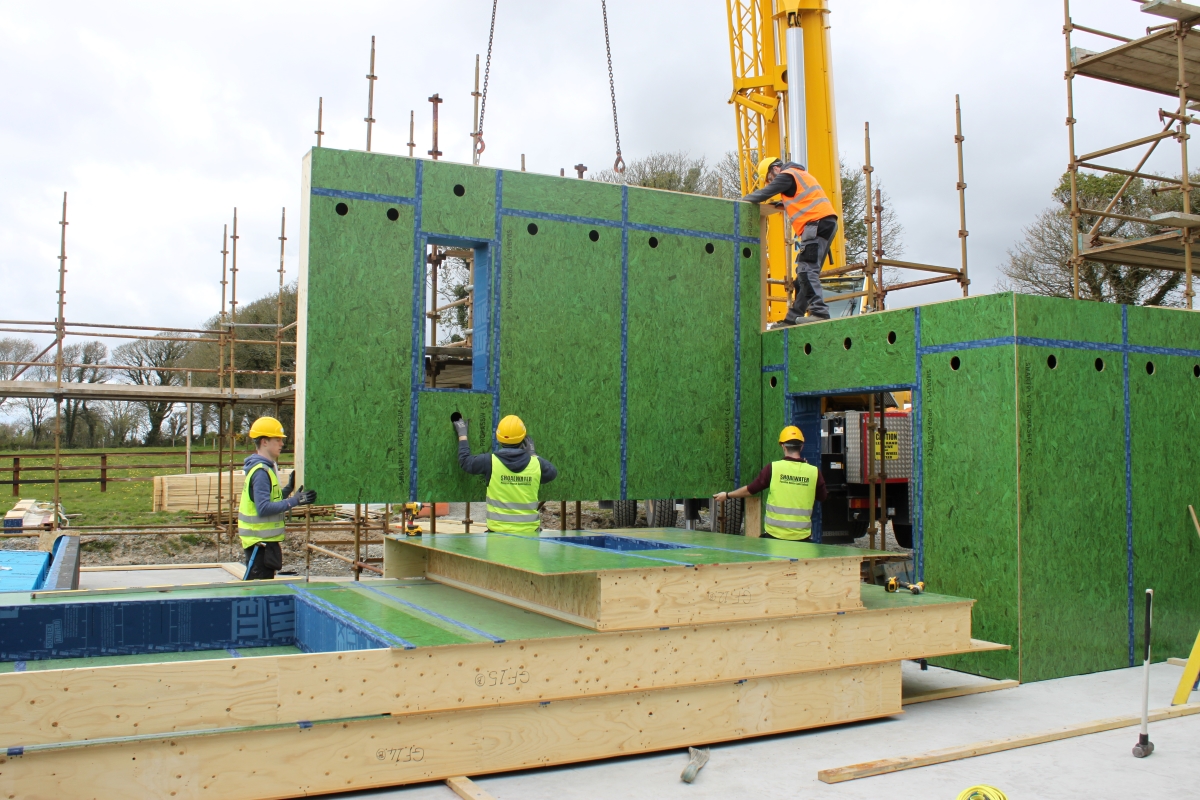
Roly Ward, Head of Business Development at Medite Smartply outlines how we can keep up with housing needs using thoughtfully engineered panels
New research from the Institute for Fiscal Studies (IFS) shows that England has struggled to build houses where they are most needed due to overly restrictive planning rules. This comes as the new Labour government embarks on a major housebuilding push, setting an ambitious target of building 1.5 million homes over the course of the next parliament.
However, across England, the total number of properties between 1996 and 2021 grew just 21 percent1 according to the IFS — a rate which is marginally higher than the growth of the adult population over the same period. Regardless, this figure doesn’t account for regional disparities, with the rate of housebuilding falling behind population growth in some areas of the country.
For instance, in London, the adult population grew by 29 percent between 1996 and 2021 while the number of new properties to house the capital’s growing population increased by just 23 percent. The research from the IFS demonstrates that the housing supply in England is less responsive to changes in demand than that of other comparable economies. Statistically, England’s housing supply was found to be half as responsive to changes in demand as parts of France, Germany and the US.
Clearly struggling to keep up with the housing needs of its growing population, the construction industry must be proactive about taking measures to rapidly increase its housing supply. The use of panelised timber frame systems provides an obvious solution that is both quicker and easier to install than traditional methods, helping to meet the government’s increased aims.
Now more so than ever, as modern building regulations increasingly mandate stricter energy efficiency and moisture control measures, construction professionals must be thoughtful about the materials they use, ensuring their sustainability credentials are up to the task.
Furthermore, the UK Government has proposed revisions to the existing building regulations for new homes. These amendments aim to enhance energy efficiency and minimise carbon emissions, future-proofing new dwellings with sustainable features.
These updated regulations are driving the demand for innovative solutions like airtight and vapour-controlled panels. The new environmentally conscious legislation is especially pertinent since the Department for Business, Energy & Industrial Strategy (BEIS) reported that the residential sector accounted for 19 percent of the UK’s final energy consumption in 20212.
In answer to these developing requirements, the Passivhaus concept presents itself as a viable solution as these homes do not require traditional heating or cooling systems. A key factor in achieving Passivhaus standards is airtightness, which refers to the building shell’s ability to prevent uncontrolled air leakage – a key factor in maintaining thermal comfort and significant energy savings by minimising the building’s heating and cooling demands.
Yet this airtightness must also be carefully balanced with proper ventilation to prevent damp and mould issues, which can arise in poorly ventilated spaces and lead to unsafe air conditions indoors. This is where innovative building solutions such as timber panels with integrated vapour control and air barrier properties come in.
To address these complicated needs, construction professionals need panels that have airtightness engineered into the panel substrate and provide an integrated vapour barrier with consistent vapour resistance over the entire surface, such as SMARTPLY AIRTIGHT. Used as structural sheathing in timber frame structures, such panels also enhance the building’s environmental credentials by reducing its overall carbon footprint.
SMARTPLY AIRTIGHT’s integrated vapour control layer and air barrier properties eliminate the need for additional Air and Vapour Control Layout (AVCL) membranes. The coating also provides a smooth, durable surface for superior bonding of airtight tape at panel joints. This helps to simplify the process of both new build and renovation projects and decreases valuable installation time, which can instead be focused on other important tasks.
Seldom Seen
First Passivhaus in Wiltshire achieved with help from MEDITE VENT and SMARTPLY AIRTIGHT
MEDITE VENT and SMARTPLY AIRTIGHT proved to be a winning combination for the first oak frame Passivhaus to be built in the heart of Wiltshire, southwest England.
Built by award-winning construction company Erigo Developments, Seldom Seen, a private detached residence, was the first house in Wiltshire to meet the Passivhaus standard at the time of completion. It still ranks as only the eighth certified Passivhaus in the southwest of England.
Designed around a traditional oak frame and finished in oak cladding, the house was strategically sympathetic to its rural Area of Outstanding Natural Beauty (AONB) setting.
The combination of MEDITE VENT and SMARTPLY AIRTIGHT helped to achieve its Passivhaus status.
Rebecca Thursby, Director of Erigo Developments commented: “At the time, there was nothing else on the market that fulfilled its role in this location. We used an oak frame to create the external envelope and then choose both MEDITE VENT and SMARTPLY AIRTIGHT to achieve the level of airtightness required to meet the Passivhaus standard. We managed to get the air tightness down to 0.38 ACH @ 50 Pascals, which is very good.”
Find out more about SMARTPLY AIRTIGHT here https://mdfosb.com/en/smartply/products/smartply-airtight.