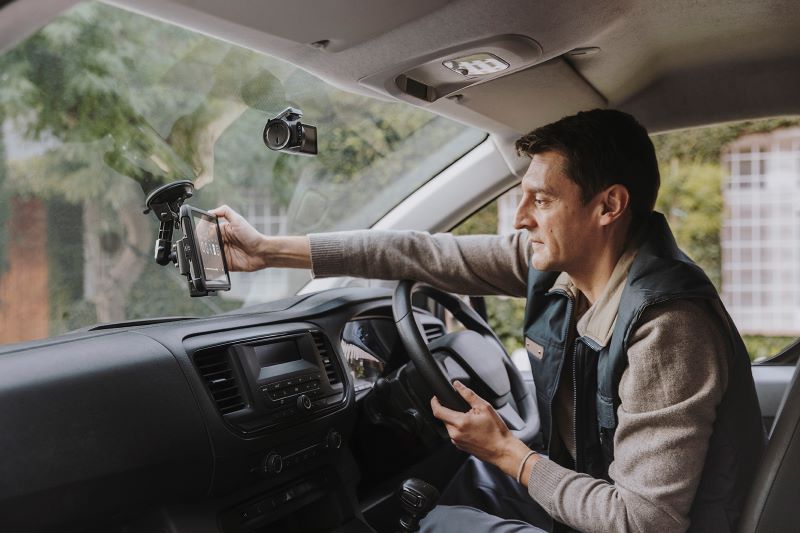
Beverley Wise, Webfleet Regional Director for Bridgestone Mobility Solutions explains how you can form your own digital shield against industry woes
A volatile economic environment weighs heavily on the construction sector. Building firms are feeling the squeeze amidst high inflation and material costs, soaring interest rates, skilled labour shortages and fragile consumer confidence.
Successfully navigating these challenges while maintaining business productivity, growth and service delivery is no easy task. The construction industry has been notoriously slow to embrace the workflow and cost efficiency gains offered by connected tech solutions, but now, more than ever before, smarter ways of working are called for.
A workflow management boost
Managing a commercial vehicle fleet and mobile workforce can be a challenging affair – for building firms large and small – without proper visibility over their activities. Indeed, access to business insights can hold the key to increased flexibility, keeping a lid on costs and a tight rein on project schedules.
Telematics solutions – and notably those that offer opportunities for seamless integration with wider tech applications – offer the route to real-time tracking of assets, streamlined processes, greater levels of automation, reduced administration and less reliance on paper trials.
The Webfleet management platform, for example, will show precisely when, where and how a construction fleet is being utilised and how much time is being spent behind the wheel. It will instantly alert you if and when a construction vehicle or asset leaves a pre-defined area and in a boost to security, if an asset or vehicle is taken from site without permission, it can be located.
Daily workflow can be sent to driver terminals, with workers automatically routed directly to their site destinations. At the same time, automatic alerts advising customers of their arrival times can be sent via text or email. Proof of delivery of equipment or materials can be submitted via signature capture functionality on the connected driver device, an in-built camera or NFC chip.
Accurate ETA information, based on traffic and historic journey time data, can also be combined with planning software – a significant benefit for the time-sensitive transportation of materials. In-vehicle sensors, meanwhile, mean managers can be informed when materials, such as concrete, are being offloaded.
The value of end-to-end connected data has been highlighted by industry operators such Wright Mix, a concrete supplier that saw a productivity uplift of more than 25 per cent after switching to a paperless system for ordering and job scheduling, underpinned by Webfleet.
Cost control in the spotlight
As fuel prices hit record highs last year, even the most financially robust of construction-sector firms found themselves hit hard at the pumps. Recent falls have given fleets cause for cheer over recent weeks, but the outlook remains uncertain.
The Office for Budget Responsibility (OBR) has warned of a 23 per cent hike in fuel duty from March, which would see petrol and diesel prices rise by around 12p a litre.
With prudent management however, it is possible to minimise the fuel cost burden by. And a reduction in fuel bills represents direct bottom-line savings – savings that may otherwise have to be recovered through an increase in prices, or through budget cuts elsewhere.
Solutions such as Webfleet offer one of the most logical options for relieving cost pressures at the pump. Better navigation alone can lead to a significant reduction in fuel consumption and thousands of pounds a year can be saved by eliminating private or unauthorised mileage, through enhanced routing and the better allocation of vehicles to jobs.
Even greater financial rewards can be enjoyed by improving the performance and mpg of drivers. Webfleet’s OptiDrive 360, for example, enables firms to improve driving styles – from unnecessary acceleration and deceleration to speeding and harsh braking – and target training where it is most needed. Engine idling is a particularly costly problem for the construction sector.
Unnecessary idling can prove particularly costly for building firms and will often occur on-site when vehicles are left waiting for extended periods – when machinery is not being powered, for example, during the loading and unloading of materials, and during operator breaks.
Elsewhere, maintenance and repair costs can be better controlled with the automatic scheduling and management of maintenance tasks. Notifications can be set up based on odometer information, operating time or time since the last maintenance, and you can be alerted should mechanical issues arise. Furthermore, connected driver terminals can be used to conduct vehicle checks at the start of each day or week – the results being automatically updated in the back office.
Building an insights-driven future
Building firms may still be playing catch up when it comes to digitisation, but as cost pressures bite, now may be the time to deploy the tools that not only help deliver competitive advantage, but that also serve as a safety net to their commercial futures.
For more information on Webfleet visit The nr. 1 Fleet Management & Telematics Solution — Webfleet GB.