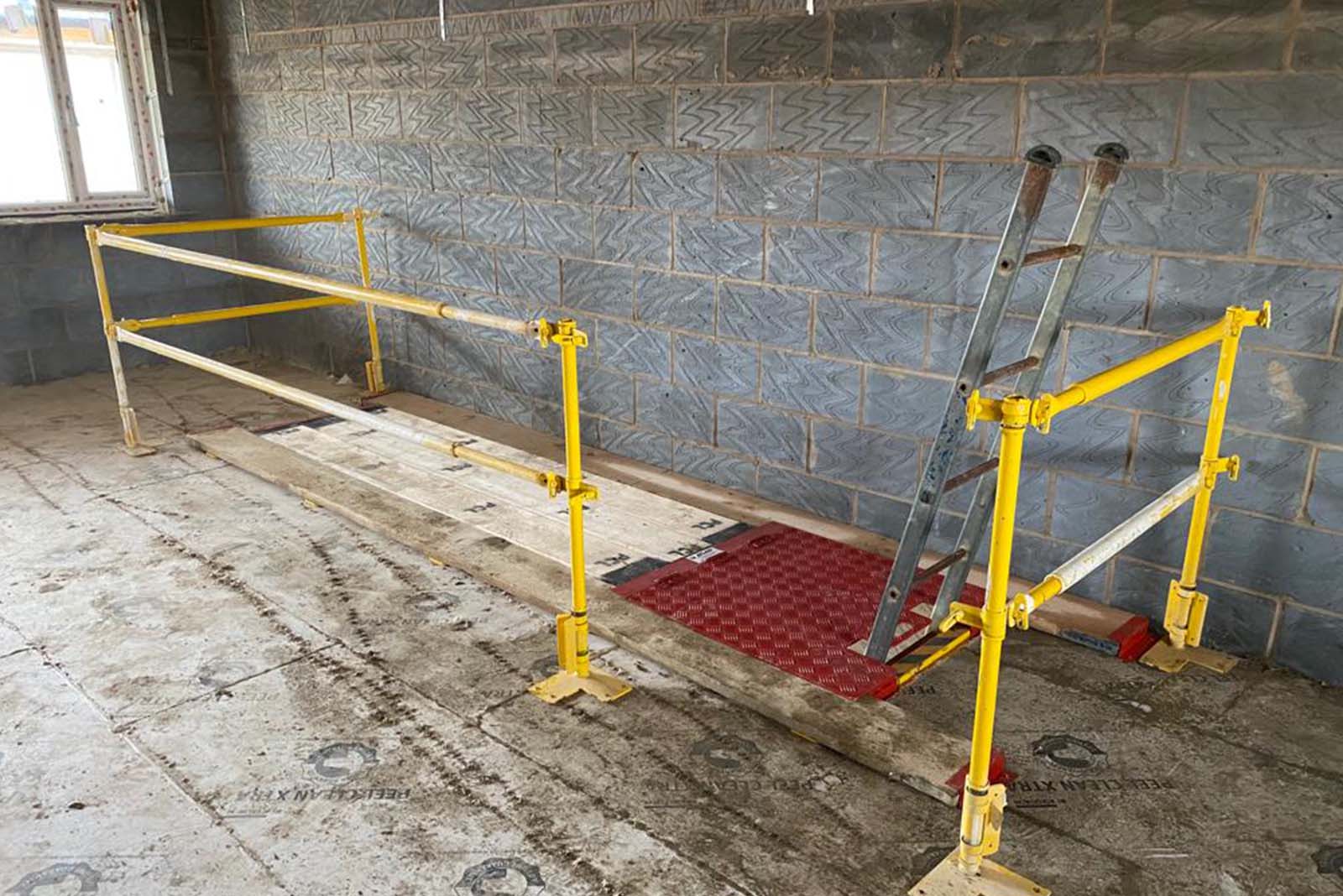
The ASAP (Adjustable Stairwell Access Platform) aims to eliminate one of the on-going safety issues in new build construction, whilst saving time and improving sustainability. Professional Builder’s Lee Jones finds out more.
Many in the housebuilding sector will recognise that second floor stair installation is a high-risk activity of the construction process. The Risk Assessment Method Statement (RAMS) on staircases advises the use of sacrificial joists, flooring, and the addition of the industry standard barrier system for stairwells, but this is often not applied in practice, and the result can be potentially dangerous and/or fatal.
Richard Pearson, the proprietor of Pearson Carpentry, and Operations Manager, Andrew Sims, were unsatisfied with a situation that leaves a hole, not just in the regulations, but in the new build itself. They set about finding a solution that was safer and more productive for their workforce and the result is the ASAP Adjustable Stairwell Access Platform.
The guiding principle behind this product’s design has been safety, and it would then take a further two years to design, build and rigorously test. When it was subsequently introduced to site on the contractor’s own projects, it is a testament to ASAP’s efficacy, that it quickly became a very welcome and standard practice amongst Pearson Carpentry’s onsite teams.
“The system has a safe working load of up to 1,000kg,” explains Keirsten Redmond, a Contracts Manager at the company with over 16 years of experience on the tools. “As the name suggests it will extend to fit a multitude of different stairwells and is fully tested at its maximum range. The assembly and disassembly is simple – with an ASAP video timing installation in under five minutes – and the components can easily be transported between jobs. Whilst a QR code located on the side of the beams will bring up an installation guide on any smart device.”
Add all that up and you’ve not just saved time on your program, but also considerable cost benefits can be accrued into the
bargain. If installed at joist stage, it eliminates the need for any sacrificial joists, as well as the associated joist hangers, flooring, fixings, and labour. Moreover, a bespoke trap hatch allows for easy access and, as a result, the system can then be left in throughout the rest of the build, providing a safer working environment for subsequent trades.
In addition, ASAP can withstand the weight of a birdcage scaffold and reduces the amount of overall waste from a housebuilding project. “The product really comes into its own on a three-storey terraced or semi-detached timber frame builds,” continues Andrew. “In those instances, the party jack walls from ground floor to underside of truss need to be covered with plasterboard. On a threestorey structure, the ASAP removes the additional visits for both the dryliner and the carpenter.”
Ashford-based Pearson Carpentry operates around the south-east and a large part of its business is with national house builders. Owner, Richard Pearson goes on to say: “I believe the ASAP design will become as important as bricks and mortar for national house builders going forward”. Mr Pearson has brought more than 30 years of experience to bear on his ASAP solution, and the result is a product designed by builders for builders, with all the virtues of safety and productivity embedded in the design that you would expect from such experience.
For further information on the ASAP Adjustable Stairwell Access Platform visit https://needasap.co.uk/