed outlet and fascia bracket to establish a straight gutter line. Fascia brackets should be fitted to the fascia board at equal intervals. A union bracket should be used where two gutter lengths are joined. Gutter supports should be spaced of no more than 900mm or less than 600mm in areas of heavy snow.
Step 5 – Cutting gutter to size
Cut to length using a saw and a file to remove any burrs from sawn ends, making allowances in length to fit the expansion lines marked in the fittings.
Step 6 – Fitting the gutter
Lubricate the seals using silicone spray. Each length of gutter should be placed into position with the back edge under each fitting. Rotate down and then click front edge into place over the top edge of the gutter.
Step 7 – Fitting downpipe
If required, fit an offset between the running outlet and the downpipe. Fit the downpipe to the offset. Ensure each connection is retracted at least 5mm from the receiving socket before fixing to the wall. Use spirit level to check vertical alignment. Mark the walls using the holes in the lugs of the socketed downpipes as guides. Then drill, plug and fix the downpipe using fixings. Water test system to ensure no adjustments to the fall is necessary and all connections to the fall are fitted correctly.
http://www.brettmartin.com/en-gb/plumbing-and-drainage/products/cast-iron.aspx
https://www.youtube.com/watch?time_continue=1&v=S2voSGHkU2U