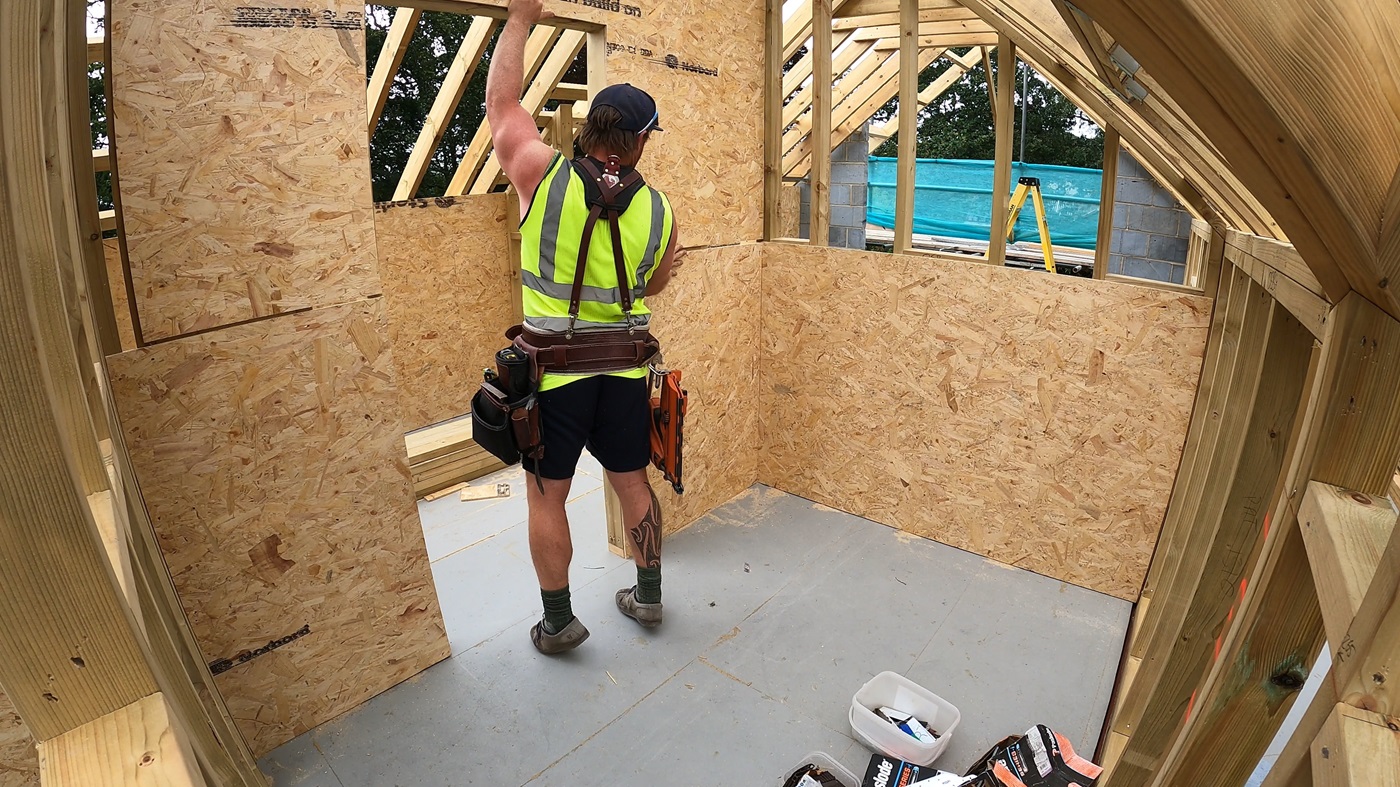
Popular with sailors and surfers, Mudeford lies on a spit of land between Christchurch Harbour and the open sea, where residential properties rival Sandbanks in nearby Poole in terms of luxury and prestige.
One of West Fraser’s customers, in a redevelopment project, is employing the company’s high performance panel products where a building is being transformed into a three-storey, five-bedroom dwelling with a rooftop sun deck.
The team carrying out the work for a private owner includes Steve Mayes who has gained a lot of experience of the West Fraser product range working for local developers, Glass Harbour Group and Ashhaus Construction: building bespoke, high specification homes. As Steve explained: “On a lot of our projects, the architect’s drawings will specify the use of a certain thickness of chipboard or another panel product, but we tend to buy West Fraser’s SterlingOSB Zero for its quality and reliability.
“The property I’m working on at the moment in Mudeford dates from the 1960s and is undergoing a full renovation as well as additions, so that it will have five bedrooms all en-suite, including the master which measures ten metres by seven. There are some new blockwork walls as well as a couple which are retained, while we are building studwork partitions on the upper floors. The roof, however, is far from conventional with two gables separated by a seven metre long ‘table-top,’ which has great sea views and is going to have a hot tub. This is being built off cranked steels infilled with 7 x 3 timbers and 7 x 2 rafters carrying a plywood deck.
“This is covered by a vapour barrier and 150mm of rigid foam insulation and then 18mm SterlingOSB Zero, which will be waterproofed with an Alwitra flexible single ply membrane. Considering the poor weather we’ve had this year; progress has been good and we are on course to complete in early 2025. Indoors, meanwhile, we are installing CaberDek across timber joists on the first and second floor with noggins fitted where any stud partitions are to be built.
“We also routinely make use of CaberFix glue as well as 50mm ring shank nails to make sure there are no squeaks; the adhesive is applied to the tongue and groove joints as well. We particularly like the ruggedness of the West Fraser boards which means you don’t get any damage to the edges when you are pulling them up over the scaffolding, like you do with some makes, slowing things up. And once you get the first row fixed down, the consistent size avoids the misalignment that creeps in with other decking, which can take a lot of work to correct.”
All West Fraser panel products produced in the UK are net carbon negative and manufactured in mills that have obtained the coveted environmental ISO 14001 accreditation. Responsibly sourced, the panels are FSC certified (C012533) and created from locally grown timber, cutting embodied carbon from transportation.
For further information visit Uk.westfraser.com