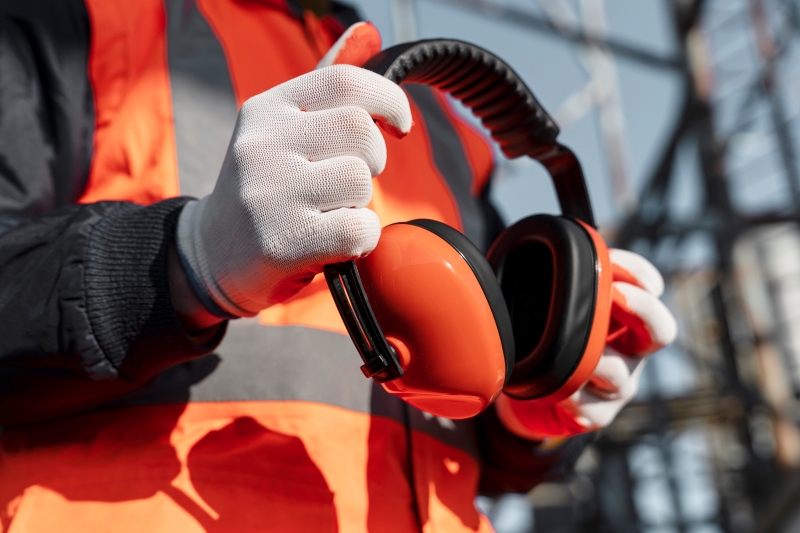
Construction workers are being reminded of the importance of hearing protection.
Noise-induced hearing loss is the most common preventable occupational health condition in the world, however in construction one in four noise-exposed workers have a material hearing impairment, and seven percent of all construction workers have tinnitus.
Phoenix Health & Safety have teamed up with Boots Hearingcare to share why construction workers are at risk of ear health damage, and what preventative measures should be put in place by safety professionals.
Recent research conducted by Boots Hearingcare found that those in construction are at high risk of hearing loss, with the industry ranking as the 5th noisiest profession with an average sound level 99.3dB.
Explaining what this means, Hannah Samuel, Audiologist at Boots Hearingcare said: “When it comes to noise levels, consistently being exposed to anything measuring more than 70 dB (decibels) can start to cause damage to hearing after two hours of constant noise.
“Average dB levels this high indicate the clear risk construction workers face by working a full day on-site. If not wearing suitable and proficient ear protection, over time this can cause long-lasting, irreversible damage such as tinnitus and early hearing loss.”
Nick Higginson, CEO of Phoenix Health & Safety, shares 3 steps safety professionals should take in order to safeguard their workers.
1. Provide suitable protection and warnings
Nick states: “The risk to employees’ hearing depends on the frequency of exposure, and the sound level in decibels (dB). A sound level of 80 dB can be harmful if exposure is regular, and that’s not much noisier than a vacuum cleaner, so Health & Safety professionals in most industries will need to assess and manage risks appropriately.
“In noisy areas, for example, it is important to identify hearing protection zones which are sign-marked areas where it is compulsory to wear hearing protection.”
2. Ensure staff training is up to date
Nick explains: “Hearing protection is only useful when worn correctly, therefore employees must receive the adequate training and information that they need. Taking an accredited, industry-standard course such as the IOSH Working Safely Course will help employees to understand how to work safely to protect themselves and others.”
3. Utilise technology for noise monitoring and mitigation
Nick shares: “Technology such as noise sensors can be connected to a central monitoring system to report on real-time noise levels and notify when these levels exceed predefined thresholds. This allows health and safety, and construction managers to take timely action to mitigate excessive noise and comply with regulations.”
He adds: “Wherever there is noise at work you should be looking for alternative processes and equipment. Companies can invest in modern, quieter construction equipment and machinery, such as electric or hybrid vehicles, or equipment with noise-reducing technologies to help mitigate noise and the effects it has on workers and the environment.”
If you are worried about your hearing, book a free hearing test today at one of Boots Hearingcare’s 400+ locations.