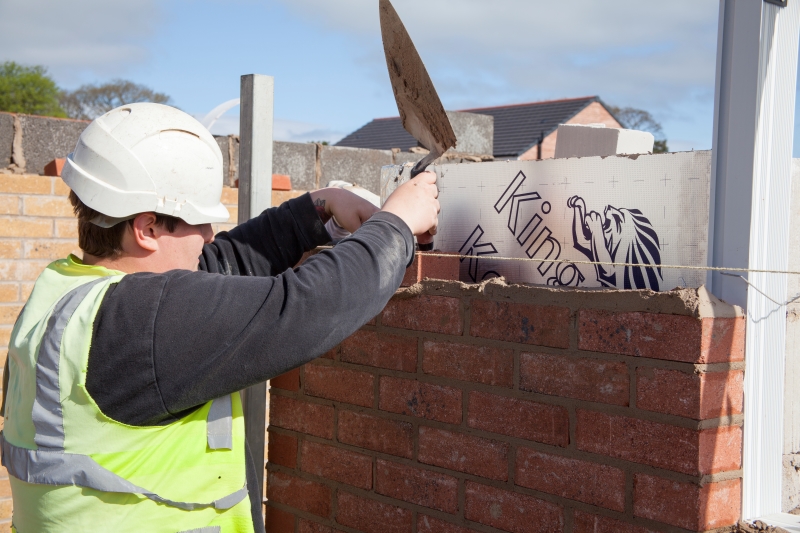
Matthew Evans, Director of Technical and Regulatory Affairs – GB at Kingspan Insulation, discusses the insulation targets you need to hit when extending a home.
Making sure all elements on your project achieve the right U-value is a standard part of all building work. However, when it comes to adding extensions, there can be some confusion on what targets you need to meet for the walls, floor and roof of the new space, and whether this work triggers any other changes for the insulation levels in the rest of the house.
U-value Targets
As you’ll probably know, the regulatory requirements are different in England, Scotland and Wales. This may affect the U-values you need to meet on extensions.
In all three countries, the Building Regulations and Standards provide a standard approach for extensions. This basically sets worst case U-values for the walls, floor and roof of the extension which you need to meet or improve on. These U-values are area–weighted, which means it is possible to insulate certain areas to a worse standard providing you compensate for this elsewhere in the construction. In all cases, no point in the construction should achieve a worse U-value than 0.35 W/m2K for the roof or 0.70 W/m2K for the walls and floor.
The worst-case U-values are shown in the table below. In Scotland, there is a single set for all extensions. In England and Wales, alongside the standard worst-case U-values for new elements, there is also a separate set of values which apply to any parts of the structure which are retained from the existing building (renovated elements). For example, if the extension is built against or incorporates a garage which was previously unheated these U-values would apply to the garage space.
England (W/m2K) | Wales (W/m2K) | Scotland (W/m2K) | |||
New element | Renovated element | New element | Renovated element | ||
Roof | 0.15 | 0.16 | 0.13 | 0.16 | 0.12 |
Walls – Cavity Insulation | 0.18 | 0.55 | 0.18 | 0.55 | 0.17 |
Walls – Internal or External Insulation | 0.18 | 0.30 | 0.18 | 0.30 | 0.17 |
Floors | 0.18 | 0.25 | 0.15 | 0.25 | 0.15 |
Table 1 – worst-case U-values (area–weighted) for domestic extensions
In Wales, adding an extension may also trigger some consequential improvements to the rest of the home. Depending on the size of the extension, these may include adding loft insulation (if existing is less than 200 mm) and adding cavity wall insulation to any currently uninsulated cavity walls where appropriate. England also has consequential improvements, but they only apply for buildings which will have a total useable floor space of over 1000 m² (including the proposed extension).
If you need more flexibility on U-values, all three countries also provide two alternative approaches. These require you to either calculate a single U-value for the total area of the construction and to prove this is no higher than for an extension of the same size built using the standard approach, or to carry out energy modelling on the extension and home, looking at expected carbon emissions and energy demand. In most cases, it’s simplest and cheapest to stick with the standard approach using the U-values above.
