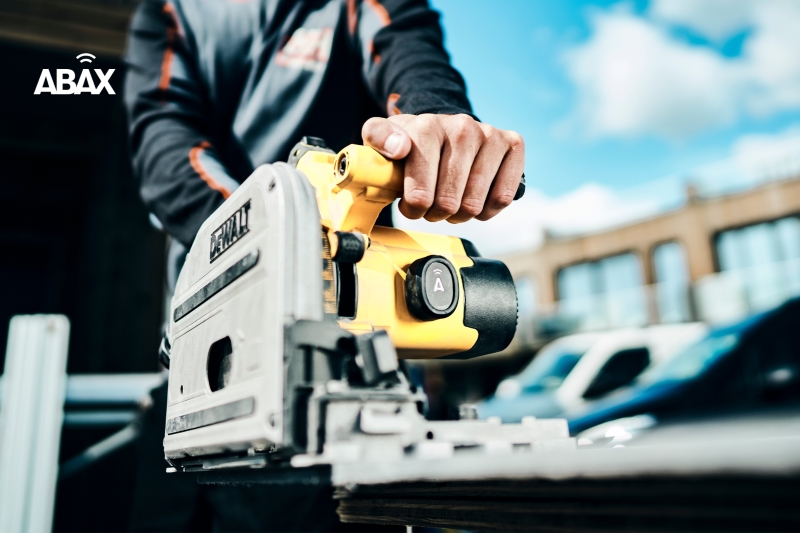
Craig Allan, Director of Specialised Sales, ABAX explains how you can start saving costs on site with cutting-edge telematics technology.
In the construction industry, staying ahead of the curve requires innovative solutions that enhance efficiency and reduce costs.
By leveraging cutting-edge telematics technology, construction companies can gain valuable insights into their operations, enabling them to make informed decisions that drive growth.
Below are some examples of how telematics software is transforming construction management, and how these advancements contribute to cost savings and increased efficiency, resulting in a stronger competitive position in the market.
Predictive Maintenance
By monitoring equipment health and performance in real-time, telematics data can schedule maintenance before breakdowns occur, and for the most convenient time for your business, reducing costly downtime and increasing business efficiency.
Regularly maintained equipment runs more efficiently – and keeps to manufacturer’s warranty requirements – minimising delays, and improving overall project timelines. By monitoring the usage and wear of equipment, companies can better manage the lifecycle of their machinery, recycling or replacing it at the most appropriate time to minimise any disruption and impact to the business – and have the least impact on the environment.
Ensuring machinery is always in optimal condition increases productivity and reliability, provides the ability to meet contractual deadlines and ensures customer satisfaction. Properly maintained equipment also tends to use less fuel and produce fewer emissions, which is a benefit to the environment and also a major requirement when answering RFQs and Tenders.
Equipment Usage
By monitoring when and how equipment is used, companies can identify under-utilised assets and reallocate or downsize their fleet to reduce rental or ownership costs.
Another advantage of effective utilisation of assets helps is delivering construction projects on time and within budget, therefore enhancing your businesses’ reputation and providing superior levels of customer satisfaction. Better use of assets means any saved money can be re-invested into other, more useful areas of the business to help maintain a competitive edge.
Better Tool Management
Effective tool tracking provides real-time visibility, reducing the risk of lost and misplaced tools and the associated replacement costs. Notifications can be deployed if a tool leaves a designated area, or is left behind on a job, allowing immediate action and minimising financial losses, both from wasted journey and from potential fines for late completion of jobs.
This solution can save valuable hours previously spent searching for misplaced tools. With the right telematics solution, you can allocate tool inventories to specific vehicles and get alerts if items are left behind. No more wasted time looking for lost or misplaced tools!
Keeping track of all assets in real-time, ensures better project management and utilisation of time and resources. This visibility significantly reduces the time and money spent on managing tools, so efforts can be focussed instead on completing jobs on time, to a high standard.
Remote Job Site Control
The ability to get an overview of assets on a site could reduce the need for on-site supervision, as employees can oversee multiple job sites from a central location – or their smartphone – cutting down on travel expenses and labour costs associated with frequent site visits. A clear view of equipment and tool usage across sites means construction companies can allocate resources more efficiently, avoiding unnecessary rentals or purchases.
With instant access to data on tool and equipment statuses, quick, informed decisions can be made, minimising delays and keeping projects on track. It also allows for better coordination and communication between job sites and teams, reducing the likelihood of misunderstandings and wasted time in identifying where specific items are and who has them.
All of this will provide greater control over all job sites, in real-time, allowing better project management. You will be able to keep your customers better informed and ensure that jobs run on budget and are delivered on time.
Compliance Monitoring and Safety Management
Telematics solutions can provide detailed reports on driver behaviour, which enables companies to proactively address any issues and mitigate reputation risk (if you operate branded vehicles) whilst preventing unnecessary expense due to increased wear and tear leading to an increase in SMR costs.
With real-time data on equipment usage and worker activities companies can make adjustments to prevent accidents and improve overall site safety. Data can identify areas where workers need additional training or where safety protocols are not being followed, ensuring that employees are operating efficiently and safely.
Telematics software has the potential to transform construction operations. From predictive maintenance to better tool management and remote job site control, these advanced solutions provide real-time insights and decision-making is data-driven. A small, simple, change to your business can have a major positive impact.
As the industry continues to evolve, adopting innovative tools like telematics will be essential for maintaining a competitive edge and ensuring long-term success.
For more information on ABAX visit Trusted experts in fleet management services | ABAX.