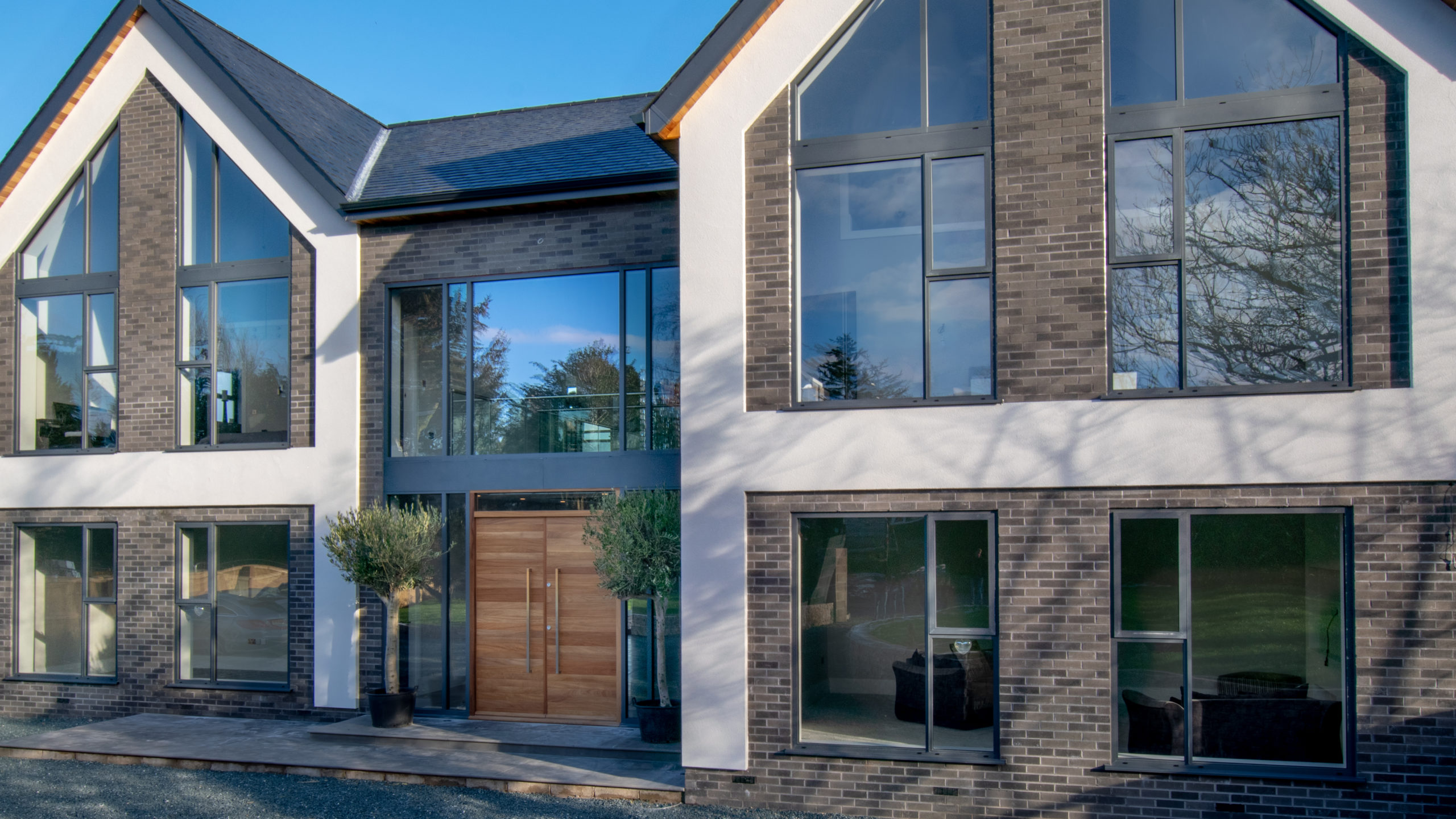
What if your perception of concrete bricks is wrong? Marshalls explains why you should be considering concrete facing bricks
You know the stories, “They’re too heavy and too slow to lay. They don’t cut well. They fade too fast. There’s hardly any choice.” But nothing stands still; concrete brick technology improves. Repeating these false rumours about concrete bricks is like stating cars are dangerous because they don’t have seat belts. It might have been true once, but it’s not true anymore. In addition, believing these stories means you might miss an incredible opportunity to building more sustainably.
