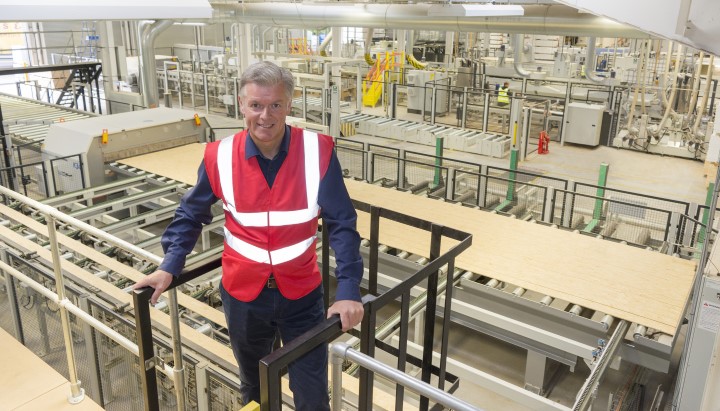
Staircraft is making sure it’s one step ahead of the competition with a significant investment in its manufacturing facilities. Professional Builder’s Lee Jones visits the company’s Coventry assembly line to find out more.
If housebuilders are looking for a supplier that can meet their growing demands then one stair manufacturer can step up to the challenge. Staircraft is already the largest manufacturer of staircases in Europe, with a capacity to supply over 1,400 staircases each and every week, but the product range goes much further, extending to I-joist floor kits, decking systems, and much more. “We are unique in providing an integrated solution that is designed to simplify the build process,” explains the company’s Joe Greenhowe. “Because we supply both staircases and floor kits the two can be designed and made to meet each other perfectly, making it so much easier for the builder on site.”
“That’s just one example of how we’re always looking to do something different but there’s plenty more,” continues Joe. “The joist market overall has changed little from its emergence in the ‘60s but with our bespoke machinery here at Coventry we will not only make the I-joists but cut and camber them to specific requirements, a service which gives us genuine differentiation in the marketplace, because there’s no other manufacturer of joists doing the same. The new I-Joists feature a bespoke OSB web with quality softwood flanges and a unique, strength-enhancing finger joint profile. Our I-Joists are notched in a factory controlled environment, which eliminates the need for perimeter noggings. This joist performance is independently certified by BMTRADA under their Q-Mark scheme and the fire credentials have been verified using the latest European standards as exceeding present UK requirements. These innovations will future proof our offering to the market.”
Professional Builder was treated to a tour of the I-Joist and MDF profile/moulding lines, where the level of investment and innovation is immediately in evidence. In fact, it took the company 12 months to develop the lifting equipment for its I-joists with vacuum lifting specialist Vaculux. Moreover, the Coventry site is the only facility to fit the now standard gap filling and heat insulating end blocks to its joists in the factory. Standard procedure has hitherto been to fabricate these end caps on site, but they will often simply fall off or go missing. Staircraft’s solution is to fit highly visible end blocks to the cut to length I-Joist that can then easily be checked by a site manager, and to model the element to ensure the best thermal performance in situ. Using its own floor design software, Staircraft will also pre-drill service holes of the right size and location for that particular floor, dramatically reducing the opportunity for on-site error and speeding up the process of installing pipework. The production line at Coventry is also the only facility of its kind that can produce cambered timber joists, which improve span performance and are ideal in applications such as roof systems.
The standard TFS-i joist already outperforms all others and improves resistance to fire within the floor void. Since it was founded in 1984, the guiding principle of Staircraft has been to drive building standards upwards, an attitude which is exemplified in the investment in its manufacturing capabilities. The machinery that produces its profiles, for instance, is a completely bespoke installation, turning sheet MDF at one end into a high quality, finished and three coat primed product at the other, which is primed on all four sides.
The new MDF moulding line, part of the west midlands facility, has a capacity for a mammoth 20 million linear metres in a single year. Profiles are primed all the way round with multiple layers, and an extensive process of sanding and denibbing ensures a quality finish. Water-based primers tend to soak into timber and raise the grain, which then requires more sanding and priming. The Staircraft solution pre-heats the timber in an oven achieving surface smoothness far more efficiently. A repeated cycle of heating and priming after each coat then results in the highest quality final appearance. Staircraft are delighted to have achieved number 51 in the 2017 Sunday Times Virgin Fast Track 100 league, an index which ranks Britain’s fastest growing private companies. The significant growth in recent years means Staircraft can now, in fact, boast eight manufacturing facilities across four midlands sites, totalling a footprint of over 200,000 square feet, with the Coventry factory now into its third year of production. In that time the TRU family has also grown in parallel. TRUstair covers stair flight and accessories, and TRUfloorsystems is the umbrella for the I-joist, decking, metalwork and accessory requirements. These were followed most recently by TRUprofile, a range of MDF primed products, and door kits will follow in 2018.
With so many of its products this manufacturer is effectively deskilling the process of assembly for the tradesman, thereby reducing the need for on-site calculation and cutting, with the inherent issues of error and wastage that entails. In fact, Staircraft claims that builders can achieve a waste saving of 80kg per plot by using its unique Well Safe stair well protection system. It’s investment in world class manufacturing facilities is considerable, but it ensures a product is delivered to site to the exact requirements of the project.
For further information on Staircraft click here