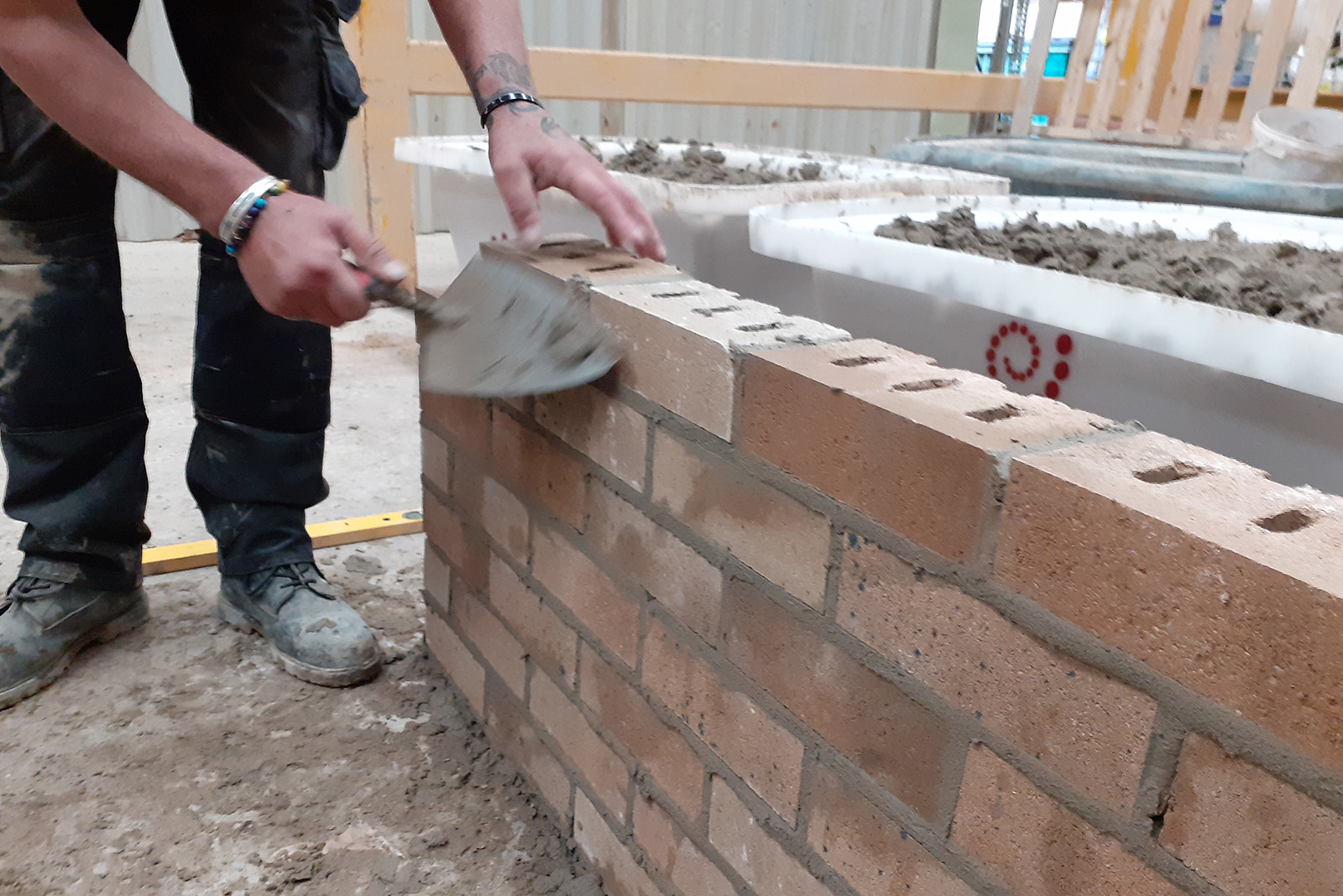
Combating climate change is the great challenge of our age and the way we build is crucial to our success. Professional Builder’s Lee Jones talks to Chris Harrop OBE about what Marshalls is doing to address the issue.
With 97 per cent of the materials that make up the Marshalls product range sourced from these shores the manufacturer is able to conveniently side-step many of the problems the industry is currently experiencing with imported commodities. That’s not the only benefit, of course, because that ‘Made in Britain’ moniker – and the reduction in energy miles it entails – is a considerable advantage in an era when sustainability is at the very top of the agenda, and that’s just one area where the company is keeping a very careful track of its carbon footprint.