Proof of the pudding is in the laying
Marshalls conducted on-site trials using their latest concrete facing bricks. The professional bricklayers who participated said that the difference in weight between the Marshalls concrete bricks and their clay equivalent was not noticeable. In these real-world trials, observers found that productivity was in line with acceptable industry standards of 20-22 courses a day. The bricklayers who took part in the trials also found that the Marshalls bricks were easy to cut and shape using hand tools.
Consistency is key
Marshalls manufacturing process for facing bricks results in greater dimensional accuracy, ensuring a more consistent size and shape between individual bricks and different batches. This regularity makes laying more efficient, as maintaining levels along a course is even easier.
Ageing well is all in the chemistry
Continued development in brick chemistry means that products are colour stable throughout their lifetime. Marshalls can demonstrate this with multiple housing developments that exhibit unfaded brick colour more than a decade after construction was completed. In addition, as the bricks have minimal soluble salt content in the mix design, Effloresence issues are considerably reduced.
A selection to fulfil any requirement
Another benefit of choosing Marshalls facing bricks is the range of finishes and colours. Available in two forms, frogged and perforated. three finishes, stock, sand-faced and vintage (with an additional creased-face variant available soon) and a wide range of traditional golden, red, brown and mixed tone colours. In addition, a wide variety of contemporary monochrome alternatives can be supplied. Bespoke colour permutations are also available. With almost 80 choices, there will be a product to meet practically any planning guideline or architectural design aesthetic.
Why change the habits of a lifetime?
With clay bricks being the housing brick of choice since Victorian times, what has changed – beyond concrete brick technology – that should inspire the industry to reconsider?
Combating climate change is now at the top of everyone’s agenda. International agreements, government guidelines, and industry targets demand a more sustainable response from the built environment industry, which is widely recognised as a significant global contributor to CO2 emissions. Plus, homeowners and buyers are becoming more conscious and demanding. Excellent EPC scores are a priority, and consumer focus is now on carbon footprint and the impact of the entire build process.
Net-Zero 2050 is looming on everyone’s horizon. Housebuilders are trying to achieve their sustainability goals through superior glazing, improved insulation, more efficient white goods, alternative heating technologies and LED light fittings. Larger companies are auditing the supply chain of their fixtures and fittings. But is it enough?
What if considerable and immediate reductions in embedded CO2 could be made simply by your choice of bulk materials? What if a single decision could seriously accelerate your journey towards meeting the industry’s net-zero targets.
Suppose you could still build a house on time and within budget – while meeting technical, aesthetic and planning requirements? If you could trust in a reliable supply of materials to be delivered to site when you expect? The question isn’t ‘Why?’ but ‘Why not?’
Concrete isn’t the problem; it’s a solution
The total lifetime reduction in CO2 derived from choosing Marshalls bricks over traditional clay bricks is 49.1 per cent.
How is this possible
Concrete bricks are cured, not fired in a kiln, so there is a massive reduction in heat energy and fossil fuels required throughout the process. Marshalls produces its bricks across the UK, making sure the supply as close to site as possible, so the carbon footprint of transportation is reduced.
Due to the nature of their composition, Marshalls bricks continue to absorb CO2 over their lifetime. If UK housebuilders switched to Marshalls bricks for all the houses built in one year, the lifetime CO2 savings would be equivalent to taking 300,000 cars off the road or reducing transatlantic flights by 500,000 planes.
To view the Marshalls bricks product range visit https://www.marshalls.co.uk/commercial/bricks-walling/facing-bricks?utm_campaign=pro-builder-editorial&utm_source=probuilder.com&utm_medium=paid&utm_content=editorial