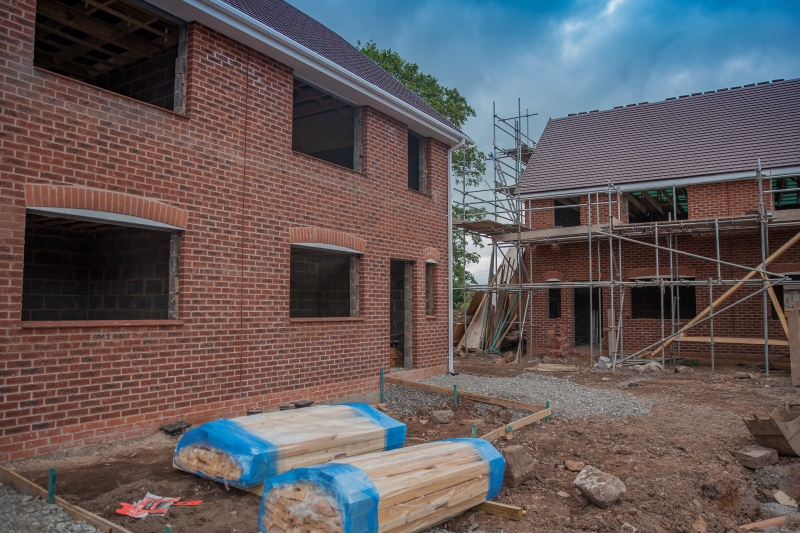
James Hulbert, Head of Housing and Offsite at Knauf Insulation explains the role of insulation in getting new homes heat pump ready.
Changes to Approved Document L (Part L) of the Building Regulations (June 2022), brought in much stricter energy efficiency standards. New homes must now produce 31% less carbon emissions than the 2013 standards. This can be achieved through a combination of fabric efficiency and sustainable technologies such as heat pumps.
The changes don’t stop there. Part L is a stepping stone to the Future Homes Standard, set to come into force in 2025, which will bring in a 75% carbon reduction [over 2013]. Buyer demand is changing too. A recent Knight Frank survey found 86% of home buyers placed energy efficiency as ‘important’ or ‘very important’ when looking for a new home.
While the government may have delayed the ban on installing gas boilers into new homes, it makes little sense for independent builders to do so. Getting your new builds heat pump ready is the best way to both appeal to homeowners now, save infrastructure costs if there’s no gas on site and future proof your builds.
Size matters
With heat pumps, one size does not fit all. Install one that’s too small and homeowners won’t be able to heat their homes to the desired temperature (or maintain a comfortable environment). Install one that’s too large, and they’ll be wasting energy. So, if you are unsure which model is best for the home you’re building, check with the manufacturer.
Remember there’s more than just the heat pump to be considered. Without effective insulation, you’re increasing the size of the space that needs heating.
Real performance
A major factor in effective insulation is your choice of material. Insulation materials are given lambda values that indicate how well they prevent heat transfer. In theory, the lower the lambda, the better the insulation performs. However, whatever the lambda value, unintended air gaps allow heat to escape (compromising the insulation’s performance, whether thermal, fire safety or acoustic).
Some materials are more prone to gaps than others despite the skill of the installer. Take rigid boards for example. They’re inflexible, so won’t adapt to imperfections in the substrate, need precision cutting on site to ensure good joint alignment, and must be taped. Even when they’re installed correctly, any movement in construction can undo the bricklayer’s good work.
In contrast, mineral wool insulation is easy to fit correctly. It adapts to imperfections, friction fits to the building elements, adapts to movement and knits together at joints – all of which helps to eliminate gaps.
Focus on fabric
Once you’ve chosen the material, consider the quantity of insulation you install – it may be more than you think. To ensure that new build homes have the right levels of insulation to accommodate heat pumps (and changing regulations), follow the lead of volume housebuilders. They now regularly install loft insulation to a depth of 400mm to 500mm to ensure maximum performance for a nominal increase in build cost.
Another area where we’re seeing change is cavity widths. With the Future Homes Standard on the horizon, 150mm cavity widths are likely to become the norm, so many housebuilders have already made the leap for Part L 22 – and with good reason.
Adapting specifications now, future proofs designs and ensures there’s plenty of time to get everything right. It means small housebuilders won’t have to adapt midway through the build or undertake retrofit work later.
More importantly, increasing cavity widths by 50mm has a minimal impact on floor space or plot sizes, but provides optimal fabric performance. It also gives you more flexibility to choose the best insulation for the job. For example, 150mm of DriTherm Cavity Slab 32 not only provides reliable thermal and acoustic performance, it also offers greater peace of mind because it’s non-combustible. Plus, with changes to NHBC Standards in 2023, it offers the design flexibility to be used with fairfaced masonry in areas deemed ‘Very Severe’ in exposure. Remember too, that, with the correct block, a 150mm cavity also delivers the 0.18 W/m2K U-value asked for in Wales (Part L 22).
So, for maximum design and compliance flexibility, it is worth speaking to your architect or designer about expanding your cavity to 150mm. Ultimately, with energy prices predicted to remain high into the late-2030s, home energy efficiency will continue to be an important factor for home buyers. So, ensuring your new build homes are well insulated and heat pump ready will give you the competitive edge in a crowded marketplace.
For further information on Knauf Insulation visit Knauf Insulation UK – Loft, Roof and Wall Insulation Products.