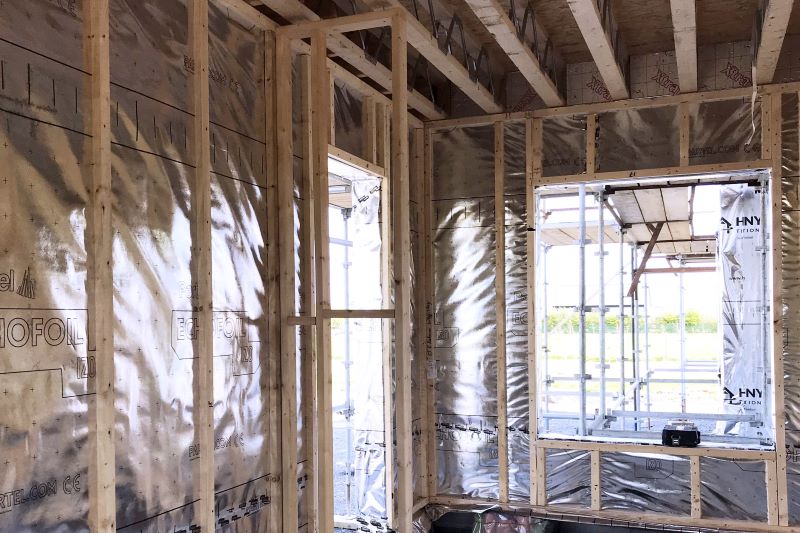
Dara McGowan, Director at Partel looks into passive house design using breathable membranes and vapour control layers
With the UK’s daunting net zero 2050 target enshrined into law, efforts to create practical ‘near zero energy’ houses are essential. With houses accounting for 40% of energy consumed, achieving the means of constructing new passive houses affordably using solutions such as offsite timber frame and lightweight steel frame systems is the realistic way forward.
Faced with spiralling construction costs, off-site construction has potential to be a cost efficient and sustainable alternative to traditional methods of construction. Its benefits are well documented and, while there are still barriers to its adoption, it can provide better working conditions, shorter time on site, and improved environmental performance in the construction process.
The importance of airtightness
Airtightness is a critical feature in Passive House, or any energy efficient home. Airtight membranes are primarily used to form the airtight barrier in passive houses and have several critical roles to play. When a building is not airtight, warm air escapes quickly and is replaced by cold air, which needs to be heated to maintain a comfortable indoor temperature. This is very energy intensive and causes occupant discomfort.
Airtight membranes are also designed to control vapour movement (i.e. Air and Vapour Control Layer – AVCL). By creating an airtight system, we are ensuring water vapour cannot freely move from the internal environment into the building fabric. A great deal of moisture is created in our homes from activities such as cooking, cleaning and showering so it is important that this water vapour does not enter our walls and roofs, where it will cool and possibly condense. By prioritising the building fabric in this way, the passive house approach to design ensures high levels of thermal performance and superior indoor comfort.
Timber frame design
One way to achieve the passive house standard is through offsite timber frame construction as it can provide the ideal fabric for buildings to achieve low energy demands and meet the typical U-value requirements, 0.15 W/(m²K) or below in walls for example. The factory setting enables a greater control over the quality, detailing and craftmanship needed to meet these high-performance building standards. It is also easier to ensure that a structure meets design specifications, and to check it for errors, when standardised and automated processes are used in a more controlled factory environment.
Offsite manufacturers have recently had to respond to the reduction in U-value targets to ensure their system is compliant with new regulations, lower airtightness targets and end user demands for more energy efficient homes. In doing so, many timber frame manufacturers have reviewed their wall build ups in pursuit of an optimised solution. While increasing insulation thickness is the obvious solution to lowering U-values, this is not always cost effective. In addition, it increases the wall thickness which can impact footings, internal floor area and the erection processes.
As an alternative, many manufacturers are exploring the use of reflective foil breather membranes and vapour control layers (VCL). When installed adjacent to a cavity, these membranes enhance the building element U-value – they help timber frame manufacturers achieve compliance with Part L without having to increase stud depth. Reflective foil membranes are designed to perform their primary function (protect against wind and rain, or control water vapour) as well as improve the heat retention of a building element.
When these membranes are installed adjacent to a cavity, they enhance the resistance value (R value) of that cavity – remember, the higher the R value, the better. For example, a typical 25mm unventilated air cavity would have an R value of 0.18 m²K/W (equivalent to less than 5mm of PIR insulation) while the same cavity, when adjacent to one of the Partel ECHOFOIL membranes, has an R value of 0.78 m²K/W (equivalent to more than 15mm of PIR insulation).
Technical support
Regardless of the method of construction, it is important to work with a manufacturer who offers dedicated specification support from U-value calculation and optimisation to condensation risk analysis and assistance with compliance such as meeting with SAP assessors. They can advise you on the most suitable products and calculate a full suite of U-values.
The technical support team can also advise on air permeability testing as the new Approved Document Part L states all houses must be tested. This will provide peace of mind that airtightness backstop will not be exceeded. They also encourage a two-test approach on new wall build ups particularly with regard to the early phase of a new development.
Improving the energy efficiency of our homes on our journey to net zero has never been more important. Offsite methods of construction are a growing part of the market and are seen as one of the most attractive ways of delivering buildings that are high quality, sustainable and cost effective. The development of breather membranes and vapour control layers which offer high performance and can meet new thermal and air permeability targets is set to revolutionise the way timber frame and light gauge steel frame structures are designed and built.
For more information on the Partel EXOPERM MONO DURO 200 a high-performance breather membrane, click here.
For more information on ECHOFOIL IZO Reflective Vapour Control Layer, click here.