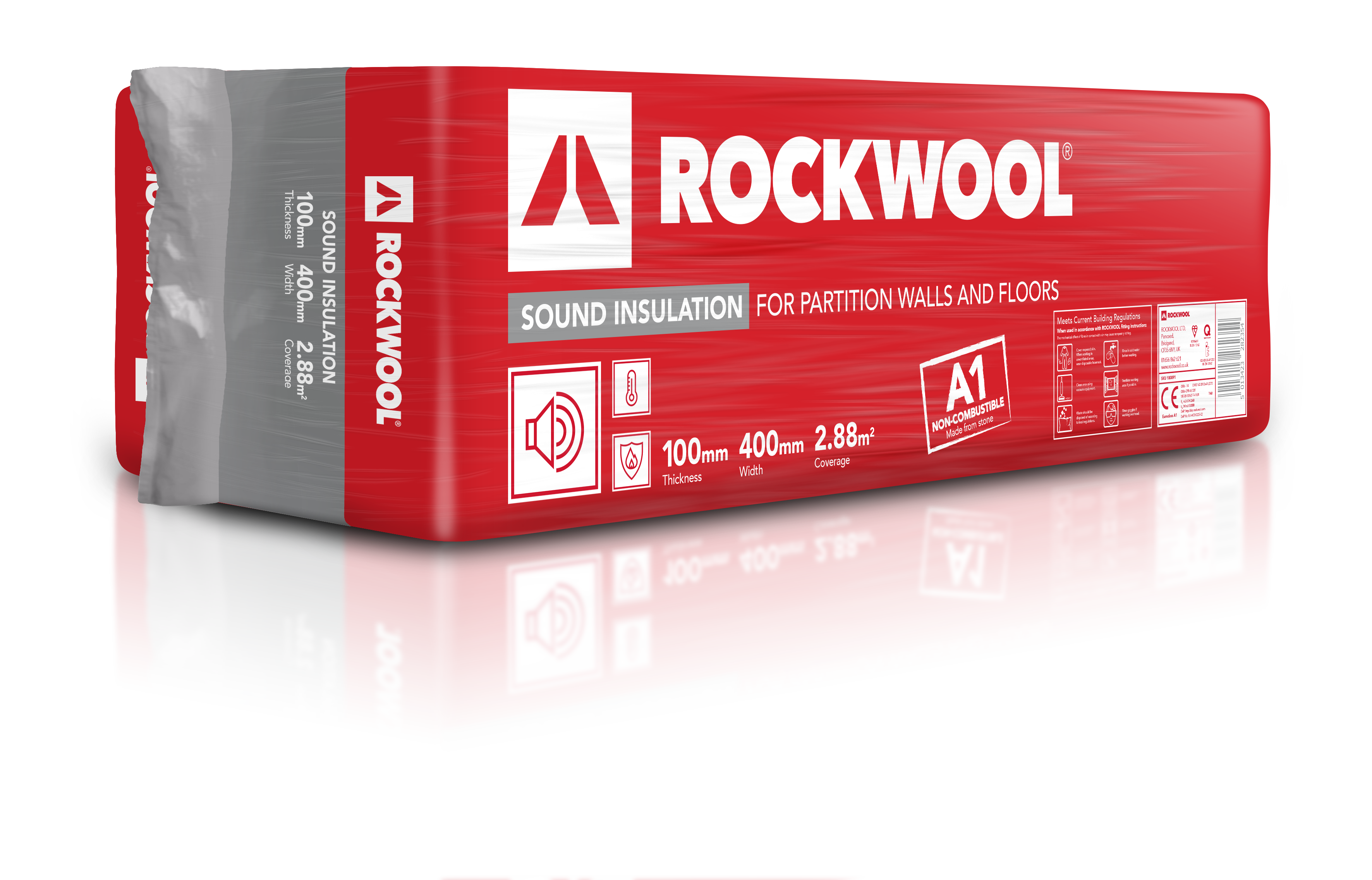
James Mills, product manager at stone wool insulation specialist, Rockwool, offers you some best practice insulation tips for loft conversions.
Loft conversions remain one of the most popular ways to renovate, add space and increase property values for UK homeowners. In a flat housing market, renovation is very attractive to homeowners. There’s strong evidence to suggest that more and more people are staying put and improving or extending their home, rather than paying the hefty cost of moving. Adding an extra room in the roof can create up to 50 per cent more living space, and add approximately 20 per cent to the value, without losing any garden space like an extension. Recent changes to planning permission also now mean that work on the loft falls under “permitted development rule”, so homeowners can make changes to their loft space without permission, subject to a few limitations. In order to fully take advantage of this opportunity, and achieve a high-quality loft conversion, it is important to pay close attention to insulation.
One of the common challenges you’ll face when tackling a loft conversion is the lightweight mass of the overall structure. This makes the loft space vulnerable to external noise, whether that’s from road, rail or air traffic, general urban street noise or the wet and windy British weather. Since the vast majority of loft spaces are converted into extra bedrooms, you’ll want to do something about noise, or you’re taking a big chance in risking an unhappy customer.
The good news is that there is plenty you can do with the right choice of insulation and you don’t have to lose any valuable headroom space either. This is because when carrying out a loft conversion you will likely need to re-roof as well. This involves removing the tiles as well as changing the roof shape. At this point, we would recommend putting a layer of Rockwool Hardrock Multi-fix insulation board over the top of the roof, with tiles added above, this additional layer will provide significant acoustic benefits and ensure the optimum thermal performance is achieved. Internally, an effective solution to use is Sound Slab, fully filling the rafter depth. Because this is stone wool insulation, the fibres are matted in such a way that they trap sound waves and deaden vibration very efficiently.
Warm-roof approach
With this dual layer, warm roof approach, you’ll create a super-efficient acoustic insulation barrier both outside and inside the loft conversion that stops any external noise in its tracks. The high-density layer on the roof reduces vibration-based sound whilst thicker insulation between the rafters addresses airborne sound.
You’ll also be efficient in meeting the U-Value requirement of Building Regs. Rockwool Sound Slab gives you a tight, friction fit between joists and around cables, pipes, sockets and services thanks to its patented ‘FLEXI’ edge. Add the continuous layer of insulation board on the outside of the conversion and you’re also minimising the problem of thermal bridging.
It’s not just about keeping the heat in. Because Rockwool has a high thermal mass, it helps effective regulation of temperature on hot summer days, keeping the loft space comfortable and giving your customer better, all year-round temperature control.
Insulating the floors and walls is also important, especially if you’re fitting wooden floors. You don’t want the people below or in the adjoining properties getting annoyed by footsteps or noises coming from your loft, nor do you want to hear music or voices from other rooms in the house or next door. Again, who wants to risk an unhappy customer?
We’d recommend you fit Sound Slab in between the floor joists, and a layer of Thermal Rockfloor, high density insulation over the top of that to cut out any risk of unwanted noise transfer in the floor. We’d also suggest battening out from any solid walls to fit Sound Slab. This will reduce sound travelling between walls of adjoining properties and again minimise external noise coming into the loft conversion through an outside wall.
Another thing to think about is safety. You’re adding a third storey to your customer’s house with a timber-framed loft conversion. You want to make sure that you’re creating a space that’s quiet and comfortable but also safe. Stone wool insulation is A1 non-combustible. It won’t burn or contribute to a fire. Importantly, it does not significantly contribute to the emission of toxic smoke either, which makes it the safe material to choose for insulating loft conversions.
Whichever way you look at it, taking this dual insulation approach to a loft conversion makes a lot of sense. If you want the quiet life – and want that for your customer too – then stone wool insulation inside and outside is the way to go.