As the external landscaping specialist’s Group Sustainability Director, it is the job of Chris Harrop OBE to challenge the business across a whole raft of environmental parameters, and his enthusiasm and engagement with the task speaks volumes for how seriously the company takes its responsibilities. “We’ve been looking at issues of sustainability for more than 20 years now and have been reporting on our CO2 emissions since 2004,” explains Chris. “It was clear then that the issue of climate change, and the future role of building materials and our built environment, would be the industry’s guiding principle and that’s certainly the case. That would then develop in 2008 into a partnership with the Carbon Trust to provide a carbon footprint for each of the products in the Marshalls’ range, and today customers have access to cradle to grave calculations of this kind for over 5,000 products.”
As a result, it can be demonstrated that the carbon footprint of the company’s concrete products has effectively halved over that timescale, and some of the biggest wins have been in the mix. Marshalls has pioneered the use of recycled material, for example, including pulverized fuel ash from the energy sector, a by-product of steel-making in ground granulated blast-furnace slag (GGBS), as well as limestone powder. Each of these can be utilised to reduce the embodied cement content – a CO2 intensive commodity – with no detriment to the functionality, performance, longevity or aesthetic of the finished product. Moreover, with the adoption of 100 per cent renewable energy in its production processes, the reduction of waste through automation – and one of Europe’s most efficient concrete block plants soon to come online – even products that do not include these substitutes have a significantly reduced carbon footprint.
In addition, Marshalls recently launched a new Bricks & Masonry division. A key component of that part of the business is its concrete facing bricks, which can claim just under 50 per cent less embodied carbon content than a traditional clay alternative. Concrete bricks have a very low water and cement content, are made from recyclable material, and there’s no need for firing in a kiln, as there is with clay.
“If more housebuilders were to specify concrete bricks in their projects the carbon savings would actually be huge,” continues Chris. “One interesting fact about concrete is that, thanks to a process of continuous carbonation, it actually sequesters CO2 over the lifetime of the product. If you take the example of paving, for instance, 19 per cent of the CO2 in its manufacture is then reabsorbed. That’s why it’s very important to make any calculations on carbon footprint on a whole life basis. In that context, the durability of a material, as well as recyclability, is significant. Put simply, the longer it lasts, and whether it can be reused, the less CO2 it will ultimately consume. That’s why, in order to ensure that a material can last 50 years and more, our approach to sustainability will equally focus on the likes of compressive strength, UV stability and water absorbency.”
Whilst every manufacturer should, of course, be following the Marshalls example, and doing everything it can to reduce the environmental impact of its current portfolio, it also has to be recognised that we are just an estimated 11 years away from the point at which human activity raises global average temperatures by 1 ½ degrees. Whilst that might sound like a modest increase, it’s more than enough to precipitate disruptive weather patterns. Essentially, regardless of what we do here and now some of the changes are effectively locked in. With flooding and periods of drought more common, water management and sustainable urban drainage schemes will take on much greater importance. Similarly, episodes of extreme heat will bring the urban heat island effect into sharp focus, and the part that building materials can play in ameliorating the threat.
“We’ve been doing massive amounts of research on permeable paving, and that’s reflected in the Marshalls’ solutions now available. With a 100-year storms now likely to occur more frequently, linear drainage channels will need to increase in capacity, rain gardens will become more common as well as a greater overall appreciation of the interface between hard and soft landscaping areas. In a world where water is set to become an increasingly scarce resource, schemes that can capture and utilise it will also emerge as compulsory features.”
Marshalls Driveline Priora is a sustainable urban drainage system that comes in a range of colours, sizes and textures. It’s designed so that water will percolate through the joints, which means that no additional drainage is required – or planning permission. Similarly, urban heat issues are being addressed with a greater appreciation of thermal mass, whilst products are now being designed with their ability to reflect solar heat very much in mind.
“Essentially it comes down to creating better futures for everybody,” concludes Chris. “Whether it’s socially, economically or environmentally, the materials we choose to build with can have a huge impact on our well-being.”
For further information on the range of paving and landscaping products from Marshalls visit https://www.marshalls.co.uk/