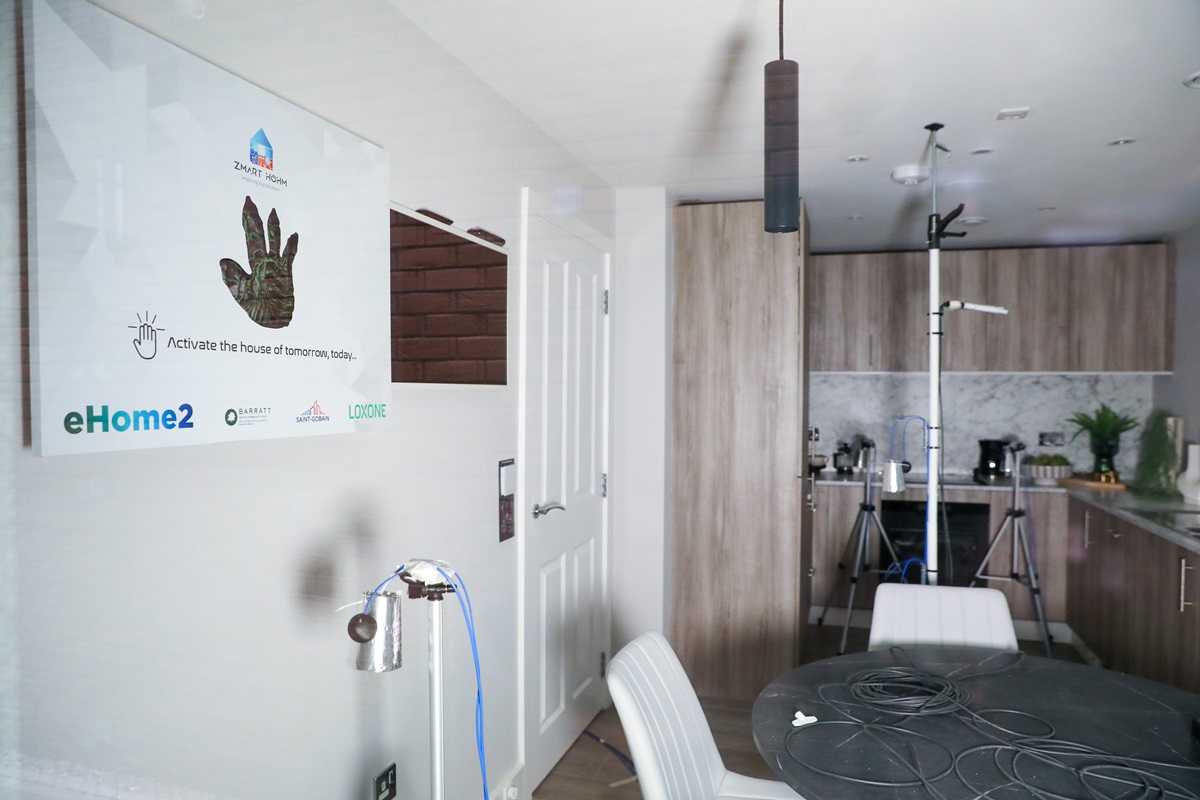
The Future Homes Standard 2025 is one of the hot topics in the construction industry.
Increasing the energy efficiency of our housing stock should be a win-win all round, helping our planet and reducing energy bill costs. It is, of course, not as simple as that though and here is where Energy House 2.0 comes in.
The University of Salford’s research facility has two environmental chambers inside, each able to accommodate two detached houses. Conditions can be controlled in these chambers, with the ability to set temperatures between -20˚C to +40˚C and simulate different weather conditions like wind, rain and solar radiation, as a means of measuring the energy efficiency of the homes inside.
We spoke to Tom Cox, Construction Solutions Director at Saint-Gobain, who is responsible for one of the houses inside the facility – the eHome2. Saint-Gobain worked with Barrat Developments on the eHome2, which was built to try and meet the upcoming 2025 Future Homes Standard requirements and has been subjected to rigorous testing for the past year and a half.
eHome2 was based on Barratt’s Moresby House type with a number of inventive additions from Saint-Gobain added along the way. Tom Cox explains the benefits of the Energy House 2.0: “It was an attractive initiative because it allowed us to push the boundaries in a way you can’t always do on an active site. It’s more focused on delivering a product – which is the house itself – and designing the property around the performance outcomes you want.”
weberwall
One of the products Saint-Gobain was keen to make use of was weberwall from the weber arm of Saint-Gobain. This brick cladding looks just like the traditional building method but is made from 95% minerals bound in cross-linked polymers and just 4-6mm thick.
Tom explained the benefits of the weberwall system in an amusing anecdote: “While the Bellway house next door used a traditional brick skin, we used a brick slip skin (the weberwall system) and when the two deliveries came in to apply the fabrics, we saw the traditional brick skin came in 26 pallets full of bricks. The weberwall system, with the render board and the components, effectively came in in the back of a Transit van.”
“We had a palette of backing board, which was British Gypsum and GlassRock and then half a pallet of render for the first floor, half a pallet of brick slip, which was the weberwall system for the ground floor, and the product went up very, very quickly.” In addition, where the Bellway team’s traditional brick skin took two weeks to go up, the eHome2 was wrapped and watertight in three days.
Tom continues: “So you’ve got these real productivity gains in terms of the labour required. Obviously, we all know about labour shortages in the UK, specifically in the bricklaying sector where the average age of bricklayers is going up and the amount of people going into the trades is going down. That’s an equation that doesn’t work in the long term.
“We are addressing that issue but, at the same time, focusing on getting the embodied carbon down through a reduction in overall material volume and the loading on the foundations. The design required shallower footings, with less concrete to carry the weight of the house above, and that means less raw material content.”
Positive learning
The University of Salford’s testing results for eHome2 have been very positive, with the house exceeding the Future Homes Standard air tightness requirement and a heat loss coefficient within 3.8% of the designed value.
One of the more valuable things for the Saint-Gobain team though was seeing what hadn’t gone entirely to plan and where they could improve. Tom explains: “We did find pockets where the wall panel installation had been compressed in the manufacturing process and there was a knock-on effect on the U value.
“For us it’s a massive learning curve to really look at the quality control in that part of the factory to ensure that the insulation being installed as it should be. As we drive towards the Future Homes Standard we are going to have to start to understand and accept that houses will be designed and delivered with very different thinking. It’s not just a combination of components to meet Building Regulations and the output is the output you get, it’s designed around what the output needs to be and then reverse engineering that back to the individual components”.
For further information on the Energy House 2 project click here
If you would like to find out more about weberwall click here
Listen to our exclusive interview with Tom Cox, Construction Solutions Director at Saint-Gobain, on an episode of the Professional Builder Podcast. Click here to tune in