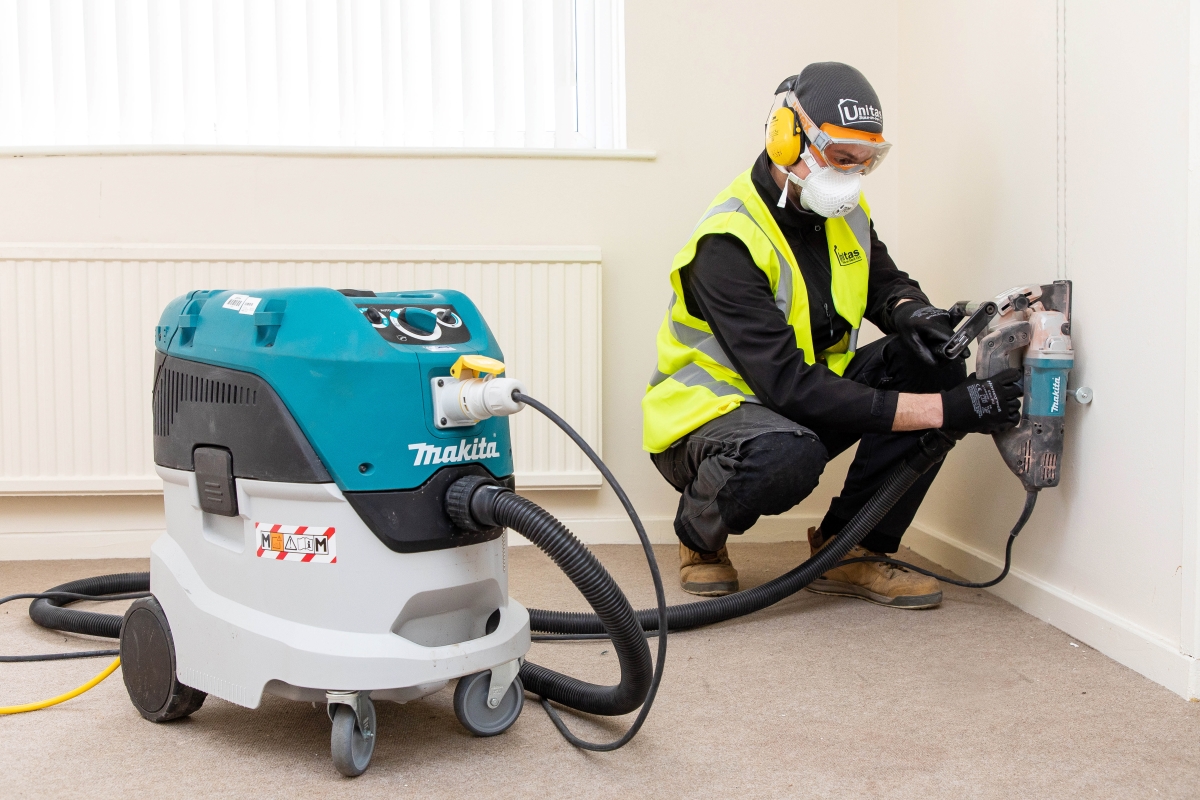
The risks of dust and vibration on site should not be underestimated. Here, Kevin Brannigan, Marketing Manager at Makita explains the issues and how choosing the right tools and equipment can make all the difference.
If not managed correctly, the dust and vibration generated through common tasks such as drilling, cutting, sanding and breaking materials can have serious implications for professionals’ long-term health.
Recognising the dangers
All power tools produce some level of vibration, but this is typically higher for tools such as hammer drills and breakers due to the nature of the machine’s action. Frequent or prolonged exposure to high levels of vibration can cause health issues including Hand Arm Vibration Syndrome (HAVS), which includes conditions such as Vibration White Finger and Carpal Tunnel Syndrome. This commonly results in painful, tingling or numb fingers and hands because of damage to the nerves and blood vessels. It can also result in weakened muscles and reduced dexterity.
With regards to construction dust, it is important to understand that it is the very fine dust particles, often invisible to the eye, that poses the biggest hazard. This is referred to as respirable dust and can penetrate deep into the lungs. Respirable Crystalline Silica (RCS) particles, which is generated from drilling, cutting or breaking stone, brick, concrete and tiles, can be 100 times smaller than the average grain of sand. Prolonged exposure to even small quantities of RCS dust can cause silicosis, Chronic Obstructive Pulmonary Disease (COPD) and has been linked to cancer. Also, it is estimated that around 500 construction professionals die every year due to past exposure to silica dust.
Addressing the issues
The good news is that there are steps that can be taken to prevent the issues associated with both vibration and dust. One of the most effective ways is to invest in tools that include features and technologies designed to mitigate the risks.
For types of tools with typically higher levels of vibration, it is important to look for options that have been engineered to prevent vibration being transferred to the user and therefore extend the time that the tool can be safely and comfortably operated. These measures will differ depending on the action of the tool but can include counterweight mechanisms to offset the force of the machine and vibration absorbing housings and handles.
As an example, Makita’s Anti-Vibration Technology (AVT) means that its latest 80VMax cordless breaker achieves a vibration level of just 6.5 m/s², compared with 9.7 m/s² for the previous generation of equivalent corded breaker. This means the Exposure Action Value (EAV), the level at which action must be taken, is reached after 1 hour and 10 minutes of trigger time rather than 31 minutes. In effect, doubling the level of productivity that is possible.
In terms of dust management, it is important to always use a dust extractor when working with materials that produce respirable dust, even for quick jobs. It is also essential to have an extractor that is of the correct class for the type of dust. The Health and Safety Executive (HSE) states that a M-Class dust extractor is the minimum legal requirement for this type of dust.
To streamline dust management, it is worth looking for an extractor that connects easily to the tools to enable automatic operation when the tool is in use. This is common where corded tools can be connected to the extractor via a power take-off. However, there are now options for cordless tools.
Technologies such as Makita’s Auto-Start Wireless System (AWS) connects compatible tools and extractors together using Bluetooth to run the extractor automatically when the tool is in use. There are also now cordless M-Class extractors available to make work on site as simple as possible by eliminating the need to connect to mains power.
Occupational exposure to dust and vibration can have serious impacts on long-term health. Choosing tools with features and technologies that help minimise the risks is an important consideration when expanding or upgrading your kit.
To find out more about how Makita products can help ensure safe working on site, visit www.makitauk.com.