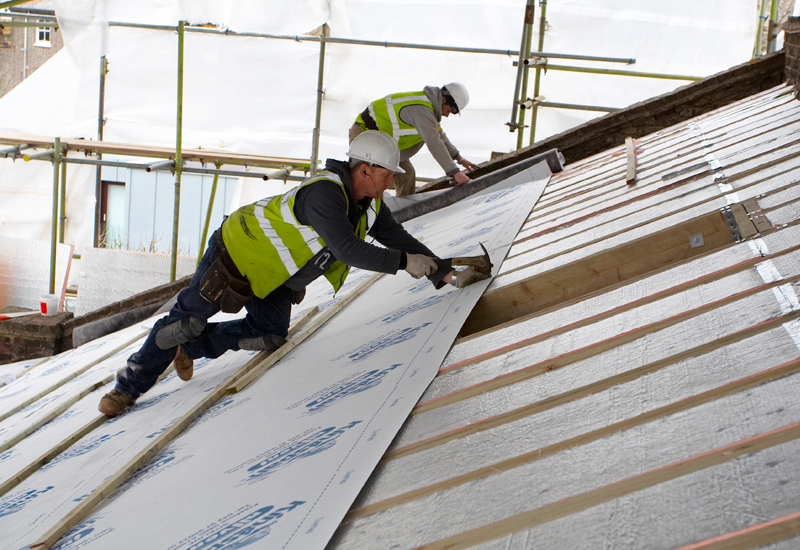
Loft & Found
Kingspan guides you through the insulation of a loft conversion
When it comes to maximising the value of a house, adding a further bedroom or bathroom with a loft conversion remains one of the most sure-fire ways to bring in an extra return. One of the key decisions builders face when carrying out a conversion is which insulation to use, as this can not only affect compliance with the Building Regulations, but can also have a big impact on the living space within the room.
Under the latest version of Approved Document L1B to the Building Regulations in England, the required minimum U-value for pitched roofs insulated at rafter level remains at 0.18 W/m².K, whilst for flat ceilings the minimum is 0.16 W/m².K.
In addition to achieving compliance, a well-insulated conversion can also help minimise additional heating requirements and CO2 emissions. Home owners should not only see the financial benefit of this directly in their energy bills, but also indirectly with an improved Energy Performance Certificate (EPC). Recent research suggests that this can significantly raise the value of a house.
However, insulating to, or above the Building Regulations with traditional products such as mineral fibre can be a pain, with the thicknesses required to achieve the desired performance often exceeding the rafter depth and seriously cutting into the headroom space. The insulation can also sag or slump, resulting in un-insulated pockets, which can in turn lead to thermal bridging, surface condensation and mould growth.
In contrast, rigid phenolic insulation can meet the required thermal performance with a minimal thickness. Unlike some other insulation materials, it has a fibre-free core, is unaffected by air-infiltration and is resistant to ingress from moisture or water vapour. This allows it to maintain its thermal performance throughout the life of the building when correctly installed. Phenolic insulation boards are also lightweight making them easy to install and by selecting a phenolic insulated plasterboard product with an integral vapour barrier, it is possible to further reduce fitting times.
Step by Step
Let’s take a step by step look at a few typical methods for constructing a compliant loft conversion using products from Kingspan’s Kooltherm range of rigid phenolic insulation products. The constructions assume a 125 mm deep rafters at any centres from 400 mm and wider.
- For houses with shared roofs and when the roof covering is not being replaced, the best approach is to install insulation between the rafters with a further layer of insulated plasterboard below. This ‘between and under’ approach helps to reduce thermal bridging through the rafters.
- The Building Regulation requirements can be met by installing 100mm Kingspan Kooltherm K7 Pitched Roof Board between rafters and 39.5mm Kooltherm K14 Insulated Plasterboard below. As the space between rafters may vary it is essential to measure each gap before cutting to ensure a tight fit. Any gaps are filled with an expanding insulated foam and / or flexible sealant.
- Where a non-breathable sarking material such as felt is used, a ventilation gap of 50mm is required above the Kooltherm K7. To maintain this gap and ensure the board is flush with the bottom of the rafters, timber stop battens can be nailed to the rafters at the appropriate depth.
- The plasterboard is then fitted with the long edge running horizontally across the rafters, lapping by at least 20mm at joints. The boards are fixed in place with drywall screws at a maximum of 200mm centres, and no less than 10mm from the edge of the board at bound edges (paper bound) or 13mm from non-bound edge. Screws should be long enough to penetrate at least 25mm into the joist without being overdriven.
- To meet the U-value requirement of 0.16 for areas of flat ceiling, 75mm Kooltherm K7 is fitted between joists and 69.5mm Kingspan Kooltherm K14 is added below using the same installation approach.
- For dwarf walls 50mm Kooltherm K12 Framing Board is installed between timber studs and 29.5mm of Kooltherm K14 on their inner face.
- When re-roofing a detatched property it is best to insulate using a “between and over” approach. For pitched roofs 50mm Kooltherm K7 Pitched Roof Board is installed between the rafters using sarking clips driven into the top of the timber at 1 meter centres to hold them in place.
- A further 60mm of Kooltherm K7 is then installed over the rafters with care taken to ensure that any joints on boards running from the eaves to ridge occur over rafters. A breathable sarking membrane such as the company’s Nilvent is then overlaid and the boards can then be held in place with counter battens (38mm x 38 mm).
- For enhanced airtightness with this arrangement a further breather membrane can be added between the two layers of Kingspan Koolthem K7, with all joints or gaps sealed using airtight tape.
For further information on Kingspanvisit www.kingspan.com