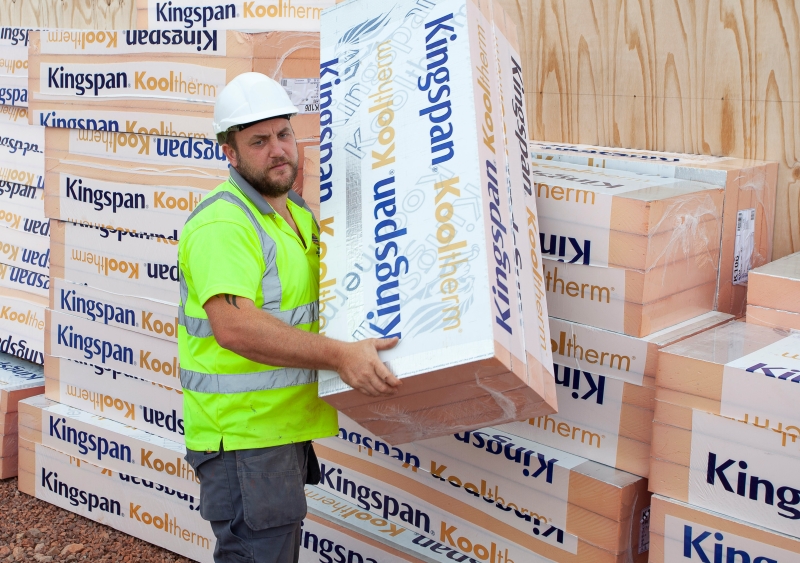
Choosing Insulation
Once you’re clear on the U-value you need to meet, it’s worth having a think about which products you’re fitting, and in particular their thermal conductivity (lambda value). The lower this is, the more effective the insulation is at preventing heat transfer. This can mean a slimmer thickness of insulation can be installed. Several manufacturers now provide online U-value calculators which allow you to enter details about the construction you’re building, including the target U-value. They will provide suggested products and thicknesses for the job.
Phenolic insulation boards tend to have the lowest thermal conductivity of commonly used insulation materials (typically as low as 0.019 W/mK). This makes them a good choice for a range of applications including floors, pitched roofs and external walls.
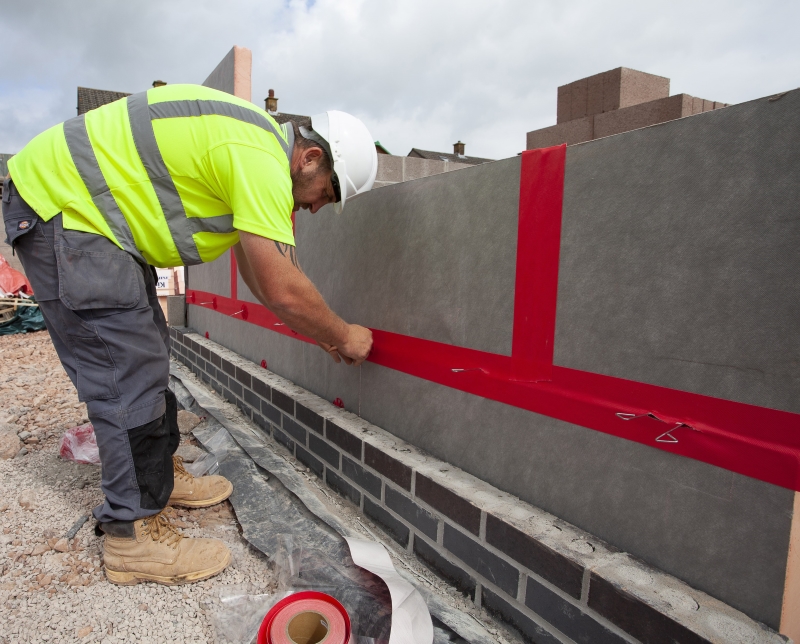
Phenolic boards can be particularly useful for new cavity walls, where they can help achieve the required U-values with a slimmer construction than would be possible with worse performing materials. Standard partial-fill phenolic cavity boards are typically fitted with a 50 mm residual cavity between the insulation and the outer leaf. It may also be possible to use full-fill phenolic cavity boards which require a residual cavity of just 10 mm. The most suitable option for a project will depend on how likely the property is to be exposed to wind-driven rain. Depending on the risk, the warranty provider may prohibit the use of full fill insulation, require different construction approaches to be adopted and/or require the residual cavity width to be increased.
In all cases, it is important to ensure that the insulation boards are cut and fitted so there are no gaps within the layer. Particular attention needs to be paid at the junctions between the wall, roof and floors and around openings. Some manufacturers can provide detailing guides with practical process sequences and diagrams, illustrating best practice when fitting products in these areas.
Ticking the boxes
The standard approach to compliance provides a clear set of U-values for installers working on extension projects to look to achieve or better. By making use of manufacturer U-value calculators and using insulation materials which achieve low thermal conductivities, it should be relatively straightforward to hit these values on all home extension projects without needing bulky constructions.
For further information and technical support from Kingspan visit https://www.kingspan.com/gb