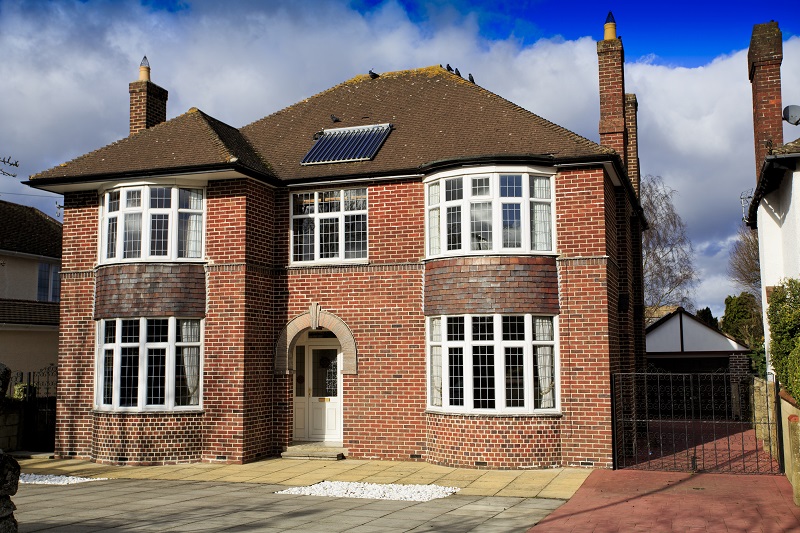
In the third of our series, Hudson Lambert of Safeguard looks at houses built in the period after WWII and up to the start of the 1960s. Although construction detail had improved on houses built pre-war, there are still areas which cause concern in respect of damp today.
As in the aftermath of the First World War, the period following the second outing saw a huge surge in house-building. This was less to do with a perceived need for ‘homes fit for heroes’ for returning combatants; and more the urgent need to replace housing in towns and cities nationwide wrecked by enemy action.
For example, around 1,000,000 homes in London were damaged or destroyed by bombing; and Liverpool, Coventry, Belfast, Plymouth, Manchester, Hull, Cardiff and Newcastle, to mention just a few, all have their own sorry tales to tell. Total loss is estimated at over 2,000,000 homes.
Again, as in the years after WW1, there was a shift in construction details in housebuilding. This wasn’t as radical as the step-change from Victorian and Edwardian techniques, but was marked nonetheless – especially in the approach to floors.
Cavity walls
Issues with walls tend to be as outlined in the previous part of this series regarding cavity structures. Cavity walls were primarily introduced to obviate penetrating damp.
Whether this improved thermal performance of housing is moot, and in the1970s it became fashionable to infill with cavity wall insulation (CWI) to tackle this concern. It is estimated that 6,000,000 properties of this period have received this treatment.
However, issues like bridging and infilling – resulting from poor construction practice (e.g. excess mortar falling onto wall ties; slumped cavity wall insulation) or where the wall was defective in the first instance (cracking, mortar losses) – mean problems can arise. These problems manifest as internal damp and colder properties.
In situations where cavity wall insulation has failed completely – generally a function of the installation, not the products themselves – and has collapsed into the foot of the wall, the only answer is removal: a truly irksome job, especially if done properly.
If the CWI is still salvageable though, then a masonry protection cream – such as Stormdry – would provide a solution.
Applied to the exterior brickwork, the breathable cream allows the CWI and wall to dry out, albeit slowly, while preventing any more moisture absorption. Stormdry, for instance, is BBA certified for 25 years – plenty of time to help retrieve the situation!
Before cream application though, it should be noted that any masonry cracking and re-pointing should be tackled first.
Masonry cracking
Masonry cracking – beyond subsidence – in this period is relatively common and is often a function of window replacement, due to over-sized unsupported apertures, missing lintels and inferior materials.
In this context, once the window and/ or opening has been reinforced, a crack-stitching system – such as BrickFix – can be used to ‘reconnect’ masonry and reinforce existing mortar beds.
Floor construction
As mentioned above, we see at this time a change in floor construction away from suspended timber floors and toward concrete slabs. Concrete strip footings – as first seen pre-war – remain in use, but ground behind them is dug out and infilled with hardcore.
And it is onto this hardcore layer that concrete floor slabs are poured. These slabs are then sealed with asphalt and the final floor layer – often herringbone parquet – laid.
As with bitumen DPCs, it is these asphalt layers that give the floor its damp resistance – and are also subject to degradation.
Installing a new DPC – using treatments such as Safeguard’s Dryrod – into the wall has been covered before, and the failure of the asphaltic floor layer can also be tackled. In such cases, the parquet would need removing and the existing, failed layer cleaning back.
Then a new damp proof membrane (DPM) – such as Safeguard’s Drybase Liquid Applied DPM – can be brush-applied. The DPM is a liquid, polymer-based barrier coating that can be used to resist penetration of water, gases – such as methane and Radon – salts and other liquids through masonry, stone and concrete.
As usual, even without remedials being necessary, it is important that damp problems are not caused by new works.
Therefore, care should be taken to avoid compromising ventilation in walls and floors by not blocking airbricks etc; ensuring window openings are structurally sound and reinforce where necessary, and, most importantly, see that DPCs are not bridged by raising external levels over them.
Next week, and in the last of our housing type series, we get into the swinging 60s and have a look at the problems you may encounter with these more modern properties.
For more information on Safeguard Europe click here.