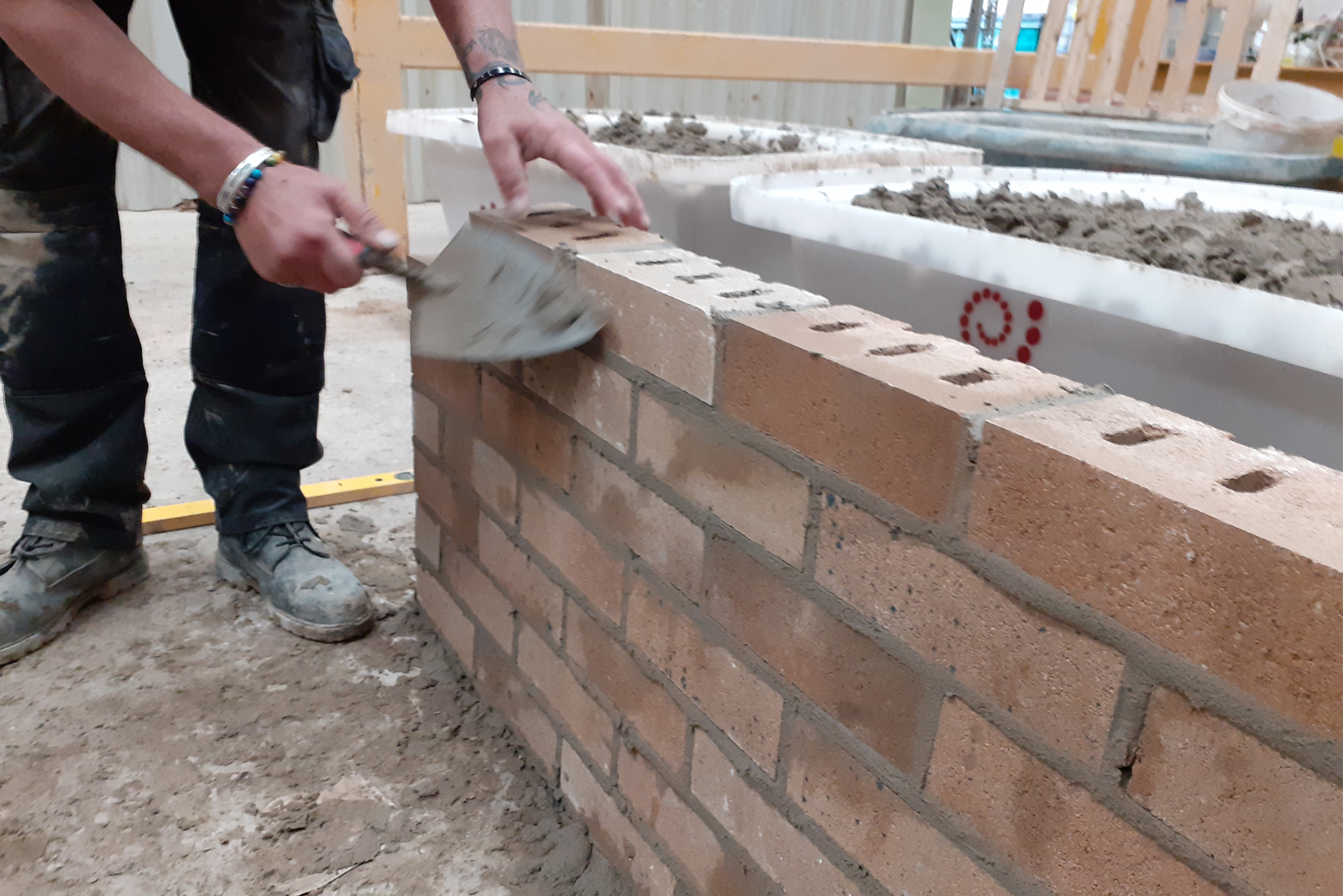
A newly formed division of one of the industry’s most familiar names could herald a new dawn for the concrete facing brick. Professional Builder’s Lee Jones explores what’s available from Marshalls Bricks & Masonry.
