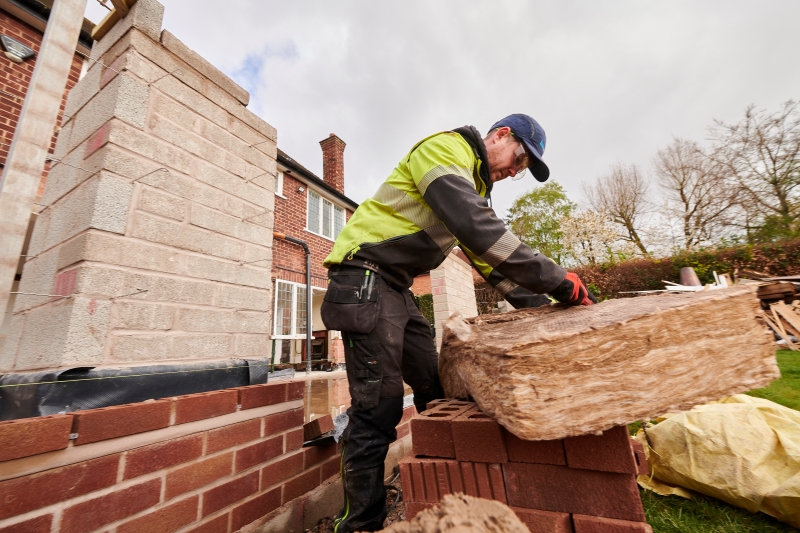
One of the most significant shifts in housebuilding is the increasing adoption of 150mm cavity width in masonry construction.
In a recent survey of housebuilders, conducted by this publication and Knauf Insulation, 41% of participants said they are already building with 150mm cavities, and just over a quarter are considering it. This might seem unnecessary, but the construction industry is changing rapidly due to increasingly tight regulations and a move towards more sustainable building practices.
This is fast becoming the new normal, which is why in this article we will explore how we got here and the benefits of building with 150mm cavities.
Closing the performance gap
‘Real performance’ isn’t just an aspiration anymore. It’s an important plank of the Future Homes Standard which, although still under consultation, has a clear direction of travel. Closing the gap between designed and actual performance means being realistic about the unforced errors that can happen under real site conditions.
For example, rigid board insulation is often chosen due to its theoretically lower lambda values and installed in traditional 100mm cavities, with the expectation that it will achieve a low U-value. In reality rigid boards are challenging to install correctly. They first need to be cut to exact sizes and taped with precision to ensure a continuous insulation layer, but the real challenge comes from making them sit flush against the substrate, which is close to impossible if the surface has even minor imperfections.
One way to tackle this issue is to use insulation that’s easier to install correctly. Mineral wool insulation, for example, is flexible, allowing it to adapt to minor imperfections in the substrate and fully fill the cavity. The slabs also ‘knit’ together, further minimising gaps and maximising thermal performance. Using 150mm of mineral wool insulation allows housebuilders to meet energy efficiency requirements both on paper and in the real world.
Compliance today and tomorrow
Beyond thermal performance, current compliance and future regulations are pushing many builders towards 150mm cavities.
The impact of the 2017 Grenfell Tower tragedy on the industry and its regulations is hard to overstate. Many insurers, local authorities and customers now ask for non-combustible insulation as standard, regardless of the height or use of the building, going beyond even the updated guidance in Approved Document B (Fire safety).
Environmental regulations are also going through a period of change. While Approved Document L addresses operational carbon reduction, by requiring lower U-values and increased thermal performance, it is likely that embodied carbon will be factored into future regulations. Embodied carbon is the total greenhouse gas emissions released over a product’s lifecycle, including raw material extraction, manufacturing, transportation, and the construction process. Some industry groups are supporting a proposed ‘Part Z’ Building Regulation which would require embodied carbon to be assessed on all projects.
As standards continue to rise, building with narrow cavities will become a constraint. Switching to 150mm allows housebuilders to choose insulation that is non-combustible and has lower embodied carbon. Glass mineral wool for example, has the lowest levels of embodied carbon of any mainstream insulation material and Knauf Insulation’s glass mineral wool has the best possible Euroclass A1 reaction to fire classification.
Cost benefits
While the benefits to thermal performance, safety, and sustainability are clear, using 150mm cavities with mineral wool insulation also has economic benefits. Mineral wool is cost-efficient compared with many types of insulation, and its price doesn’t depend on the volatile petrochemical and oil markets, unlike materials such as PIR. As countries look to decarbonise, the supply of petrochemicals will likely be reduced, putting further pressure on the price and availability of many insulation products.
Mineral wool slabs or blown-in insulation are also easier to install correctly than rigid boards and require no additional taping or fixings, minimising waste and saving on people-hours needed on a project.
Finally, building with wider cavities gives you flexibility to adapt your specification, without delay to your project, should your usual insulation choice become unavailable.
An evolving industry
Stricter regulations and a greater awareness of thermal, fire safety, and environmental credentials, mean housebuilders have a lot of boxes to tick. We’ve also seen a clear movement in the industry towards regulating embodied carbon and non-combustible materials in all buildings. Creating homes with 150mm cavities will help you meet the necessary requirements today and futureproof buildings for the tighter standards of tomorrow.
For further information on Knauf Insulation visit https://www.knaufinsulation.co.uk/