It might be the most ubiquitous and traditional of building materials but that doesn’t mean it can’t be improved upon, and one sector of the brick market is proving it can do just that. We live in an age of unprecedented demand for new housing delivery at speed, but it is equally imperative that they are produced sustainably. A product that scores on both counts is the concrete facing brick, and a company that can already point to a pedigree of over 100-years in the walling sector is championing its green credentials.
Marshalls has occupied the hard landscaping market since as far back as the 1890s, and in 2018 acquired Edenhall, a company that has itself been involved in the production of concrete bricks since the 1950s. “Our new division is a result of the merger of Edenhall with Marshalls,” explains Dean Harris, Managing Director, Marshalls Bricks & Masonry, “and what that means for our customers is a larger product offering. That now extends to blocks, engineering bricks (including a perforated version launched in February), facing bricks, recon walling, and architectural cast stone. Add to that the rest of the Marshalls portfolio and that provides a much-increased profile for builders who can now source more of what they need from one manufacturer.”
Edenhall had already led the way in the industry, with the introduction of the perforated concrete brick in 2015, and that’s a journey that is now accelerating. Marshalls continues to supply concrete bricks in a solid format when required, but the development of perforated products has helped further advance their user friendliness for bricklayers. In addition, the strength, durability and aesthetic credentials of concrete bricks are all qualities that the industry is waking up to, and there are a number of other advantages besides. Lead times on concrete bricks are typically shorter than their clay counterparts, for example, whilst all of Marshalls’ Brick & Masonry production facilities – and the raw materials they utilise – are based in the UK, further reducing the impact of their manufacture on the environment.
These are bricks that tread with a lighter carbon footprint at every stage, and the sustainability arguments for their use are compelling. “The environmental benefits of the product speak for themselves,” enthuses Dean, “and can be a key component in helping contractors meet their own carbon reduction targets. Our concrete bricks have a very low water and cement content, are made from recyclable material, and there’s no need for firing in a kiln, as there is with clay. Not only that, thanks to the continuous carbonation during the lifetime of the product, the products are a net absorber of CO2 and, once crushed, they are themselves fully recyclable.”
In fact, a Marshalls brick typically has just under 50 per cent less embodied carbon content than clay. In 2019 the UK housebuilding industry built approximately 195,000 homes, making use of 1.4 billion bricks, 91 per cent of which were clay. Given that significantly less carbon is used in the manufacture of concrete bricks, making the switch would result in some prodigious improvements in environmental performance. Indeed, Marshalls own calculations have revealed that replacing all of the clay bricks currently used with concrete alternatives in one year of housebuilding would equate to removing 300,000 cars from our roads, or reducing transatlantic flights by 500,000 planes.
It is these sustainability selling points which are supported by further gains in their use. All the facing brick products are fully frost resistant (equivalent to clay F2), which means they can be used continuously below and above ground and, because the level of soluble salts is much lower in concrete bricks, the problem of efflorescence is largely eliminated.
New product development continues apace with the launch of a perforated engineering brick which is equivalent to the Class B products already in the market, and is available in red or blue. All Marshalls bricks are through coloured, and include the contemporary shades in white, creams, blues and greys that are becoming increasingly popular with designers, as well as the more standard options.
The Marshalls Bricks & Masonry division also encompasses the recon walling products across the Edenhall Darlstone, Thistlestone and Cromwell brands. Moreover, its architectural cast stone offering is a bespoke solution where the manufacturer will work with its customers on specific designs.
“We have made significant gains in recent years with concrete facing bricks,” concludes Dean, “and it’s a product that is now making real inroads into the market. We want to provide not just a quality product but a level of communication that supports it. That’s why all of our solutions are backed up with full technical support, including advice and guidance from design through to completion.”
For further information on the products available from the Marshalls Bricks & Masonry Division visit https://www.marshalls.co.uk/